Gas type, Argon – Arc Machines 307 User Manual
Page 154
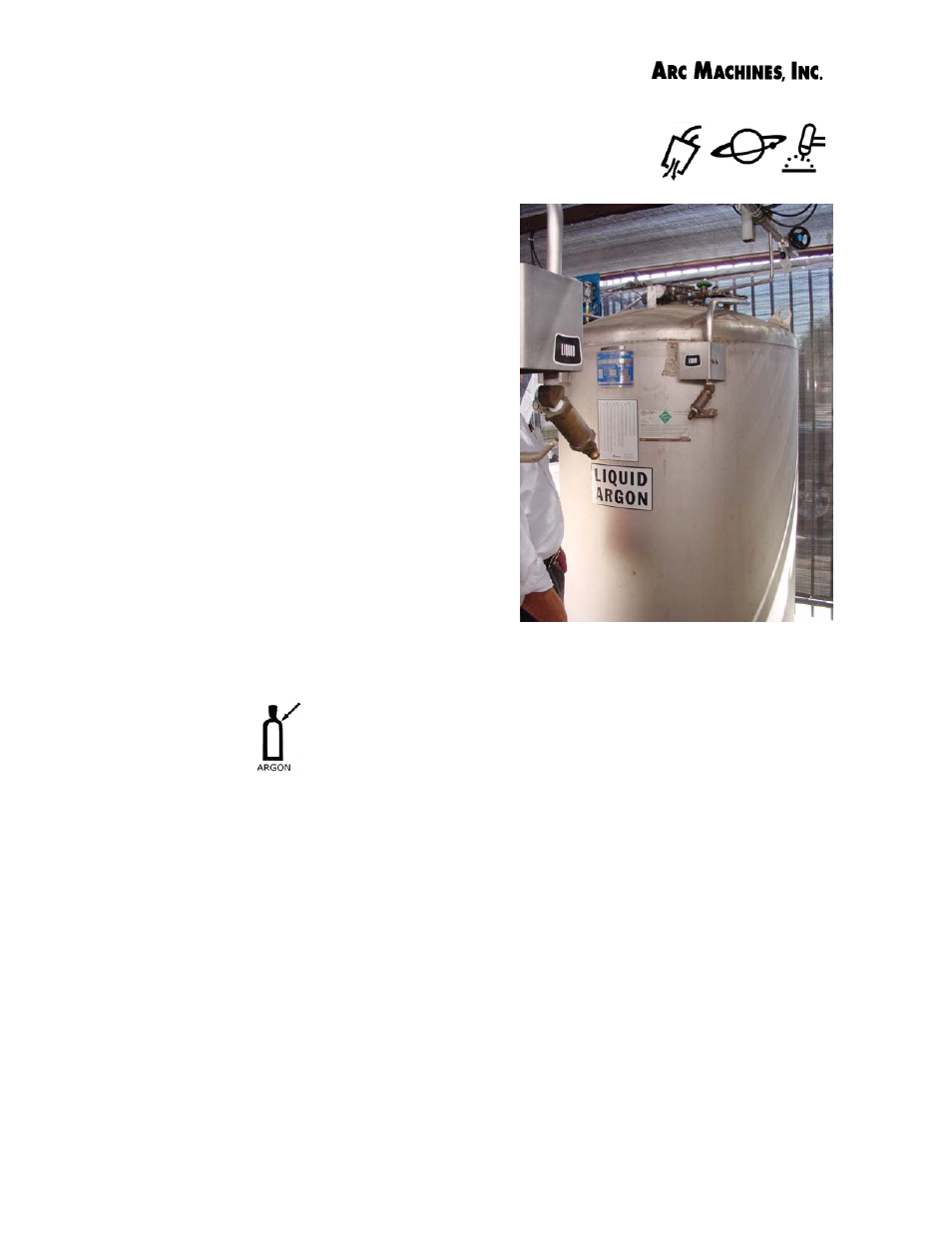
Arc Machines, Inc. Model 307 Orbital Tube Welder Training
Document No. 740096
Chapter 16. Page 1.
Rev. A
C
hapter 16. Purging Requirements
for Orbital Welding
etals have a tendency to oxidize in
air. This tendency is accelerated
when heated to welding tempera-
tures. Moisture, and even nitrogen, which
forms the largest component of the at-
mosphere, may have detrimental effects
on some metals. In the GTAW process an
inert shielding gas is supplied to the
weld head to protect the electrode, the
molten weld puddle and adjacent areas
from oxidation. For autogenous orbital
welding in enclosed weld heads, the head
forms a chamber of inert gas providing
protection of the entire O.D. weld joint.
A backing or purge gas is applied to the
I.D. of the weld joint to prevent the for-
mation of oxides or other detrimental
surface substances and to provide pres-
sure for the weld profile. Backing gas is
required for high-purity orbital welding
and for tack welding (if tack welds are
permitted).
Gas type
Argon
Argon is the most commonly used gas for both shield and backing during
GTA welding of 316L stainless steels in the biotechnology and pharmaceu-
tical industries, while a gas mixture containing 1 to 5% hydrogen is often
used in the semiconductor industry. The type of gas used as a shield gas
has a profound effect on the character of the arc and the depth of weld pen-
etration. Gas mixtures of helium and argon (75% helium/25% argon), as
well as argon and hydrogen (95% argon/5% hydrogen), provide a hotter
arc than pure argon and deeper penetration at the same current settings.
The gas type is considered to be an essential variable for weld procedure
qualifications and a change from one gas type to another or to a gas mixture
requires requalification of the welding procedure. Welding operators must
also be requalified when there is a change of gas type or gas mixture.
Large argon dewar outside a cleanroom is used
for purging welds on high-purity semiconductor
and pharmaceutical piping assemblies. Photo
courtesy of Murray Company.
Ar
He/Ar
Ar/H
2
M