Chapter 12. weld procedure optimization, Making a test run, Hapter 12. weld procedure optimization – Arc Machines 307 User Manual
Page 130
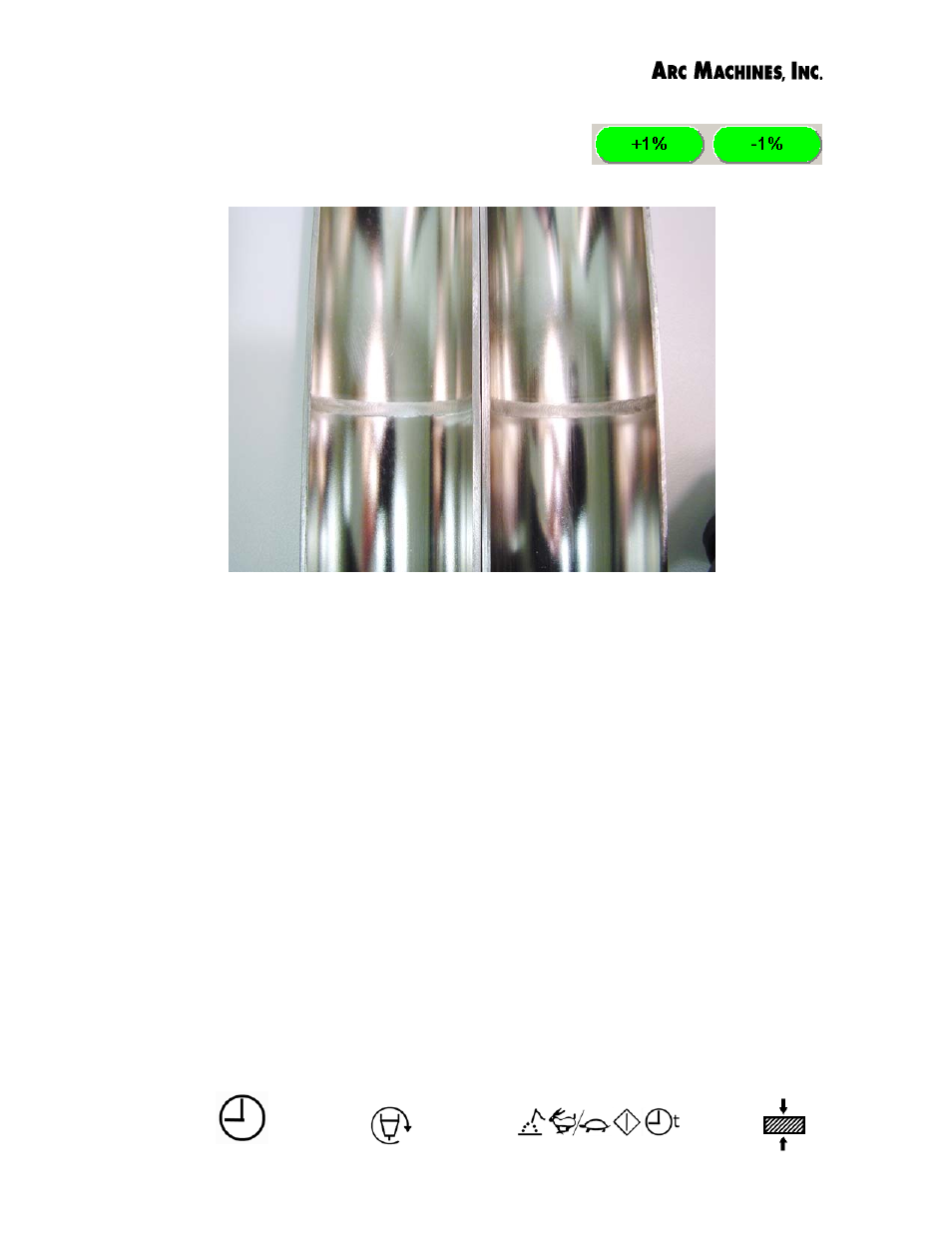
Arc Machines, Inc. Model 307 Orbital Tube Welder Training
Document No. 740096
Chapter 12. Page 1.
Rev. A
C
hapter 12. Weld Procedure
Optimization
H
eat-to-heat variations in stainless steel may make it necessary to adjust
weld parameters, particularly amperes, for individual heats of material. The
objective of this chapter is to guide the operator to achieve an optimized
weld program from one that is untried. The weld should have complete
uniform penetration around the entire circumference, have good alignment
of weld components and be well purged on the ID and OD. See Chapter 17
Weld Criteria for more specific industry requirements.
Making a Test Run
Before attempting to weld with an untried weld schedule, make a Test Run.
In a Test Run, the weld head rotor rotates at the programmed RPM without
striking an arc.
A Test Run is done to make sure that the Total Time in all levels (excluding
Downslope) is adequate to achieve a complete revolution (360°) plus
tie-in. Downslope must be set to zero for the Test Run and
re-entered for the actual weld.
Total Time includes Time for One Revolution (360°), plus Travel Start
Delay time, plus time for the proper amount of overlap or tie-in which
should be equal to time to travel a distance of at least 2 wall thicknesses.
Weld coupon on 1.500 inch O.D. 316L stainless steel cut open for evaluation
of the I.D. surface for a bioprocess application. Photo courtesy of ProTech Process, Inc.
= t
Total Time
360° +
+ 2Xt
∑