Rockwell Automation 999 IMC S Class Compact Motion Controller (Cat. No. 4100-999-122) User Manual
Page 126
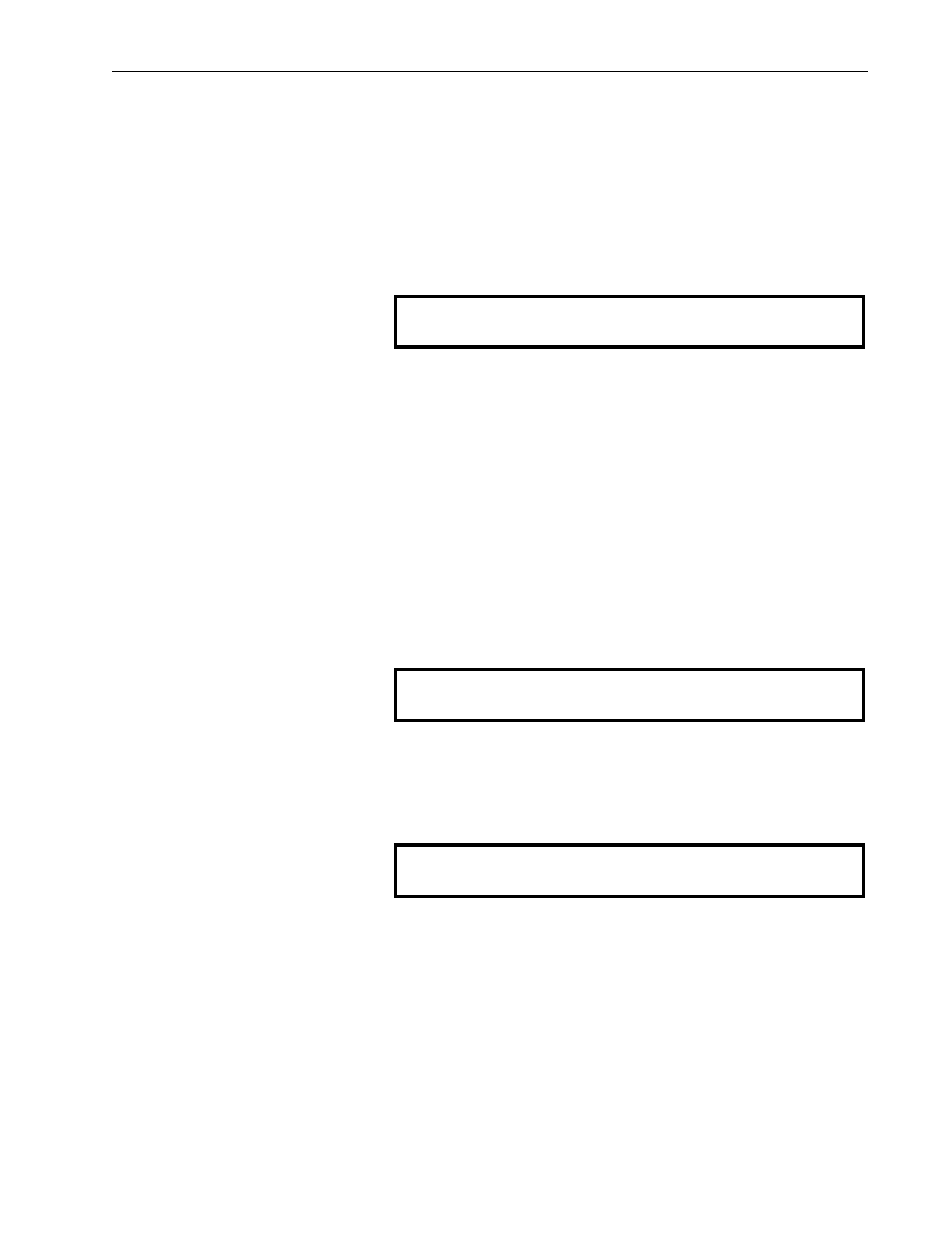
5-46
Understanding IMC-S/23x Setups
Publication 999-122 - January 1997
Loss of quadrature can be caused by physical mis-alignment of the
encoder components, or excessive capacitance (or other delays) on the
encoder signals. Radiated noise problems can usually be cured by
proper grounding and shielding techniques. See the Installation and
Hookup section of this manual for cabling recommendations. After
fixing the problem, re-run the encoder or motor/encoder test.
If the encoder loss detection circuitry noise is activated during the
encoder test, the message
is displayed. An encoder loss condition indicates that one of the
following occurred:
1. Both of the differential signals for any encoder channel (A+ and A-,
B+ and B-, or Z+ and Z-) are at the same level (both high or both
low). Under normal operation, the differential signals are always at
opposite levels. The most common cause of this situation is a broken
wire between the encoder and the motion controller.
2. Loss of encoder power or encoder common to the motion controller
or the encoder.
Correct the problem with the encoder wiring and re-run the encoder test.
Once proper operation of the encoder or other feedback transducer has
been verified, the message
is displayed, indicating satisfactory completion of the encoder test.
If you are running the encoder test because this axis failed the
motor/encoder test, when proper operation of encoder or other feedback
transducer has been verified, the message
is displayed, indicating that the encoder or other feedback transducer
is operating properly and that the problem is in the servo amplifier.
*** Encoder Loss Detected!
*** Check Encoder Hookup and Retest
Hookup OK
Motor/Encoder Polarity Set
*** Encoder Hookup OK!
*** Check Motor Hookup and Retest