Mass monitoring, Dynamic monitoring – Dr. Livingstone, I Presume WELDWISE 2400 User Manual
Page 21
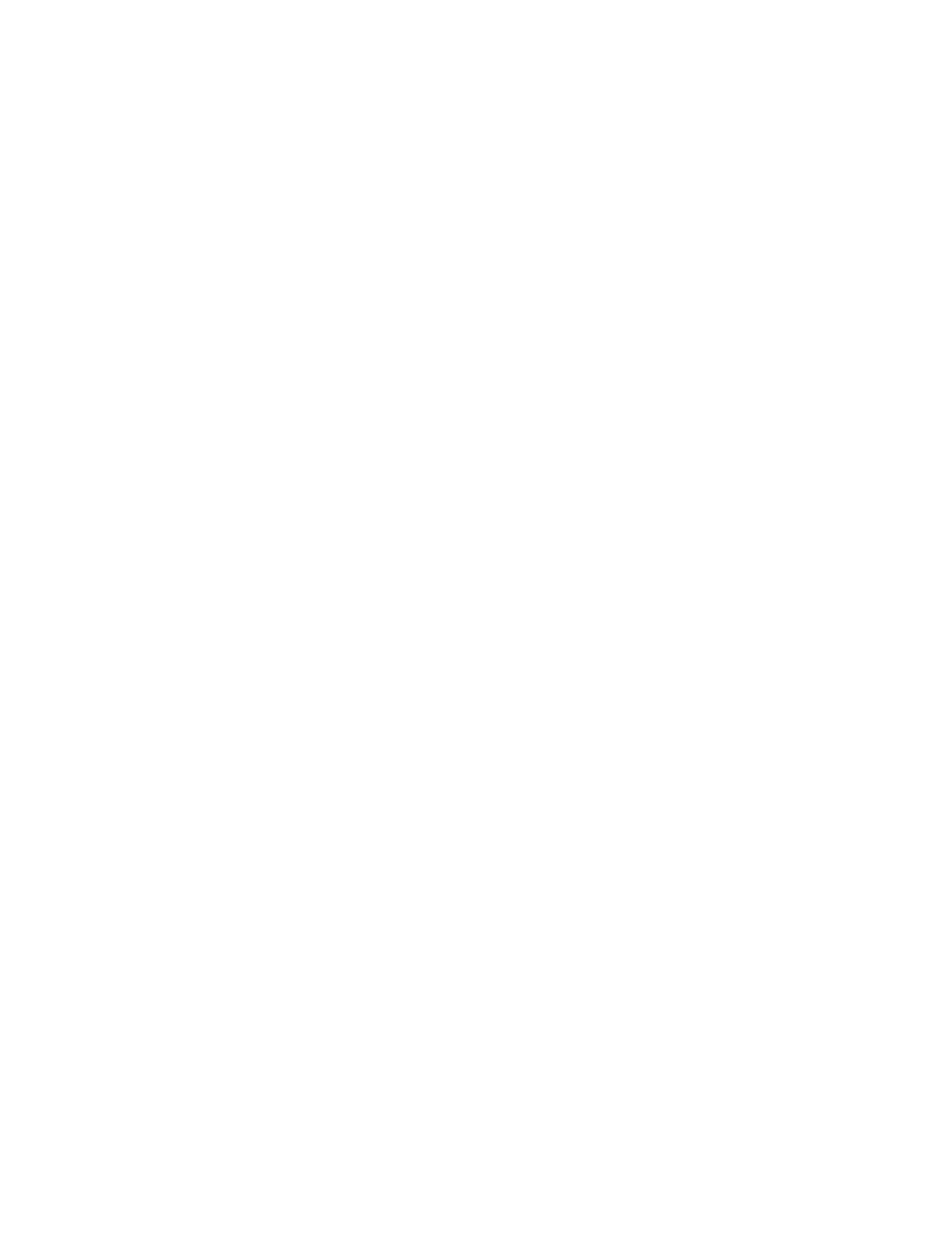
0429-INS-400 Rev. C
2-3
displacement can indicate whether the resulting weld was formed properly. BA monitoring measures
the displacement before the weld is made (Initial Thickness), and then again after the weld is made
(Final Thickness). However, if it is determined that the displacement is consistently below where it
should be (e.g., the nut is not sinking far down enough into the workpiece to make a good weld), BA
monitoring cannot identify exactly where in the process the problem is occurring. Similarly, the BA
monitor may indicate a normal setdown, yet the nut may be sinking down much too quickly due to
expulsion. While BA monitoring provides an account of the beginning and end of the weld process, the
key middle-portion of the process is unwisely overlooked.
Mass Monitoring
Mass monitoring provides a more in-depth examination of the weld process, but does it by averaging
all the measured parameters during the course of the weld. Using the weld nut from the displacement
example in the previous section, we'll examine force during the weld process. The nut and workpiece
are clamped together under pressure between the electrodes, and the weld current is fired, generating
heat and creating a weld. A Mass monitor will measure parameters during the weld process and will
provide an average for each after the weld is made. In this particular example, the monitor might
indicate that the average force during the weld was 800 lbs. Suppose, however, that subsequent
destructive testing of the part showed that the weld was bad. Why would this be the case if the monitor
indicated that the average force was appropriate?
The trouble with this type of monitoring system lies in the averaging of the parameters before a result
is presented. Recall that a typical weld cycle can be broken up into three separate sections: the pre-
weld, weld, and post-weld segments. If the force during each of these sections was 1700, 300, and 400
lbs., respectively, the average would be 800 lbs. The end result appears acceptable, but the averaging
only serves to disguise substantial irregularities in the force during the weld process. Mass monitoring
is also relatively insensitive to changes in the weld schedule and weld current. Aspects such as
upslope and downslope are recorded, but are delivered as averages rather than by the cycle (or
halfcycle). Although the average current for a 10-cycle weld could be the same as for a 20-cycle weld,
there would probably be a great deal of expulsion in the 20-cycle weld. A Mass monitor would not be
able to detect anything amiss in this situation, because the average would likely be an acceptable
figure. While Mass monitoring is a more thorough method of observation than BA monitoring, it's still
not the most effective method of monitoring the resistance weld process.
Dynamic Monitoring
Dynamic monitoring is currently the most comprehensive method of observing and recording the weld
process. A Dynamic resistance weld monitor measures weld parameters in real-time, while the weld
process is happening. More detailed than a before/after picture, and more accurate than an average of
each parameter, a Dynamic monitor provides a complete view of the weld process as the weld is being
made, measured in either halfcycles or cycles (based on a 50 or 60 Hz sine wave). Because the weld
process is observed so closely, events such as Expansion and Setdown can be pinpointed down to the
halfcycle. If weld irregularities are suspected, recorded weld data can be analyzed to determine where
in the process they're occurring and what factors are contributing to the problem. Potential problems
can also be detected before they occur: parameters such as resistance or force can be trended to
ultimately predict electrode wear and improve preventive maintenance schedules.