Rockwell Automation 999 IMC S Class Compact Motion Controller (Cat. No. 4100-999-122) User Manual
Page 118
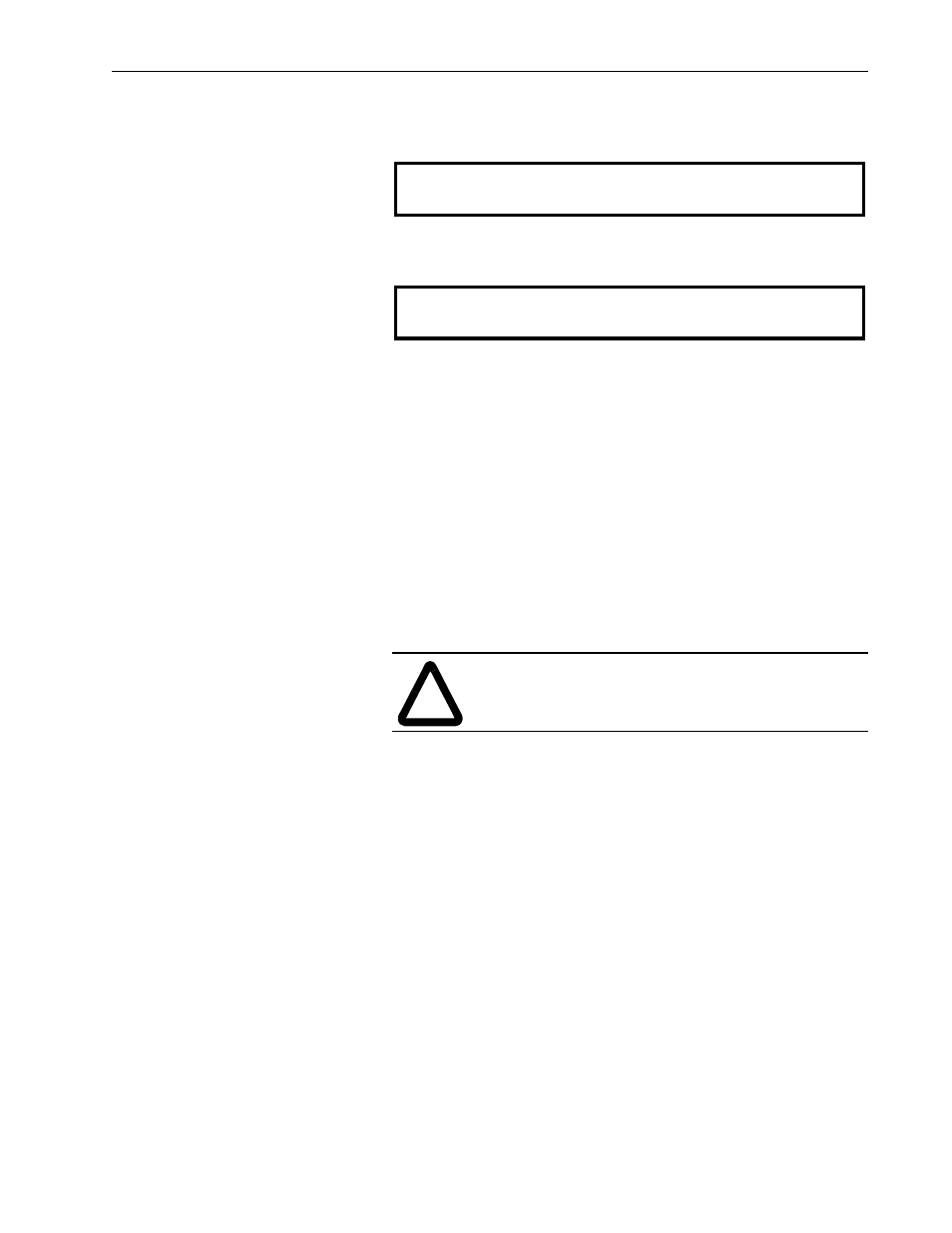
5-38
Understanding IMC-S/23x Setups
Publication 999-122 - January 1997
If you select the axis you are setting up or another SERVO axis, the
message
is displayed and you must select another axis. If you select an AxisLink
virtual axis , the message
is displayed and you must select another axis.
Both the hookup diagnostics and the self tuning procedures work
properly for dual loop axes. It is important, however, that both encoders
be functioning properly before attempting to close the servo loop.
There must always be a physical connection between the dual loop axis
(position loop) encoder and the dual loop velocity axis encoder or it
will not be possible to move the axis correctly. Since the dual loop axis
(position loop) encoder is not normally connected directly to the motor,
this has implications when, for instance, this encoder is driven by the
material fed by a feeder: when there is no longer material driving the
position encoder, the axis will "run away" at a controlled speed until
the position error tolerance is exceeded since it has no position
feedback!
To disable dual loop control for an axis, answer
NO
to the
Dual Loop
Control?
question. You may also need to rewire the encoders since
the encoder mounted directly to the motor (the dual loop velocity axis)
will most likely be the one used for position feedback when dual loop
control is no longer required. In this case, be sure to run the hookup
diagnostics for this axis again to ensure proper feedback polarity and
then run the servo setup routines to establish proper gain values for the
axis after re-wiring the encoders.
!
ATTENTION: When disabling dual loop control on
an axis, be sure to run the hookup diagnostics and the
servo setup routines again to ensure proper operation.
*** This Axis is a SERVO AXIS!
*** This Axis is a VIRTUAL AXIS!