Rockwell Automation 999 IMC S Class Compact Motion Controller (Cat. No. 4100-999-122) User Manual
Page 116
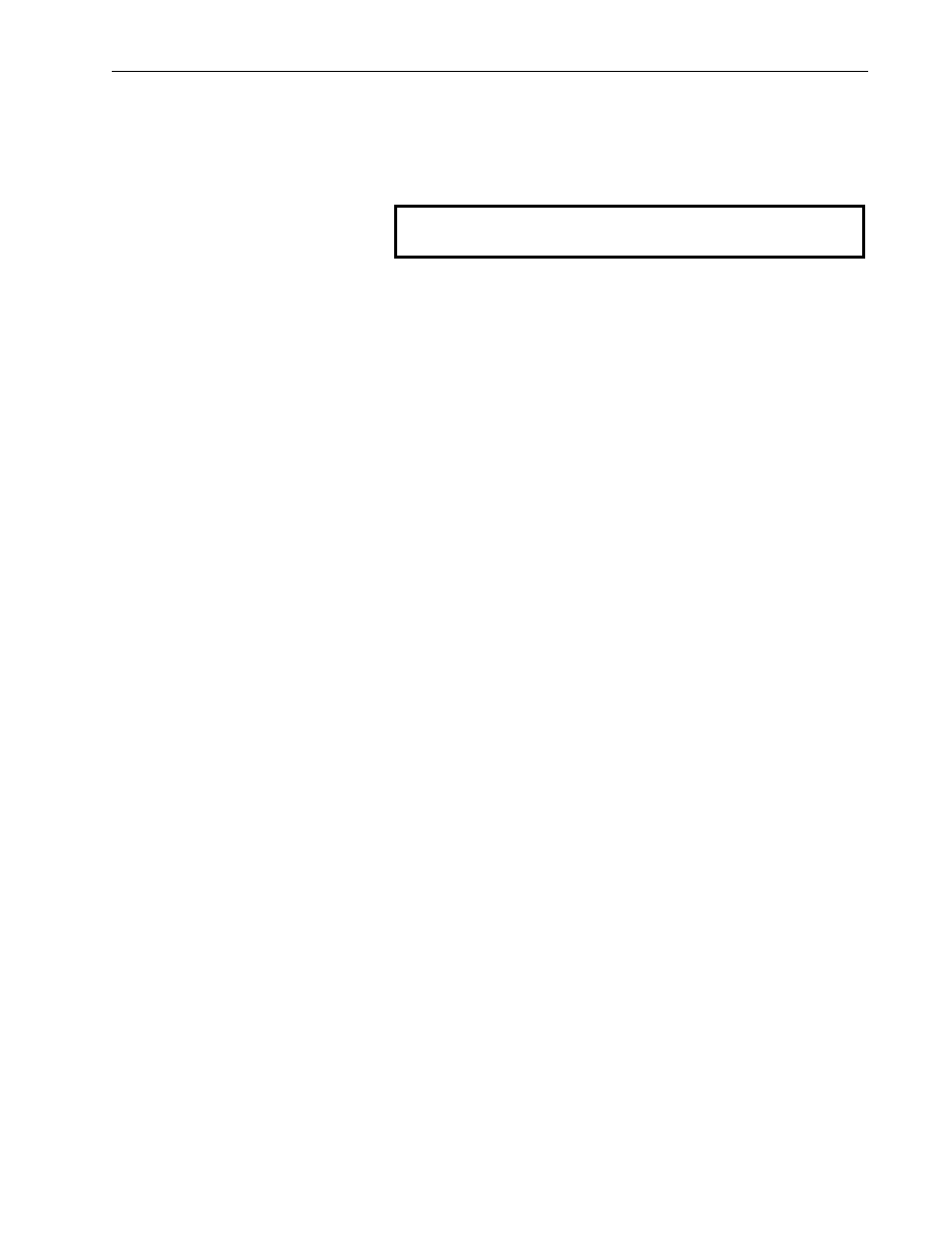
5-36
Understanding IMC-S/23x Setups
Publication 999-122 - January 1997
Editing the Servo
Configuration
Each physical axis of the IMC-S/23x can be configured to interface
with standard servo amplifiers operating in either the velocity (tach) or
torque (current) modes. Next, the following message appears on the
IMC-S/23x:
1. To set up the servo configuration for this axis, toggle to
YES
and
press ENTER.
2. Select the servo drive type that matches the type of servo system
you are using. If a
VELOCITY LOOP
servo drive type is specified,
the software velocity loop (see Technical Overview earlier in this
manual) is disabled.
Dual Loop Control
Dual Loop Control is a special mode of operation–available only if you
have selected
TORQUE LOOP
as the servo drive type–which uses a
separate feedback device to close the digital velocity loop. It is
sometimes useful in applications where accurate positioning must be
achieved despite severe mechanical non-linearities (backlash, slip, gear
ratio variations, etc.) between the motor and the load.
Dual loop control requires two encoders (or other feedback devices)
for each axis, one coupled to the motor and the other to the load. The
encoder on the motor is used to close the velocity loop since tight
coupling is essential for maximum gain and performance of the velocity
loop. The encoder on the load is used to close the position loop, putting
the mechanical non-linearities of the system inside the position loop,
which provides better positioning accuracy.
Note:
The second encoder used for closing the position loop is wired
into another axis. Using dual loop actually consumes two
physical axes on the IMC S/23x.
Edit Servo Configuration? NO