Rockwell Automation 999 IMC S Class Compact Motion Controller (Cat. No. 4100-999-122) User Manual
Page 138
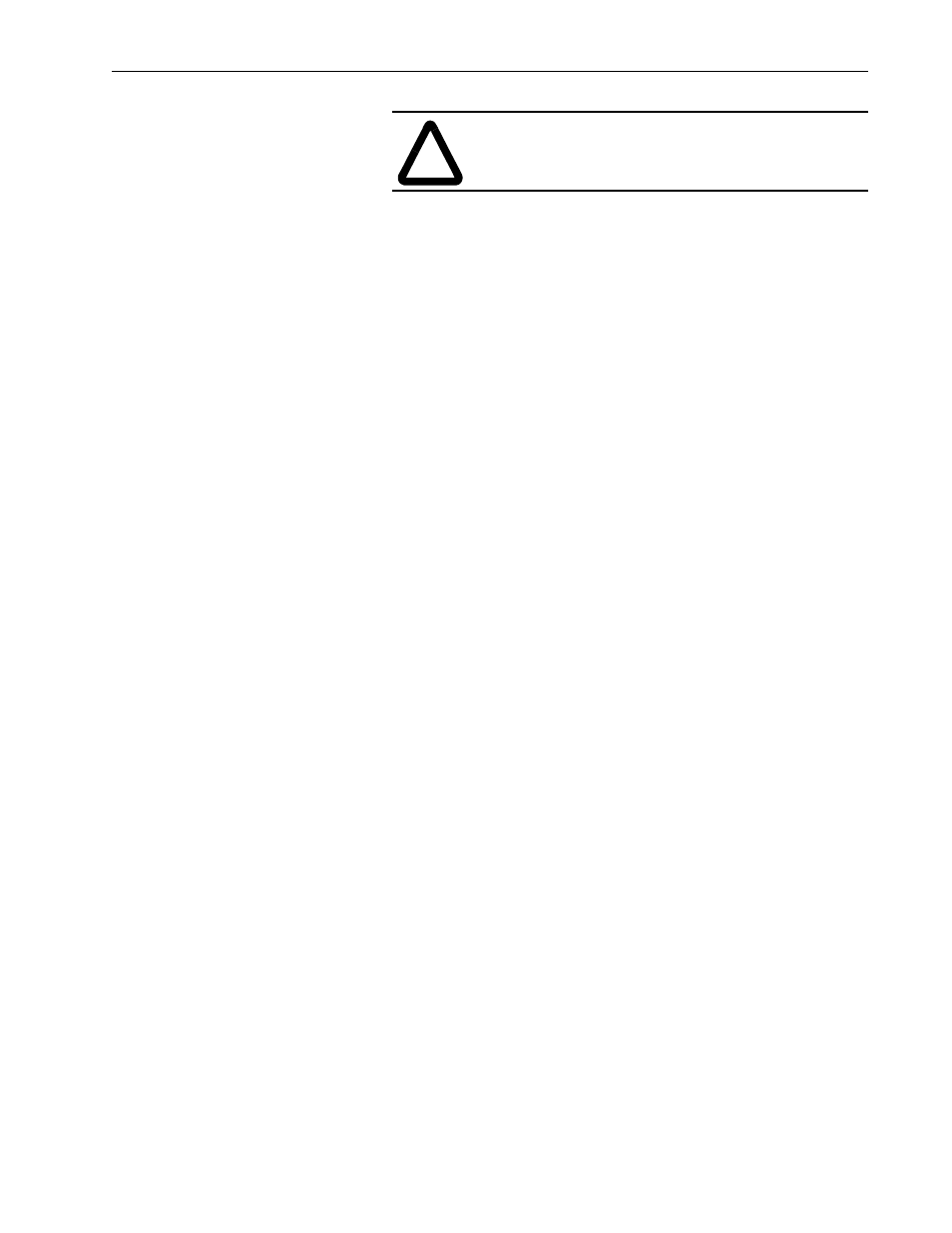
5-58
Understanding IMC-S/23x Setups
Publication 999-122 - January 1997
To change the analog output value, enter the desired new value and
press ENTER. Verify that the specified output is producing the
specified output level.
Servo Setup Menu
The IMC-S/23x provides a sophisticated automatic tuning routine
which allow it to determine proper settings for the servo loop
parameters for each
SERVO
axis. These include not only the P, I, V, and
F gains, but also the maximum acceleration, deceleration, and velocity.
The values determined using the automatic tuning routine may also be
reviewed and edited (changed) if desired.
Usually, the servo loop parameters need only be tuned once when the
motion controller is first integrated onto the machine or when the
machine is being commissioned at start-up. However, if the load on any
axis changes significantly or if the motor or servo amplifier are replaced
for any reason, it may be necessary to re-tune the servo loop parameters.
The Servo Loop Gains
The IMC-S/23x uses a Nested Digital Servo Control Loop consisting
of a position loop with proportional, integral and feedforward gains
around a digitally synthesized inner velocity loop using velocity gain
for each physical axis. These gains provide software control over the
servo dynamics, and allow the servo system to be completely stabilized.
Unlike analog servo controllers, these digitally set gains do not drift.
Furthermore, once these gains are set for a particular system, additional
IMC-S/23x controllers programmed with these gain values will operate
identically to the original one. A detailed explanation of the servo loop
operation can be found in Technical Overview earlier in this manual.
The units for the servo loop gain terms are shown following.
!
ATTENTION: The analog output test activates the
selected output directly. Ensure that it is safe to activate
the outputs before running this test.