Displacement channel overview – Dr. Livingstone, I Presume WELDWISE 2400 User Manual
Page 156
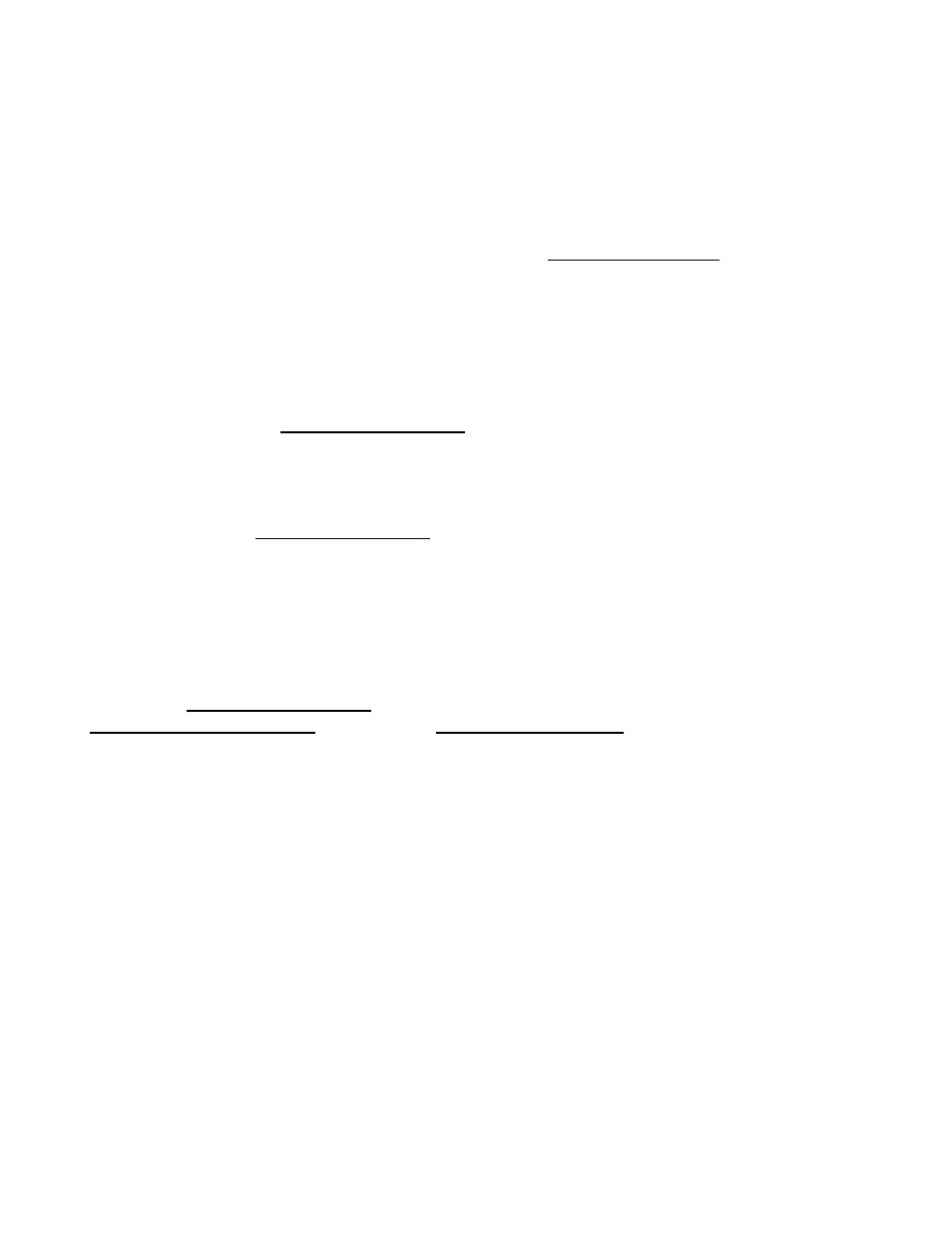
11-10
0442-INS-400 Rev. C
Displacement Channel Overview
The displacement channel is used to measure the thickness of a part before, during, and after the weld
process. This channel is designed to work with a potentiometer type sensor, which is a variable resistor
with three terminals; one on each end of the resistor and one “wiper” which contacts the resistor to
indicate a variable position. The potentiometer is used as a voltage divider to indicate position of the
electrodes. For proper installation, please refer to Chapter 7, Installing the Sensors.
The weld monitor provides a 10-volt excitation voltage for the sensor. The signal returned from the
potentiometer is 0 to 10 volts depending on the position of the potentiometer shaft. For example, a 4”
stroke linear potentiometer will return 0 volts when the shaft is fully extended, 10 volts when fully
retracted and 5 volts at a position of 2” (mid-stroke). Depending on wiring and sensor mounting,
opening and closing the electrodes may cause a positive or a negative voltage change. The weld
monitor will accommodate either polarity by setting the Displacement Polarity accordingly in the
General Setup (Refer to WMS Reference Guide in Chapter 6).
In order to get an accurate high-resolution measurement over a relatively small window of travel of the
sensor, the displacement channel is designed to read an input voltage of +/- 0.45 volts, which
corresponds to 9% (+/- 4.5%) of the sensor’s full stroke. When viewed using the Input Monitor
screen (see chapter 6, WMS Reference Guide), the A/D reading will saturate at +32767 (0.45 volts),
and –32768 (-0.45 volts). Since the displacement sensor returns a signal from 0 to 10 volts, the
displacement channel will be saturated over all but 9% of the stroke. Note: This saturation is normal
and will not damage the displacement channel.
The Zero Displacement feature is used to center the displacement readings within the 9% window.
Typically, displacement is zeroed using a “zeroing” gauge block to represent the initial part stack-up
(projection welds), or zeroed with electrodes closed (spot welding). Refer to the Input Monitor screen
in chapter 6, WMS Reference Guide to use the Zero Displacement feature. Refer to Chapter 9 -
Frequently Asked Questions and Chapter 8- Calibrating the Sensors for how to calibrate the
displacement sensor.
Example: A linear potentiometer with a 4” stroke will have a usable displacement window of 0.360”
(9% of 4”). If the potentiometer is extended to a stroke of 1”, and the displacement is “zeroed” at this
point, then the 9 % window would be +/- 4.5% (+/- 0.180”) of the stroke, relative to 1”. In other
words, the weld monitor would measure usable readings when the actual stroke is between 0.820”and
1.180”. The calibrated readings reported by the monitor within this window would be –0.180” to +
0.180”. In the example, the maximum allowed displacement change is +/-0.180” during the weld.
Note: If in the example the part stack-up physically changed by greater than 0.180” then the reading
reported by the monitor would be in error since the displacement was saturated at some point during
the weld. The solution would be to use a longer stroke sensor or mechanically change the ratio of
electrode movement to sensor stroke to enlarge the measured window.