Rockwell Automation 999 IMC S Class Compact Motion Controller (Cat. No. 4100-999-122) User Manual
Page 152
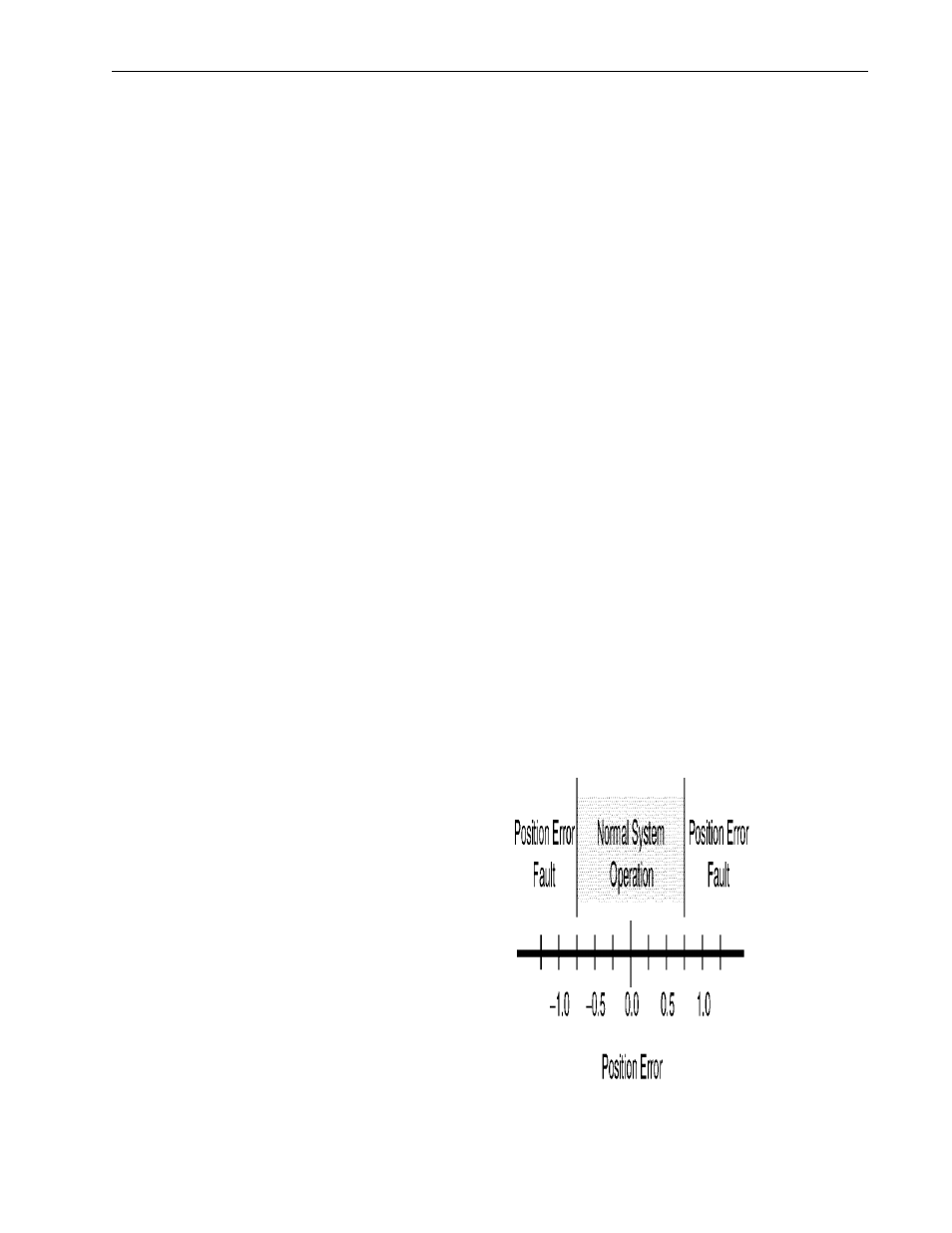
5-72
Understanding IMC-S/23x Setups
Publication 999-122 - January 1997
Setting the Feedforward Gain
If near-zero position error over the entire speed range of the axis is
desired, set the feedforward gain at 1.00 to achieve this. If necessary,
the F gain may be "tweaked" using the Watch Window in the Online
Manager in GML to monitor the position error of the axis during a
move. Increase the feedforward gain until the following error at
constant speed is as small as possible, but still positive. If the
following error at constant speed is negative, the actual position of
the axis is ahead of the command position (see Technical Overview
earlier in this manual). If this occurs, decrease the F gain such that
the following error is again positive. Note that reasonable maximum
velocity, acceleration, and deceleration values must be entered to
move the axis.
Setting the Position Error Tolerance
The self tuning routine sets the position error tolerance to twice the
following error at maximum speed based on the measured response of
the axis. In most applications, this value provides reasonable protection
in case of an axis fault or stall condition without nuisance faults during
normal operation.
The Position Error Tolerance parameter specifies how much position
error the IMC-S/23x tolerates before giving a position error fault
(
ERR FLT
displayed in the status field of the Standard Operator
Interface). Like the position lock tolerance, the position error tolerance
is interpreted as a ± quantity. For example, specifying a position error
tolerance of 0.75 position units means that a position error fault will be
generated whenever the position error of the axis is greater than 0.75
or less than -0.75 position units, as shown below: