Dr. Livingstone, I Presume WELDWISE 2400 User Manual
Page 27
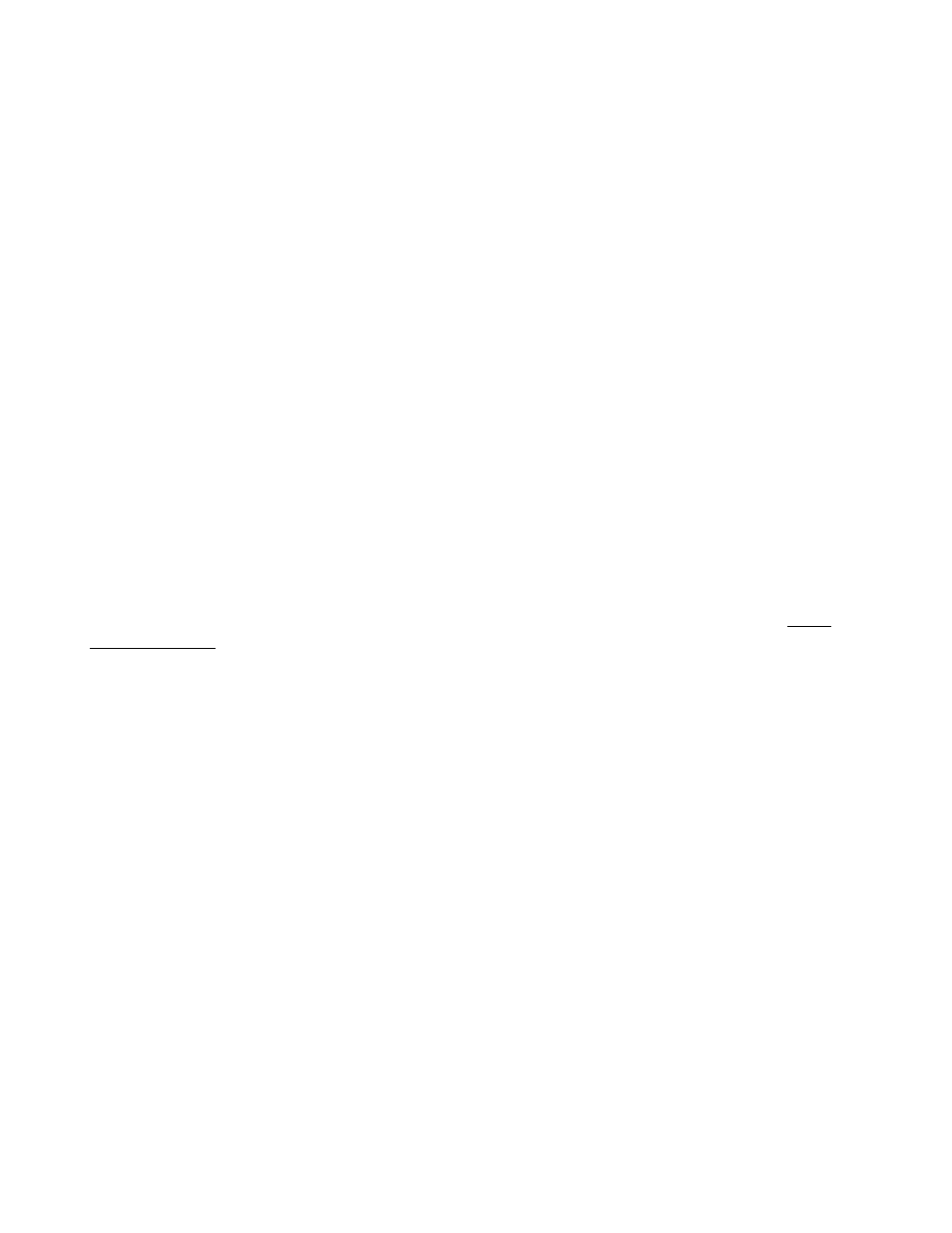
0430-INS-400 Rev. D
3- 3
Every factor involved in making a weld has its own weld lobe and set of unique tolerances. There are
multiple parameters that can be measured and toleranced using a Livingston monitor. The WMS
program makes it easy to define, track and record tolerances for each parameter critical to the weld
process. For maximum flexibility, acceptable tolerances can be specified by absolute or relative values
when comparing weld data in real-time against a master.
Measured Parameters
Livingston monitors capture measurements from up to four sensors attached to a welder. From these
four measurements, the monitors then calculate and record the following parameters:
• Current Rms
• Part Expansion
• Current Peak
• Electrode Setdown
• Voltage Rms
• Conduction Angle
• Voltage Peak
• Energy
• Force
• Resistance (Dynamic)
• Initial Part Thickness
• Number of Halfcycles
• Final Part Thickness
For a complete definition of each of these measured parameters, please refer to section 6, the WMS
Reference Guide.
Segments
Since there are many different weld processes, users may be more interested in observing and
analyzing certain time periods during a weld. To accommodate these differences and needs, Livingston
devised the concept of segments. A segment is simply a collection of halfcycles before, during and
after the firing of weld current. By default, there are three segments created when a master is made: the
Pre-Weld (Squeeze), Weld, and Post-Weld (Hold) segments. Different tolerances can be set for each
segment, segment lengths can be increased or decreased and new segments can easily be created.
Using segments, each weld can be divided into as many parts as necessary to focus on the data that is
critical to the weld process. Consider the following example:
Coated steel is being welded with the following weld schedule: 8 cycles of Squeeze, 10 cycles of Weld
and 12 cycles of Hold. The objective is to monitor the current density during the Weld time, to ensure
sufficient concentration for high-quality welds. According to the factory weld lobe, the current at the
electrodes during the weld must be 12 KA, with an allowable difference of only +/-0.5 Amp. After
examining preliminary weld data, it is discovered that the current during the first few halfcycles of the
Weld period is much less than 12 KA. The reason for the decrease is that the coating must first be
burned off before the weld current actually reaches the steel at the faying surfaces and makes the weld.
How can tolerances be properly set to accommodate the weld lobe specification of 12 KA +/- 0.5 Amp
without automatically rejecting welds during the time it takes for the coating to burn off?