Rockwell Automation 999 IMC S Class Compact Motion Controller (Cat. No. 4100-999-122) User Manual
Page 151
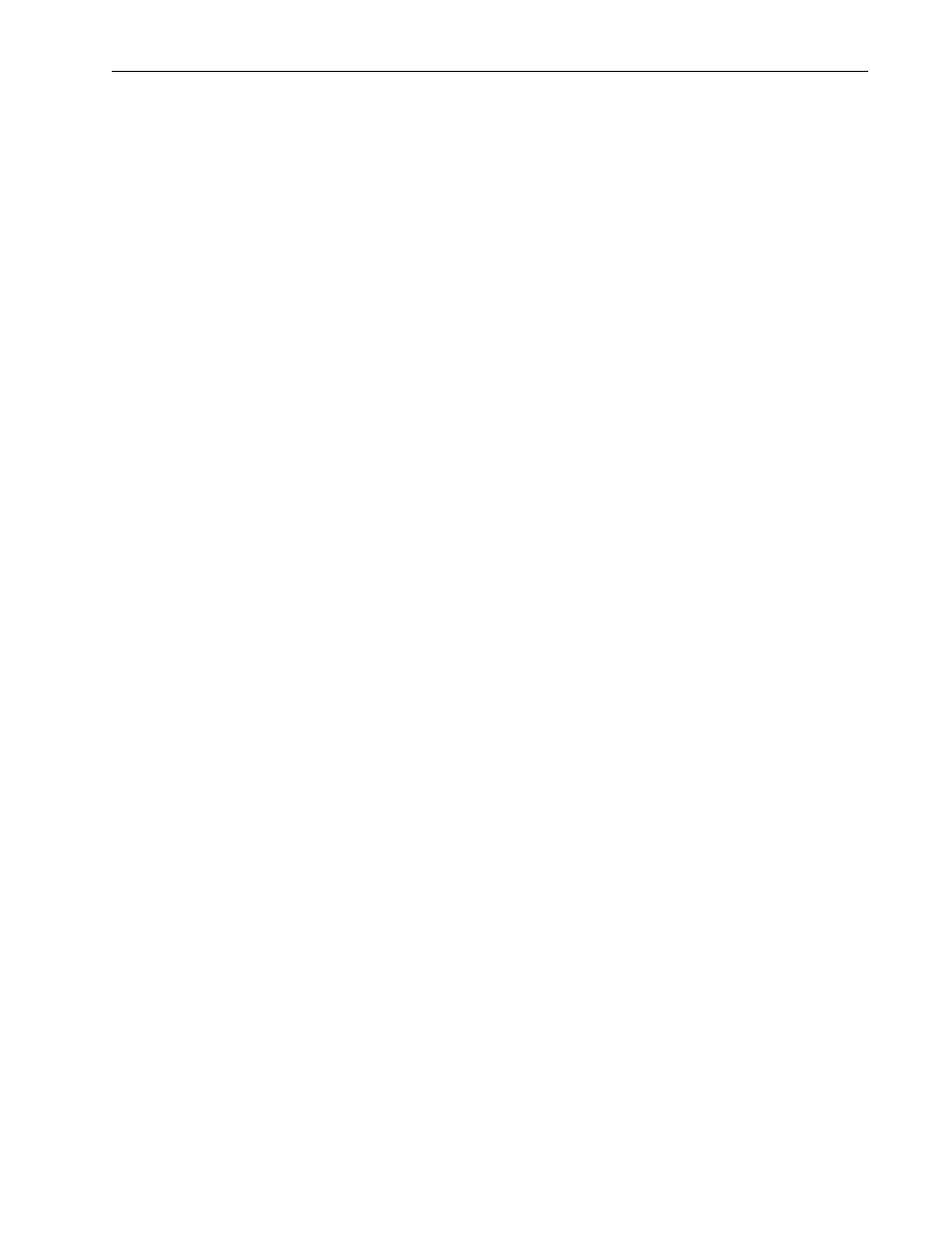
Understanding IMC-S/23x Setups
5-71
Publication 999-122 - January 1997
Setting the Integral Gain
Once the proportional and velocity gains have been tuned or set as
explained above, small amounts of integral gain may be added to
improve static positioning accuracy. If you are using an analog velocity
loop servo amplifier, set the integral gain to zero–most analog velocity
loop servo amplifiers will not tolerate any amount of integral gain
without producing severe oscillations. With a digital velocity loop servo
amplifier, the velocity integrator in the amplifier must be disabled to
use I gain in the motion controller.
If you are using a torque (current) loop servo amplifier, set the I gain
using the formula below.
I Gain = 250 x (P Gain)
2
Alternately, increase the integral gain starting at 0 until the motor
sustains oscillation for a few seconds or more. The optimal I gain value
is about 50% of this value. Notice that as the I gain is increased, the
system becomes "tighter" at standstill, but also tends to become more
unstable or "jittery". In general, the smallest integral gain value that
gives a reasonably tight system without excessive jittering at standstill
is best. Too much integral gain causes severe instability!
If you are converting the integral gain from a basic (IMC-S/20x) or
integrated (IMC-S/21x) IMC S Class motion controller, calculate the
equivalent I gain for the IMC S Class Compact (IMC-S/23x) using the
formula below.
Compact I gain = 1,000 x (Basic/Integrated I gain)
For example, if a basic or integrated IMC S Class had previously been
used successfully on this axis with an I gain of 0.003, the equivalent I
gain for the IMC S Class Compact is 3.