Yaskawa J50M Instructions User Manual
Page 197
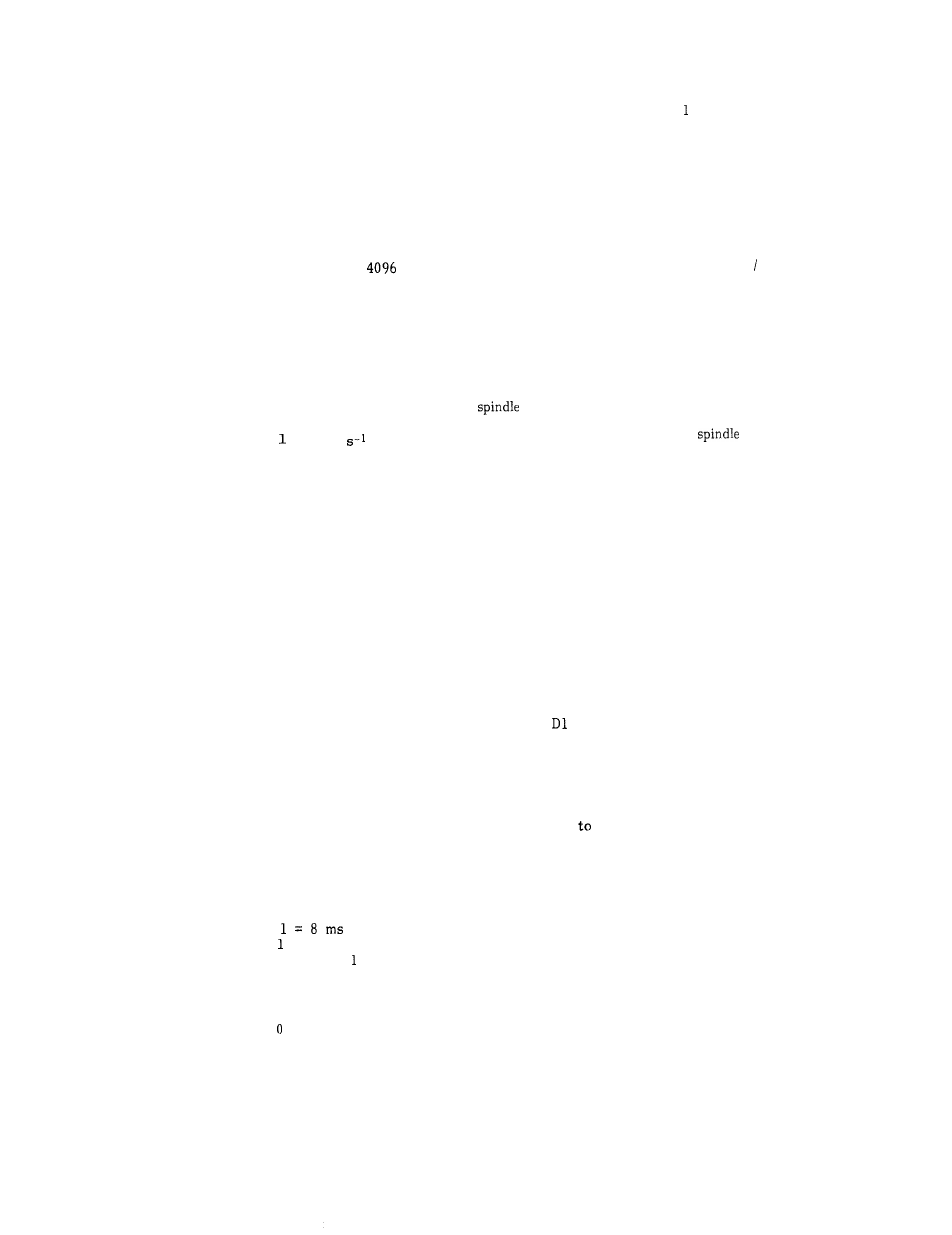
(4) Feedback pulses per spindle PG rotation
#6449
Setting unit:
1 = 1 pulse
Setting range: 1 to 32767
Standard setting value: 1024
Notes :
1.
Set the value before commanding the spindle
feedback pulse magnification, in this parameter.
2.
When performing spindle indexing, set the
parameter so that the feedback pulses (#6061
x
#6449) per spindle rotation become
pulses.
(5) Spindle revolutions against commanded voltage 10 V
in the spindle indexing execution gear
#6472
(6) Spindle
#6486
(7) Spindle
#6174
(8) Spindle
#6462
Note :
Setting unit:
1 = 1 rein-l
Setting range: 1 to 32767
Standard setting value:
6000
designation unit position loop gain
Setting unit:
= 0.01
Setting range: 1 to 32767
Standard setting value: 2500
error detection ON area
Setting unit:
1 = 1 pulse
Setting range: 1 to 255
Standard setting value: 50
indexing rotary speed reference
Setting unit:
1 = 500 pulse/s
Setting range: 1 to 32767
Standard setting value: 20
The spindle indexing rotary speed cannot exceed
the maximum speed of the spindle (#6472) .
(9) Spindle indexing creep speed reference
#6463
Setting unit:
1 = 500 pulse/s
Setting range: 1 to 32767
Standard setting value: 10
Note :
The spindle indexing creep speed cannot exceed the
maximum speed of the spindle (#6472) .
( 10) Spindle indexing spindle stop acknowledgment
timer
#6464 Setting unit:
Setting range: to 255
Standard setting value:
(11) Spindle indexing reference point position
#6465 Setting unit:
1 = 1 pulse
Setting range: to 4096
Standard setting value: O
(12) Spindle stop acknowledgment revolutions
#6473 Setting unit: 1 = rein-l
Setting range: O to 30
Standard setting value: 30
( 13) Spindle revolutions upper limit for solid tap
#6471 Setting unit:
= 1 rein-l
Setting range: 1 to 32767
Standard setting value: 4500
5.2.12.3 1/0 SIGNALS
The 1/0 signals described here are used to transmit
the operation request and the ending between the
NC unit and the sequencer.
Spindle indexing can
normally be performed by the miscellaneous function
command, without considering these I O signals.
(1) Spindle indexing position command
#1341 D7 to DO
#1342 D3 to DO
Note :
A binary 12-bit (O to 4096) input that specifies the
stop position.
The sum of the data input to
this external input signal and the data preset in
the parameter (#6465) is the
stop position.
(2) Spindle indexing input
#1343 DO 1:
Spindle indexing request ON
o:
Spindle indexing request OFF
Note :
If this input turns on while the spindle is rotating,
the revolution command for the spindle indexing
operation is output.
The spindle indexing operation
is performed when the spindle stops.
The spindle
revolution command analog output is still the spindle
positioning command even after the spindle indexing
is completed, and continuous the spindle indexing
operation until this input is turned off.
(3) Spindle indexing position incremental command
#1343
1:
Spindle indexing incremental
request ON
o:
Spindle indexing incremental
request OFF
Note :
This input is
accept, the spindle indexing position
command input prepared for multiple spindle
indexing to different positions, as the incremental
position command from the previous spindle indexing
p o s i t i o n . H o w e v e r ,
turning on this input for the
first spindle indexing after rotating the spindle
with an operation other than the spindle indexing
operation, or the first spindle indexing operation
after the power is supplied, will not make an
incremental position command.
(4) Spindle indexing restart input
#1343 D2 1:
Spindle indexing restart request
ON
o:
Spindle indexing restart request
OFF
189