I.d. pressure, Purging techniques – Arc Machines 307 User Manual
Page 159
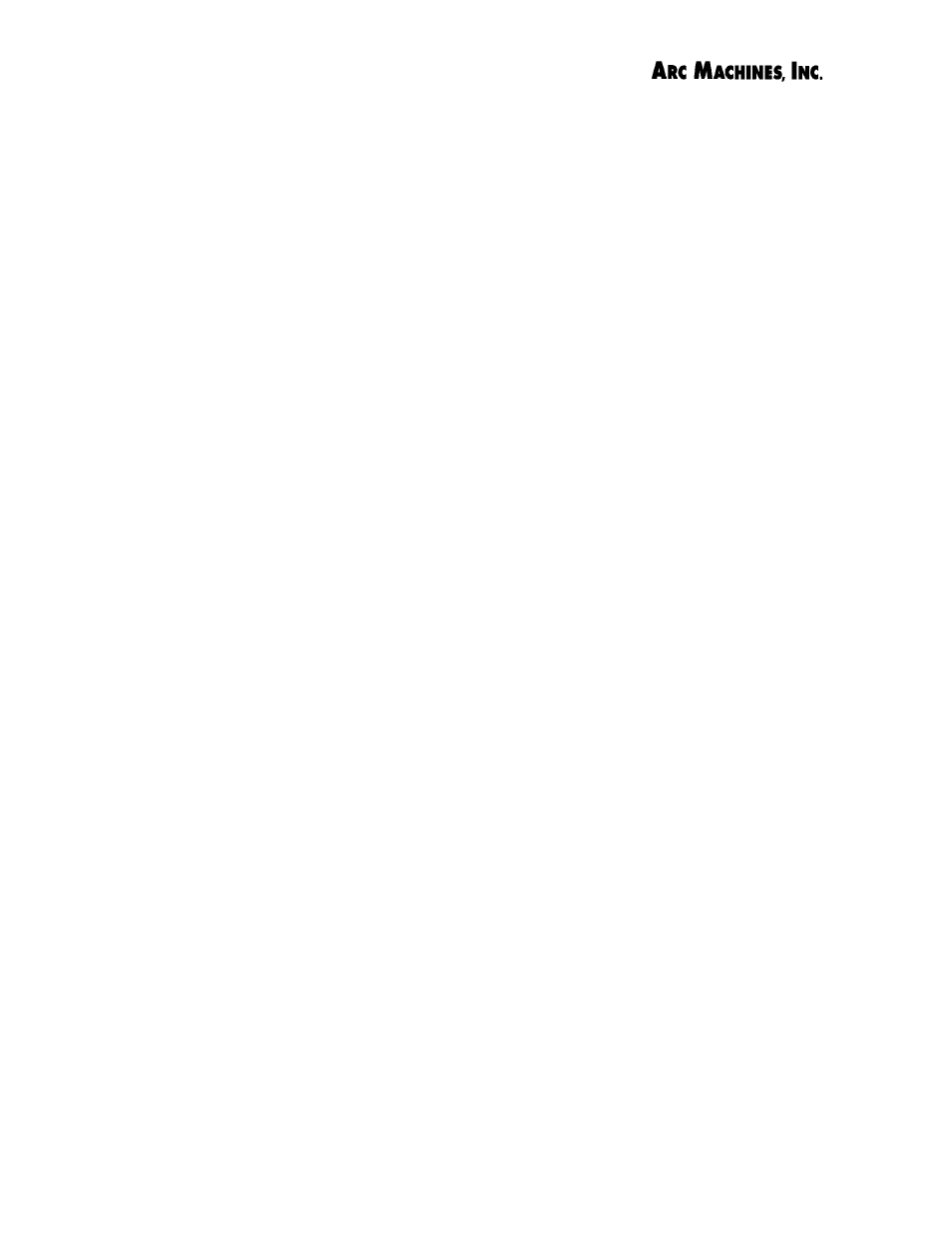
Arc Machines, Inc. Model 307 Orbital Tube Welder Training
Document No. 740096
Chapter 16. Page 6.
Rev. A
is sometimes used to flush out volatilized materials from the weld area be-
fore they can be deposited in order to prevent the "blue halo."
I.D. Pressure
Caution must be exercised to avoid overpressurizing the weld. If a high flow
rate is used, a larger exit orifice for the purge gas is required to prevent I.D.
concavity ("suck-back") or a blow-out. The exit orifice diameter should be
measured and recorded for each different size of tubing. A pressure gauge
(Magnehelic
®
or equivalent) connected to a tee inserted at the weld joint is
used in high purity applications to adjust the flow rate (or orifice size) that
will result in the amount of I.D. pressure necessary to produce a flat, fully
penetrated I.D. weld bead. The tee is then removed from the joint and the
weld head installed on the joint to make the weld using the predetermined
flow rate (orifice diameter). Flow rates, purge times, orifice sizes and inter-
nal pressure should all be documented as part of the Standard Operating
Procedures (SOPs) and, once established, followed routinely by all welding
personnel. See SEMI Standard F79-0703 Table 1. for suggested I.D.purge
settings for high-purity applications.
Purging techniques
Sound purging procedures are an essential component of a successful orbit-
al welding program. Successful purging requires gas of appropriate quality
for the application and maintaining the gas purity up to the point of use, i.e.,
the O.D. and I.D. of the weld puddle and HAZ. This requires air-tight hoses
and connectors. Welded stainless steel tubing with face seal fittings are
used for the highest purity semiconductor applications so that only stainless
steel comes into contact with the weldment. All types of plastic tubing are
permeable to atmosphere to some degree. The Polyflow
®
(polyethylene)
tubing supplied with the Arc Machines equipment is very good. The SEMI
specification recommends PFA plastic tubing, but in either case the plastic
tubing should be restricted to less than 10 feet in length. Specifications for
the various types of plastic tubing listing permeability to oxygen and mois-
ture can be obtained from the plastic tubing manufacturers. The use of rub-
ber or similar type purge hoses is not consistent with high-quality welding.
Some type of diffuser may be used to disperse the argon flow to assure
that the entire weld joint is covered. A diffuser at the connection of the gas
hose to end cap can be used to disperse the argon stream entering the tube
or pipe ID. This can also be accomplished by a filter. Contractors have de-
veloped a variety of devices and techniques to assure that the entire I.D.
weld joint is adequately covered by purge gas.
Analytical equipment such as oxygen and moisture analyzers can be
used to verify that purge gas exiting the I.D. of the tube or pipe being weld-
ed has approximately the same level of purity as the source gas. If it does
not, the location of the leak(s) must be found.