Dr. Livingstone, I Presume WELDWISE 2400 User Manual
Page 81
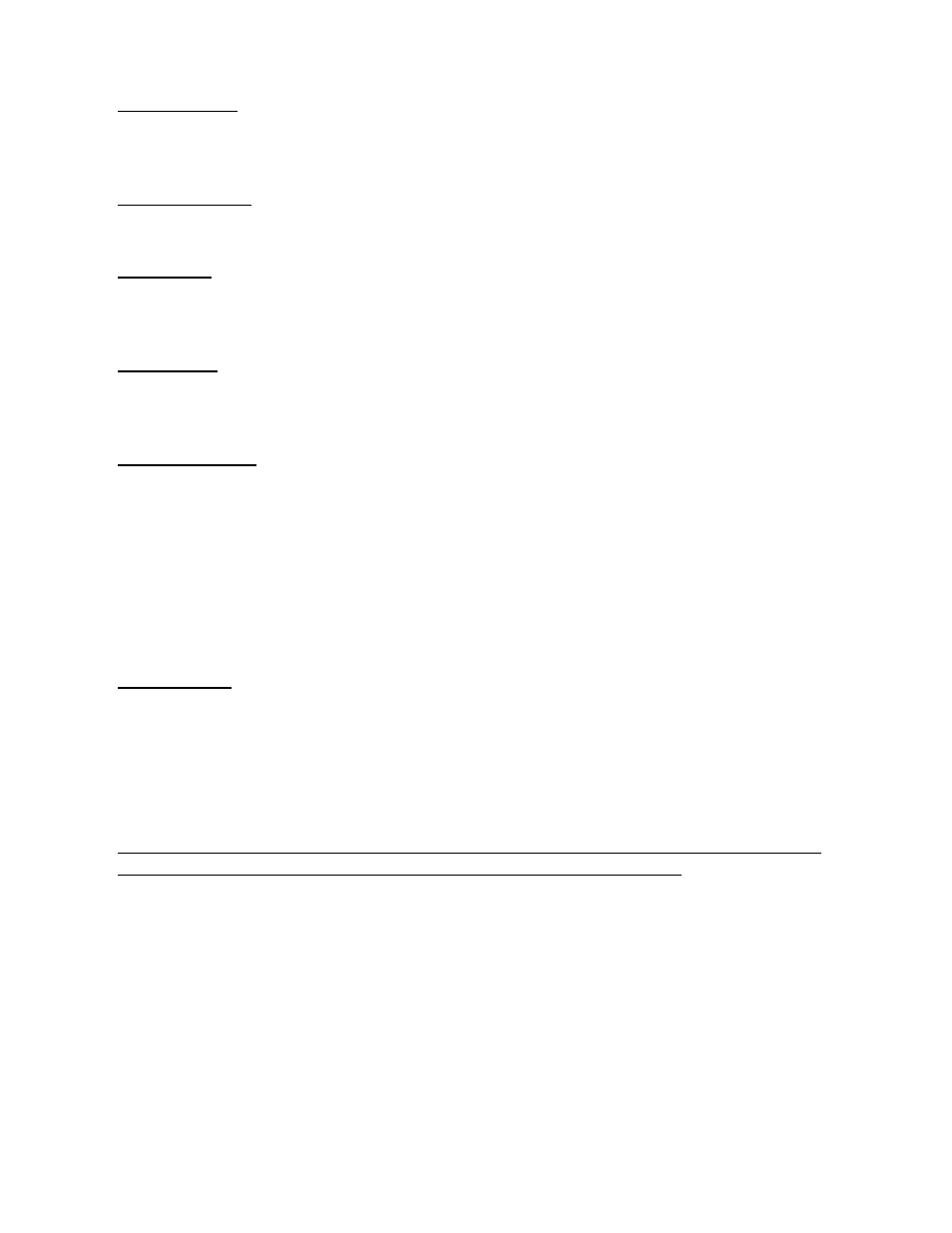
0433-INS-400
Rev.
E
6-35
• Trigger Hcycle (Applies only when Scope Mode is Enabled)
Trigger Hcycle determines the halfcycle within the Trigger Segment that will be the start of data
gathering in Scope Mode. This halfcycle is the 'trigger point' for Scope Mode.
• Trigger Segment (Applies only when Scope Mode is Enabled)
Trigger Segment determines the weld segment in which data gathering starts in Scope Mode.
• Trigger Pre (Applies only when Scope Mode is Enabled)
Trigger Pre determines the amount of time (in halfcycles) that data is gathered before the 'trigger
point' in Scope Mode.
• Trigger Post (Applies only when Scope Mode is Enabled)
Trigger Post determines the amount of time (in halfcycles) that data is gathered after the 'trigger
point' in Scope Mode.
• Max Bad Hcycles (Default Setting: 0)
Max Bad Hcycles is the number of rejected halfcycles that the weld monitor ignores when
determining whether the weld is rejected or accepted based on a halfcycle fault. The number of
rejected halfcycles includes the number of halfcycles that rejected due to a parameter fault (not
within master tolerance limits), plus the number of halfcycles where there was conduction angle >0
(current flow) where the master weld did not have a conduction angle >0 (no current flow), plus the
number of halfcycles where the conduction angle = 0 (no current flow) where the master weld did
have a conduction angle >0 (current flow). Although the weld may be Accepted, the rejected
halfcycle data is still recorded in the database and displayed in the Halfcycle and Weld Summaries.
• AD Threshold ( adjustment may be required)
Recommended initial setting: 750
The weld monitor determines that a weld is occurring by using a toroid to monitor the flow of weld
current in the secondary (weld loop) of the transformer. AD Threshold and AD Hysteresis are
adjusted collectively in order to avoid false triggering due to electrical noise. This noise may be
caused by nearby contactors, other secondary shunts in multi-head applications, servo drives, etc.
The sum of the AD Threshold and AD Hysteresis settings determines the minimum amount of
Current that must flow before the weld monitor begins capturing weld data. If the AD Threshold is
set too high, the monitor may record inaccurate halfcycle counts and produce inaccurate
information. Too low a setting may cause false triggering leading to rejected welds and possible
loss of data during a weld.
For maximum accuracy, the AD Threshold should be set to a value higher than random noise
spikes in the toroid signal. Generally, the AD Threshold is adjusted to a value twice the noise floor
in the toroid signal. The following graph should be used to determine an initial setting for these
values. However, since each welding application and environment is unique, these settings may
need further adjustments.
Scope Mode can be used to help determine an appropriate setting if the initial settings do not work.
Call Livingston & Co. for technical support or for more information.