Chapter, Technical overview – Rockwell Automation 999 IMC S Class Compact Motion Controller (Cat. No. 4100-999-122) User Manual
Page 31
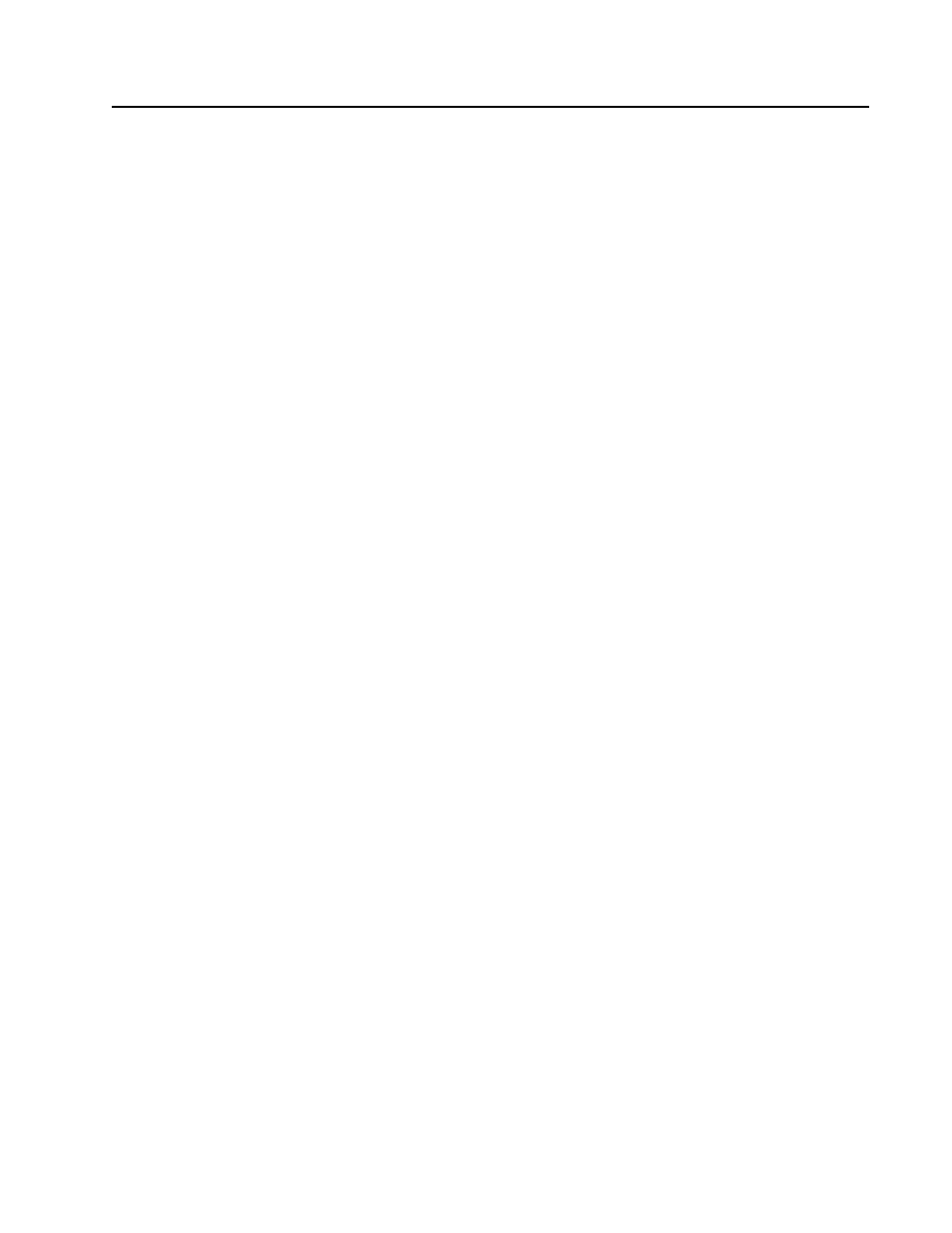
Publication 999-122 - January 1997
Chapter
3
Technical Overview
Digital Control Loop
Each axis of the IMC-S/23x utilizes a powerful Nested Digital Servo
Control Loop to provide servo positioning control and compensation
of a servo actuator. The servo actuator can be a DC motor, a brushless
DC motor, an AC motor (with the appropriate drive electronics), or a
hydraulic cylinder or motor.
The Nested Digital Servo Control Loop utilizes state-of-the-art digital
hardware and software to perform the functions necessary to establish
a closed loop servo system. The only external elements needed to
complete the servo loop are:
•
Actuator (Brushless DC Motor, Hydraulic Cylinder, etc.)
•
Servo Amplifier for Actuator
•
Digital Incremental Encoder (Quadrature type)
The digital approach to motion control has numerous advantages over
conventional analog servo control techniques. Digital feedback
eliminates the need for potentiometers in the control loop with their
associated adjustment labor and drift. Furthermore, the Nested Digital
Servo Loop is microprocessor-based. Microprocessor design reduces
the system parts count, increases system reliability, and greatly
increases the flexibility of the control.
The Nested Digital Servo Loop synthesizes a velocity (rate) loop as
well as the required position loop in software using only the position
information provided by the encoder (or other feedback device). No
analog tachometer is required to provide complete stabilization and
positioning control of the motor and load. In addition, velocity
feedforward is provided to reduce the intrinsic following error of the
position loop when the motor is moving.