Introduction to resistance weld monitoring, Introduction, Why monitor – Dr. Livingstone, I Presume WELDWISE 2400 User Manual
Page 19
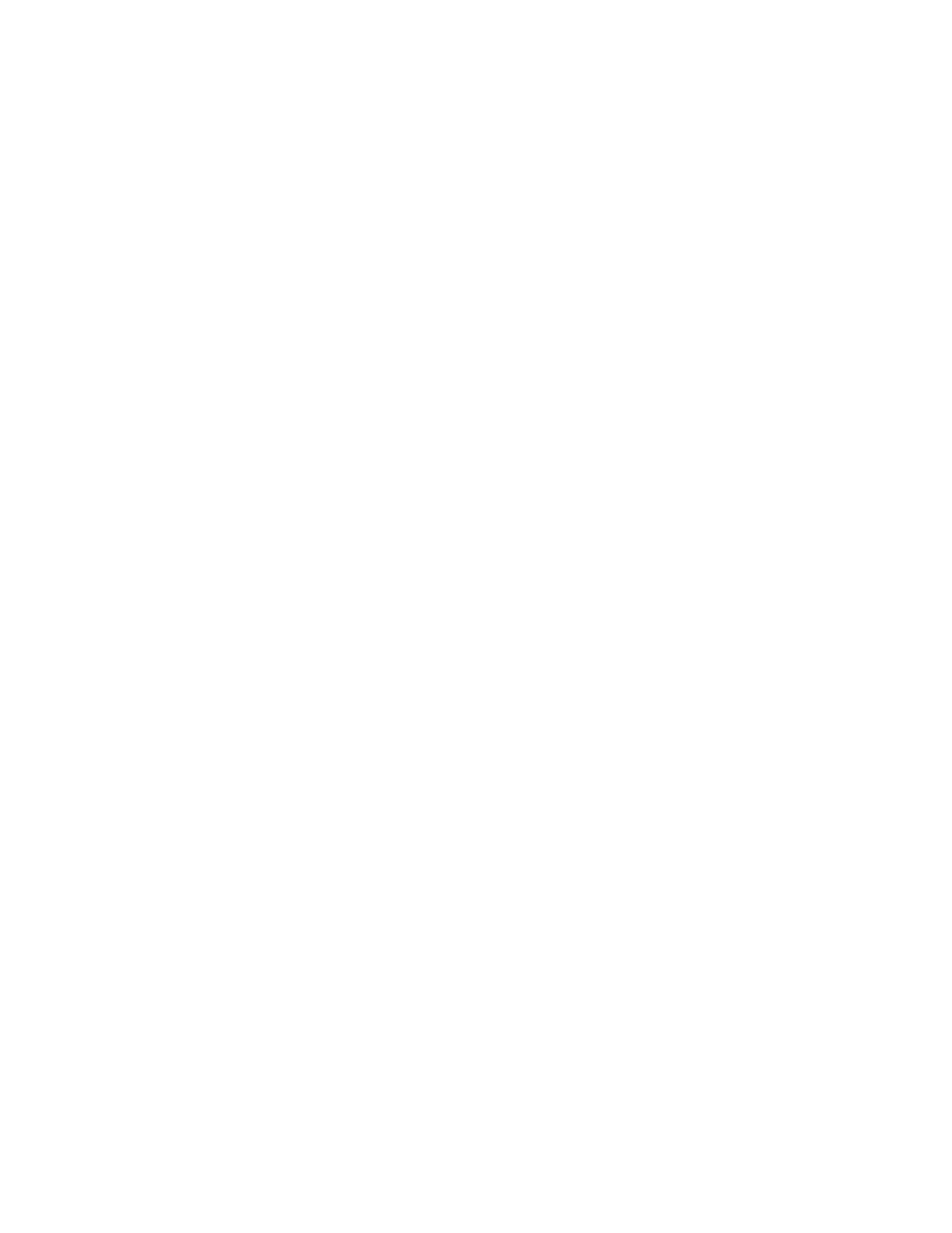
0429-INS-400 Rev. C
2-1
Introduction to Resistance Weld Monitoring
Introduction
As discussed in the last chapter, what you see is not always what you get. Although a constant current
control may indicate that there is sufficient weld current to create a quality weld, unless the
measurement is taken at the electrodes, the actual amount of heat generated is only speculation. In
view of the fact that the generation of sufficient weld heat is a function of current density, it could
logically be argued that the primary cause of bad welds is inadequate current density. Many factors
affect current density: poorly maintained, worn or improperly sized electrodes, dirty materials, lack of
sufficient force at the tips and lack of sufficient weld current at the tips are just a few examples. This
being the case, how can a production person or weld engineer catch these (or other) potential problems
before they lead to bad welds? How do you make sure that what you see is what you get? The answer
lies in the subject of this chapter: resistance weld monitoring.
Why Monitor?
When Professor Elihu Thompson developed the concept of resistance welding, the idea of weld
monitoring most likely didn't exist. At that time, the only means available of differentiating a good
weld from a bad weld was through destructive testing. Even today, destructive testing is regularly used
to provide a reliable answer— 'good weld' or 'bad weld'— depending on how the weld reacts during its
destruction. For all its reliability, however, destructive testing doesn't tell the whole story. While it can
easily be determined whether a weld is good or bad, uncovering the precise factors that made it that
way is not as straightforward. Was there an excess or deficiency of one or many factors during the
weld? At what point or points in the welding process did the excess or deficiency occur? Resistance
weld monitoring can provide immediate answers to these questions.
With the advent of advanced computer technology, today's methods of observing and testing individual
weld integrity have advanced significantly, keeping in step with ever-evolving safety and quality
standards. By monitoring the welding process, compliance with international quality standards– such
as ISO and/or QS 9000+, or MVSS– is simplified. Weld quality can be instantly verified with
electronic documentation of individual weld characteristics; hard copy of weld data can even be
printed for comprehensive record keeping or for inspection. It's hard to dispute the integrity of a
product when the most critical stages in the manufacturing process have been systematically observed,
recorded and analyzed.
It's important to realize that weld monitoring is not a substitute for destructive testing. Rather,
monitoring and destructive testing go hand in hand. While destructive testing can unconditionally
guarantee whether an individual weld is good or bad, monitoring can show why that particular weld
was good or bad. Together, they can answer what is perhaps the most important question of all: is the
welding process consistently within the defined weld lobe?