Rockwell Automation 999 IMC S Class Compact Motion Controller (Cat. No. 4100-999-122) User Manual
Page 105
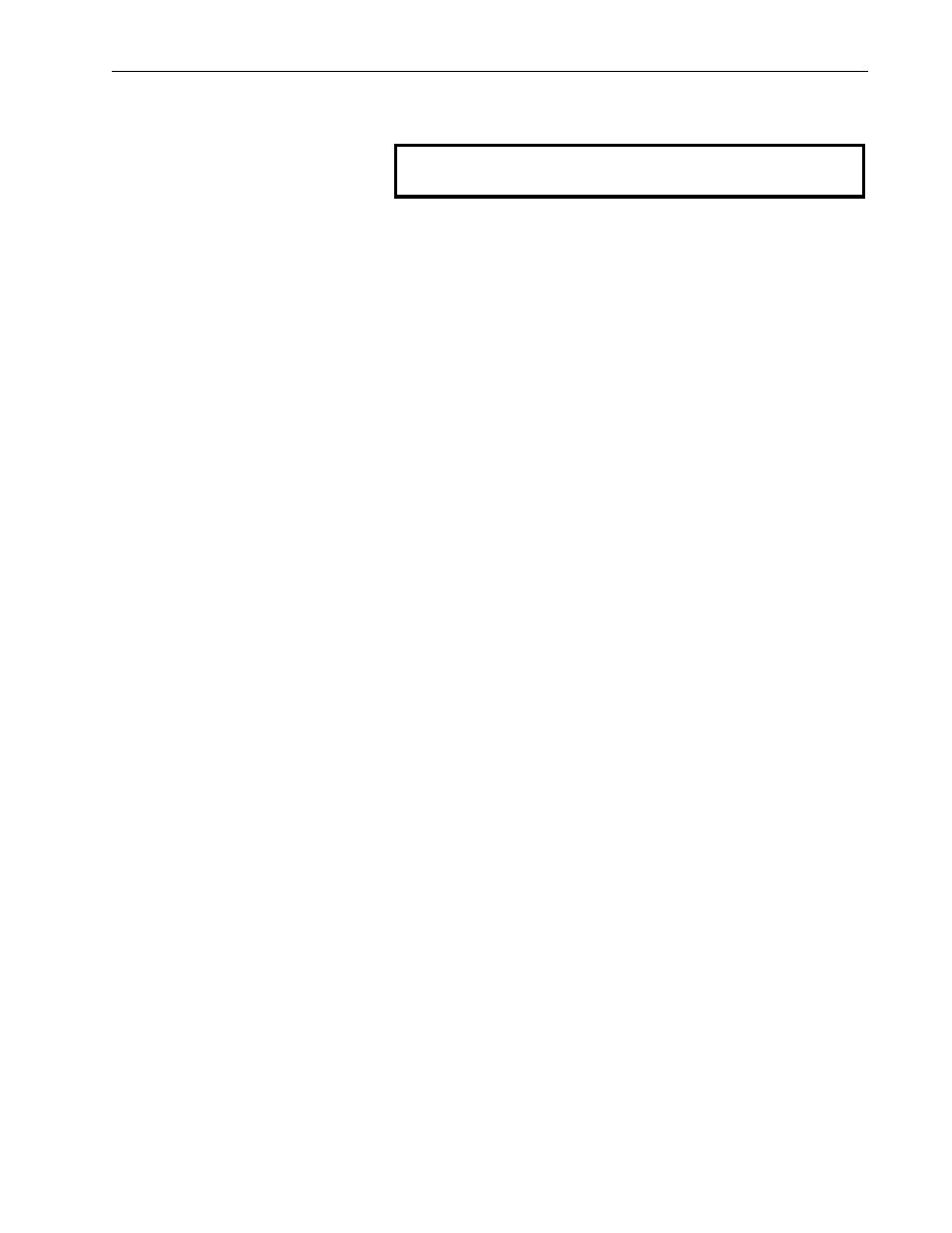
Understanding IMC-S/23x Setups
5-25
Publication 999-122 - January 1997
Editing the Feedback
Configuration
After selecting the axis, the IMC-S/23x asks
Toggle to
YES
and press ENTER to set up the conversion constant and
feedback loss detection for this axis.
Conversion Constant (K)
To allow axis position to be displayed and motion to be programmed
in the position units specified in the application setup menu, a
conversion constant must be entered for each axis. The conversion
constant (K) allows the IMC-S/23x to convert your position units into
encoder (feedback) counts and vice versa. For physical and virtual axes,
enter a value for K which is the number of encoder (feedback) counts
per position unit (as specified in the application setup menu) using up
to 15 digits, and press ENTER.
The IMC-S/23x uses 4X encoder decoding (both edges of channel A
and B are counted). The count direction is determined from both the
direction of the edge and the state of the opposite channel. Channel A
leads channel B for increasing count. This is the most commonly used
decode mode with incremental encoders, since it provides the highest
resolution.
For example, suppose this axis utilizes a 1000 line encoder in a motor
coupled directly to a 5 pitch lead screw (5 turns per inch). With position
units of Inches, the conversion constant is calculated as shown below:
For the imaginary axis, the conversion constant is essentially arbitrary,
but does affect the smoothness of gearing and position-lock cams which
use the imaginary axis as their master. In general, a value between 4000
and 10,000 counts per position unit should provide adequate resolution.
Edit Feedback Configuration? NO
K
1000
Lines
Rev
--------------
4
×
=
Counts
Line
------------------
5
×
Revs
Inch
-------------
20 000
Counts
Inch
------------------
,
=