Features – Rockwell Automation 999 IMC S Class Compact Motion Controller (Cat. No. 4100-999-122) User Manual
Page 18
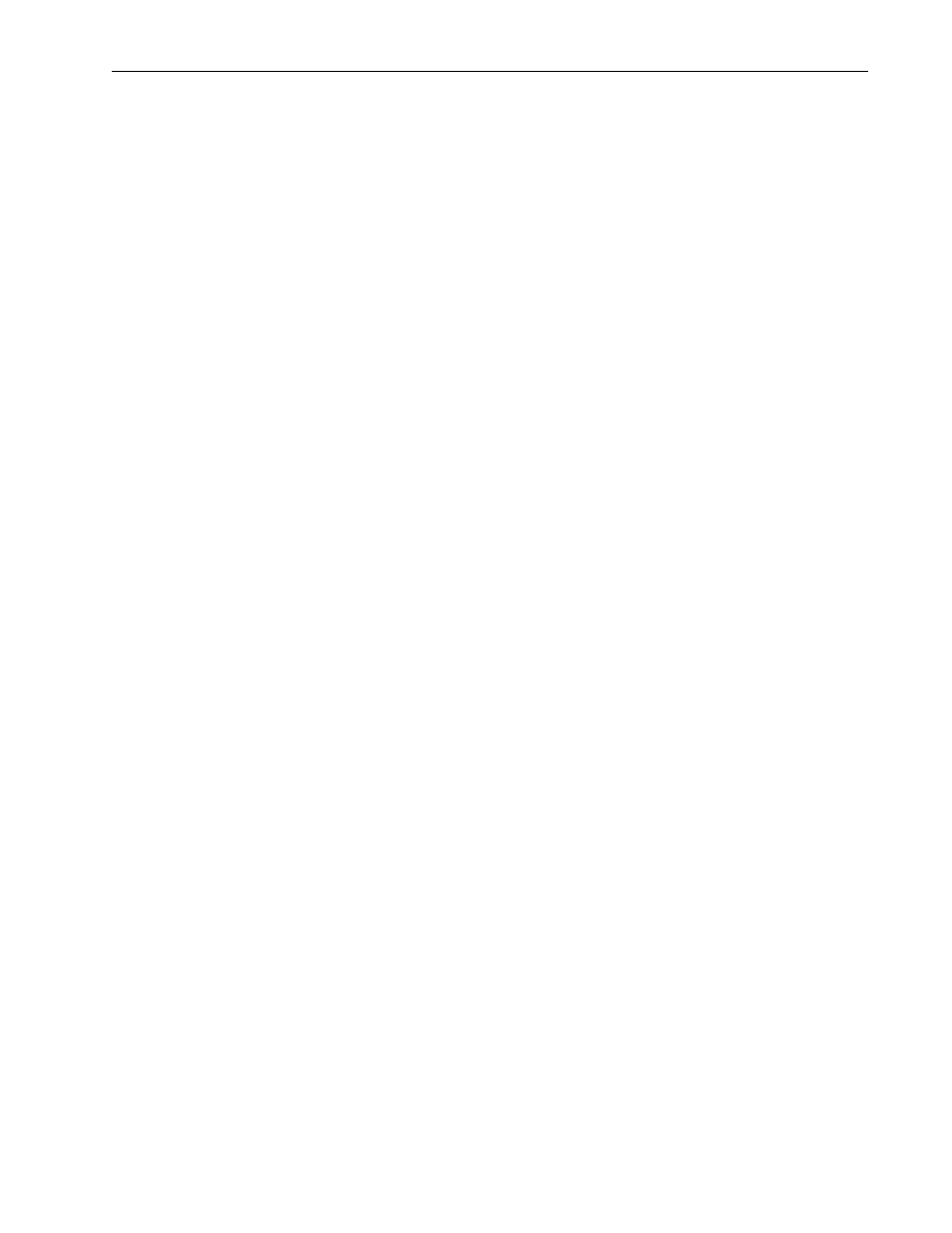
2-2
Introduction
Publication 999-122 - January 1997
A dedicated serial port–which can be field-configured for RS-232,
RS-422, or Allen-Bradley DH-485 communications–is provided for the
man-machine interface (MMI). Connection of the MMI device is via
an AT-compatible DB-9 connector (RS-232 or RS-422) or RJ-45
connector (DH-485), both located on the front panel. If DH-485 is not
used, a multi-unit addressing scheme (Multidrop) allows up to eight
IMC-S/23x motion controllers to share a single RS-422 communication
channel in sophisticated multi-axis systems. The address of each unit
is set by a recessed front panel rotary switch.
The Remote I/O option allows the IMC-S/23x to communicate directly
with an A-B PLC® via Remote I/O using both discrete and block
transfers. The AxisLink option allows axes on other IMC S Class
controllers or ALECs (AxisLink Encoder Converter modules) to be
used as master axes for electronic gearing and cams. This ability
provides real-time coordination for distributed, multi-axis systems in
electronic gearing, cam, lineshaft, and synchronization applications.
Features
•
Powerful graphical software development system (GML) makes
application programming easy and fun.
•
State-of-the-art Intel i960 RISC microprocessor.
•
Fast application program execution (most commands executed in
less than 1
µ
s) ensures highest machine performance and
productivity.
•
Completely digital–no potentiometers or other adjustments
required; will not drift with time temperature or humidity.
•
Multitasking operating system allows simultaneous execution of up
to 10 tasks for efficient utilization.
•
Electronic gearing for synchronization of any axis to another at a
programmable ratio. Ratio may be specified as a floating-point
number of integer fraction (1/3, 3/10 etc.).
•
Electronic cam for coordinated motion profiles on one or more axes.
Profiles may be position versus time or slave axis position versus
master axis position.
•
Sophisticated phase shift and advance/retard capabilities for
electronic gears and cams allows complex motions to be easily
programmed.
•
Auto-registration and auto-correction make high-speed registration
applications easy.
•
Exclusive Imaginary Axis provides additional command-only axis
for precise generation of master motion in master-slave applications
or correction moves in registration and synchronization
applications.
•
Concurrent, independent, or synchronous motion on all axes.
Interpolated motion on up to three axes.