Motor power cabling, Shield termination of power cables, Motor power emc shield connection – Rockwell Automation 1398-DDM-xxx USE MNL/ULTRA 200 DIG.SERVO.DR User Manual
Page 113: Tb1 – motor power terminals, E 7-3, Ge 7-3
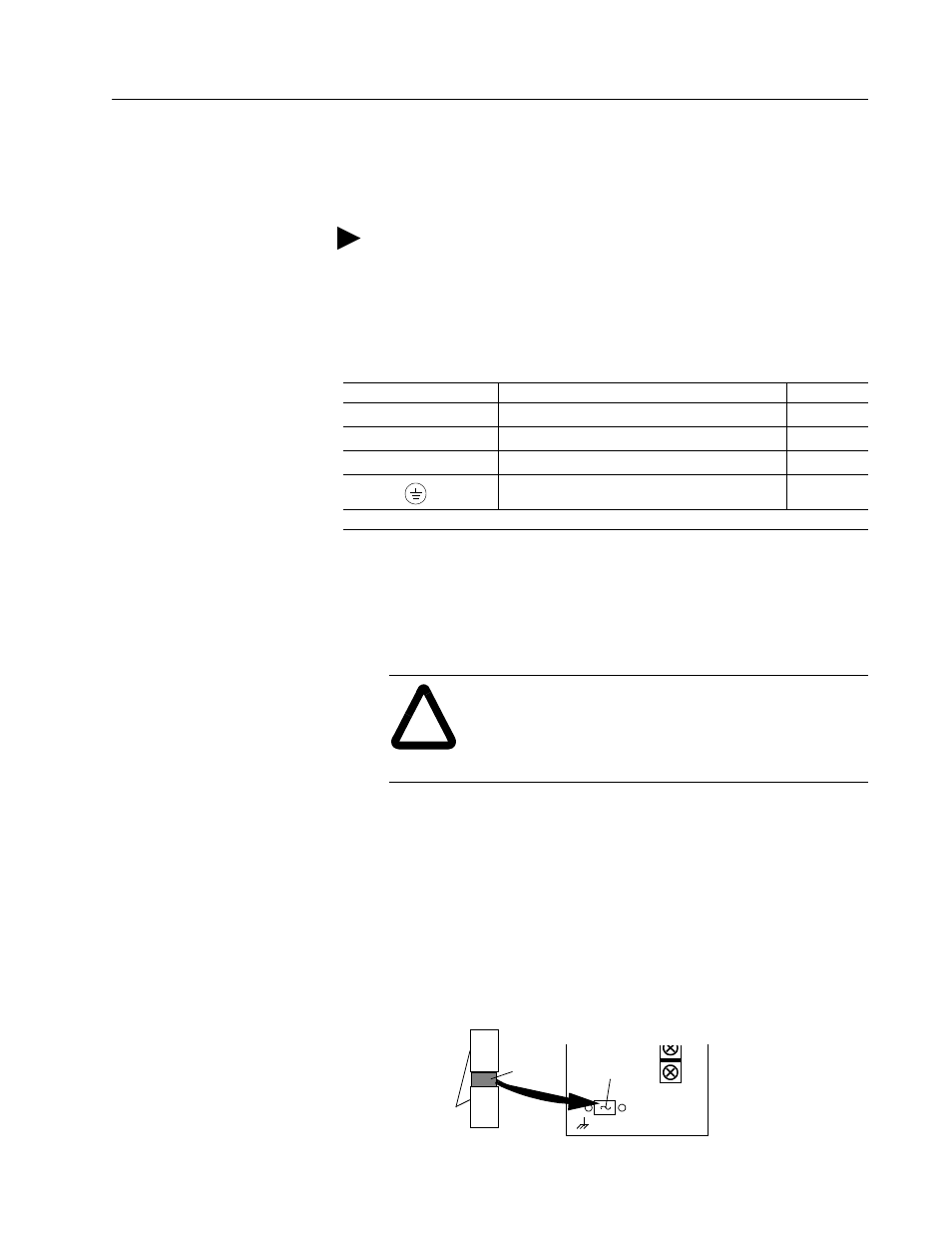
Publication 1398-5.0 – October 1998
Power Connections
7-3
Motor Power Cabling
Terminals 1 through 4 connect the drive to the windings of the motor.
Table 7.1 lists the drive terminals and typical motor connections;
Table 7.2 lists the minimum wire size for making power wiring
connections.
Refer to Appendix A, “Options and Accessories” for a list of available
Allen-Bradley cables.
Shield Termination of Power Cables
Allen-Bradley motor power cables are shielded. The power cable is
designed to be terminated at the drive during installation. A small
portion of the cable jacket is stripped, which exposes the shield wires.
The exposed area must be clamped at the left front of the drive chassis
using the clamp provided near the bottom. It is critical for EMC
performance that the shield wires be clamped against the area of the
chassis which is not painted. This section of the chassis is labeled with
the chassis ground symbol.
Note: Proper phasing of these outputs relative to the motor terminals
is critical. Double check the connections after wiring the motor.
Table 7.1:
TB1 – Motor Power Terminals
Motor Phase Signal
Description
Terminal
R
1
R phase from drive
TB1-1
S
1
S phase from drive
TB1-2
T
1
T phase from drive
TB1-3
1
Ground for the motor case
TB1-4
NOTE: Torque all terminal connections to 1.25 Nm (11.0 lb-in).
1.The I-Series and V-Series motors require swapping of the R and S motor power
leads when connecting to the drive.
!
Intro
ATTENTION: Shielded power cables must be grounded
at a minimum of one point for safety. Failure to ground a
shielded power cable will result in potentially lethal volt-
ages on the shield and anything connected to it.
Figure 7.1
Motor Power EMC Shield Connection
Intro
Masked area
Shield
Cable Jacket