Sensor calibration utilities overview – Dr. Livingstone, I Presume WELDWISE 2400 User Manual
Page 157
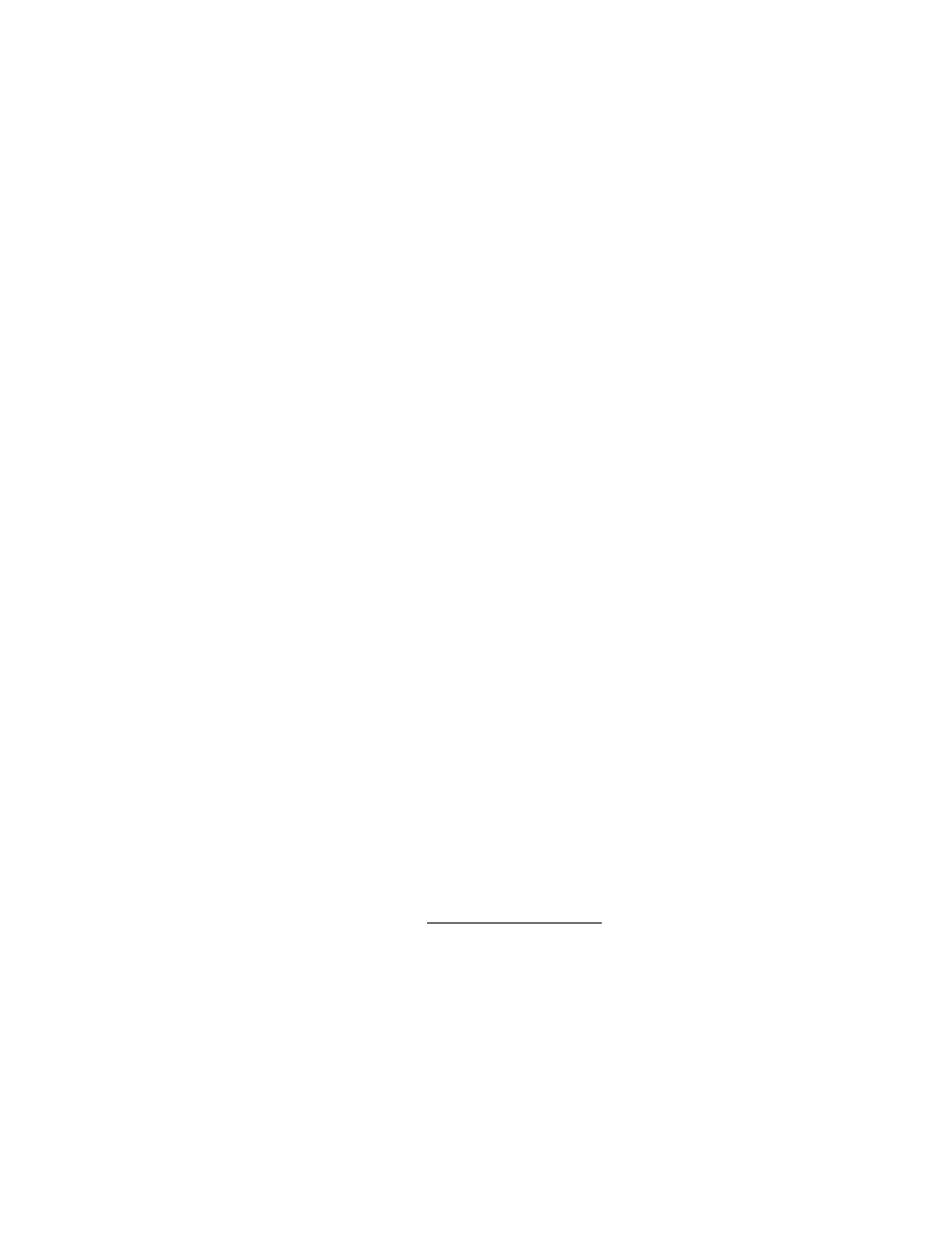
0445-INS-400 Rev. D
11-11
Sensor Calibration Utilities Overview
Sensors such as toroids, slide-potentiometers, and force gauges are used by Livingston weld monitors
to get information about the weld process as welds are taking place. The relationship between the
output of a particular sensor and a standard unit of measure (such as inches) is defined during the
calibration process. Many factors can influence the relationship between the output of a sensor and a
defined unit of measure, such as variations between sensors and different application techniques.
A good sensor will provide an output with a linear relationship to what the sensor is intended to
measure. During the calibration process, two known reference points are provided. From these points,
the Livingston weld monitor records the linear relationship between the installed sensor and standard
units of measure.
• The toroid (current sensor) channel is calibrated at the factory and does not require further
calibration.
• The voltage channel has no sensor (readings are picked up via lead wires attached close to the
electrode tips), and therefore does not require calibration after leaving the factory.
• The remaining two channels— force and displacement— must be calibrated only when a new
sensor or slide-potentiometer is installed.
• Under normal operating conditions, the only continuing procedure that is required is to zero the
displacement sensor when changing or dressing electrodes or when using workpieces of
significantly different thickness. This can be done via the Zero Displacement button in the
Input Monitor display.
Force sensor note: If it is not possible to obtain two distinct readings at different levels, the
monitoring program can work from a single value. For example, suppose you open the welder tips, but
cannot completely remove the force from a transducer because of the weight of connected mechanics.
Suppose you also can’t easily determine how much force is on the sensor, because it’s not practical to
get a calibrated force gauge into the mechanics. In this case, the weld monitor can perform a single-
point calibration by assuming that a zero output from the force transducer corresponds to a force of
zero PSI. When the weld tips are closed and a known force is provided as the second (high) reference
point, the linear relationship is established.
Note:
It is strongly recommended that whenever possible you use two calibration values to ensure
more accurate calibration and more precise monitoring operations. For more information about
calibrating sensors, please refer to chapter 8, Calibrating the Sensors.