Dr. Livingstone, I Presume WELDWISE 2400 User Manual
Page 13
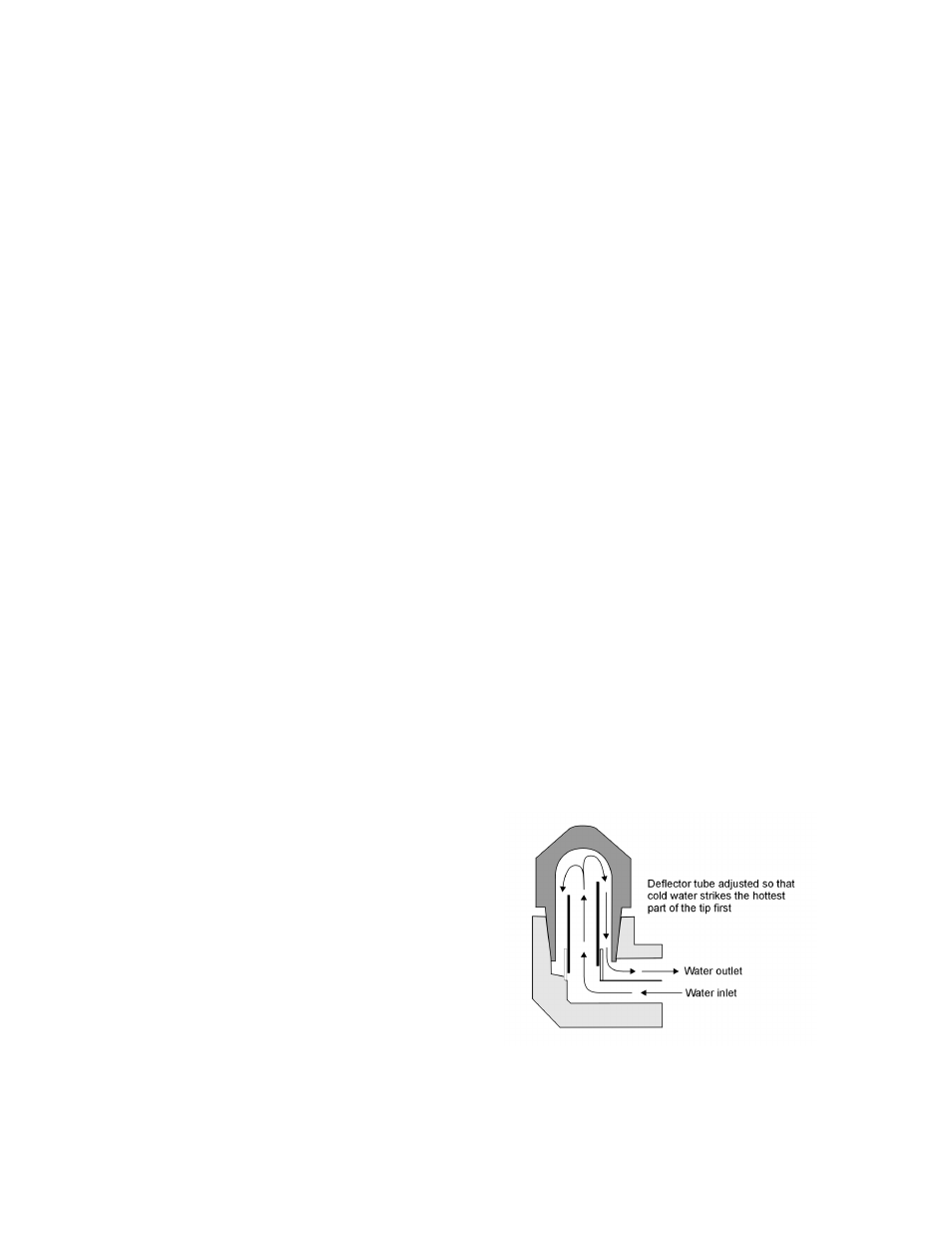
0428-INS-400 Rev. E
1- 5
an acorn to the size of a plum, it is also important to choose electrodes that are able to withstand the
force needed to make a good weld.
A key point to understand is that force and resistance have an inverse relationship: more force will
result in less resistance, and vice-versa. The equation has to do with surface contact, which refers to the
specific area on the workpieces touched by the electrodes. Surface contact will be covered further in
the next section, but the following example will begin to illustrate this relationship: if you examine
your fingertip under a magnifying glass, what first appears to be a smooth surface is actually a mass of
rough-looking ridges and bumps. The same is true of electrodes and workpieces. The tips of the
electrodes and the surfaces of the workpieces may look to be smooth and in good condition, but in
reality their surfaces are quite rough, especially if the electrodes are old and worn or if the workpieces
are dirty. By applying pressure to these rough surfaces, any microscopic inconsistencies (e.g., dirt or
grease on the workpiece and/or pits and cracks in the electrodes) are compressed and the surface
actually evens out. This results in improved (increased) surface contact between the electrode tips and
the workpiece, and between the workpieces themselves. When the surface contact is increased, current
can flow more readily from the tips through the workpieces, which means that the resistance has been
lowered.
Force also is what helps to keep the weld intact as it's being formed. As the current generates heat, the
workpiece metal begins to melt. A good analogy to this process is a child eating a popsicle on a hot
summer day. When the popsicle melts, it doesn't remain on the stick― it drips everywhere. When
metal melts it wants to do the same thing, however because it's molten metal and not a runny popsicle,
it doesn't simply drip. It explodes out of the workpiece. This is why proper weld force is so important:
it literally forces the molten metal to stay put, so it can then cool to form a weld nugget. Without
sufficient force, the metal will do what it wants to do, which is what causes expulsion. Expulsion is
nothing more than little pieces of molten metal exploding out of the weld because they're not being
properly held in. The problem with expulsion is that all the metal flying out of the weld is metal that's
not going in to the weld; a weld cannot be made stronger by removing metal from it. Determining the
proper amount of force is entirely application dependent. The RMWA can be contacted for additional
recommendations and guidelines.
Cooling the Workpiece
Electrodes get considerably hot with 10-20 KA or
more repeatedly flowing under hundreds of pounds
of force. Although most welders have an internal
water cooling system that allows water to circulate
through the tips of the electrodes while welds are
being made, a common problem is a lost, damaged or
improperly sized cooling water tube. Without
anything to cool off the tips, heat can quickly build
up to the point where the electrodes will eventually
weld to the workpieces. To correct this problem, the
water tube should be placed so that the incoming
cold water strikes the hottest part of the tip first, as
shown in figure 1-2.
Figure 1-2 Example of an electrode cooling
channel.