Rockwell Automation 1441-PEN25-Z Enpac 2500 Data Collector User Manual
Page 87
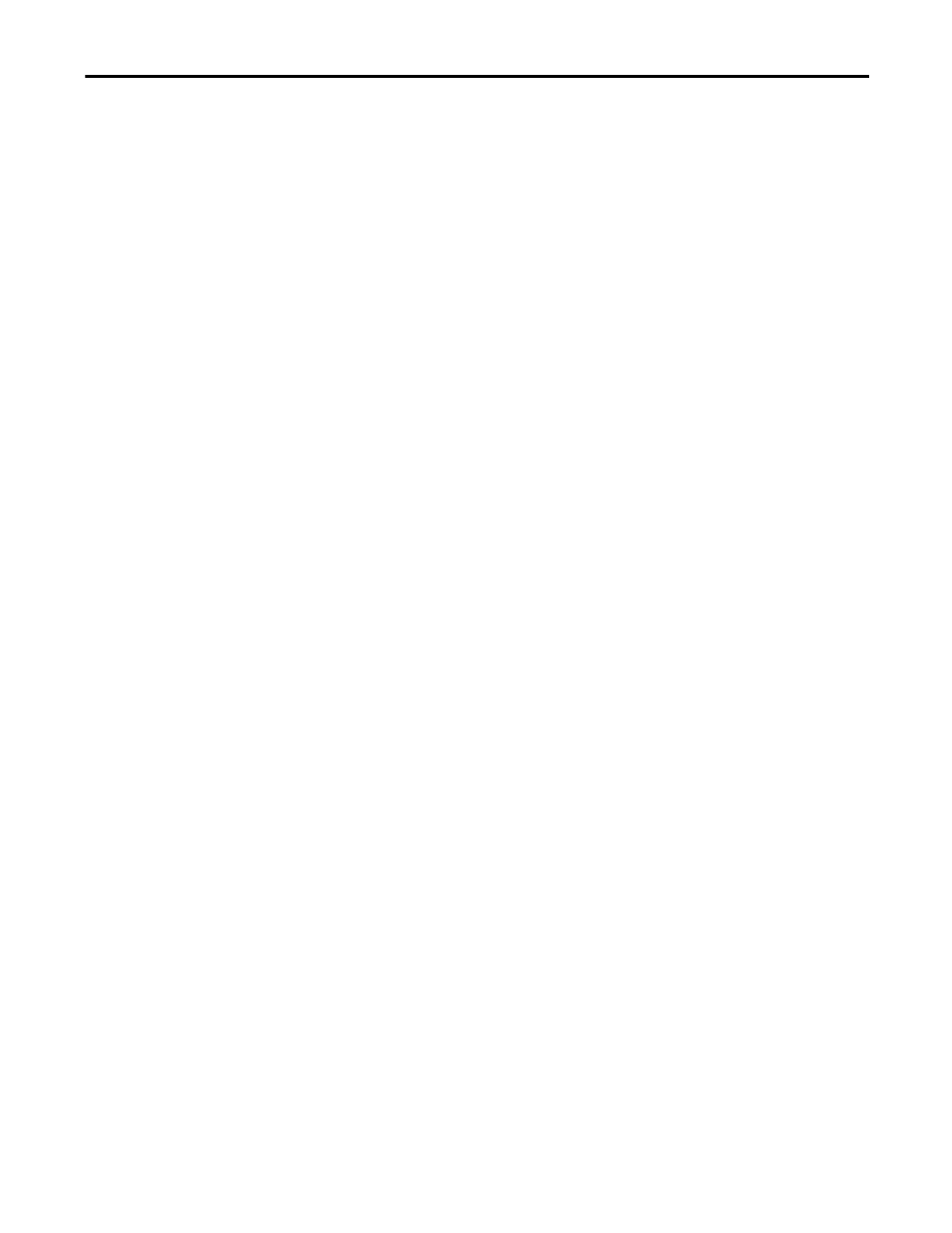
Rockwell Automation Publication GMSI10-UM002D-EN-E - August 2012
87
Setting Up Measurements
Chapter 2
Order Normalized Spectra in the Enpac 2500 Data Collector
•
Order normalized spectrum measurements have a frequency axis based on
multiples of the running speed (orders). This quickly identifies the
frequency relationship between each measured vibration amplitude and
the running speed of the machine. It is particularly useful on variable speed
machinery.
•
An order normalized spectrum measurement requires a trigger input to the
Enpac 2500.
•
Set up a Collection Specification with Window set to ‘Hanning.’ Select
the Maximum frequency in ‘Orders,’ and make sure to select the Order
normalization option. The Averaging can be either ‘linear’ or ‘time
synchronous,’ but should include at least four averages.
•
The Enpac 2500 may collect more orders than required. For example, if
you set the Maximum frequency to ‘10 Orders,’ the Enpac 2500 may
collect more than ten orders. The Enpac 2500 always collects at least the
number of orders you request in the Collection Specification.
•
The Enpac 2500 displays an order normalized spectrum. If the Collection
Specification dialog has the Also collect phase data checkbox checked, and
if the Maximum frequency is eight orders or less, the table on the Enpac
2500 screen shows the magnitude and phase values at each order. If the
Collection Specification dialog does not have the Also collect phase data
checkbox checked, or if the Maximum frequency is more than eight orders,
the table on the Enpac 2500 screen shows magnitude values only. The
Enpac 2500 displays a maximum of eight orders in the table.
If the table has eight orders or less, the Enpac 2500 arrow keys move the
spectrum cursor. If the table has more than eight orders, the Enpac 2500
arrow keys scroll the table values.
Proximity Probe Measurements
•
Proximity probes measure the position and motion of a shaft within a
bearing.
•
You can use a spectrum measurement definition to measure the dynamic or
AC component of a proximity probe measurement. This indicates the
motion of the shaft within the bearing at each frequency.
•
Set up a displacement transducer in the Transducer Calibration dialog
with Input type set to ‘AC Coupled’ and Units set to ‘mils’ or ‘um.’ Make
sure you enter the Calibration value that converts the voltage to a
displacement.
•
Set up the Collection Specification to include the displacement
Transducer, and set the Signal detection to ‘Peak-Peak.’ You also need to
select the window, frequency range, and averaging options.
•
Finish setting up the dynamic proximity probe measurement by setting
Data Type to ‘Magnitude’ and Units to ‘mils’ or ‘um.’ You can use a Filter if
desired, but make sure it does not interfere with the frequency of interest.