Data blocks require i/o configuration, Engineering units – Rockwell Automation 1771-QI,D17716.5.126 PLASTIC MOLD.MODULE User Manual
Page 78
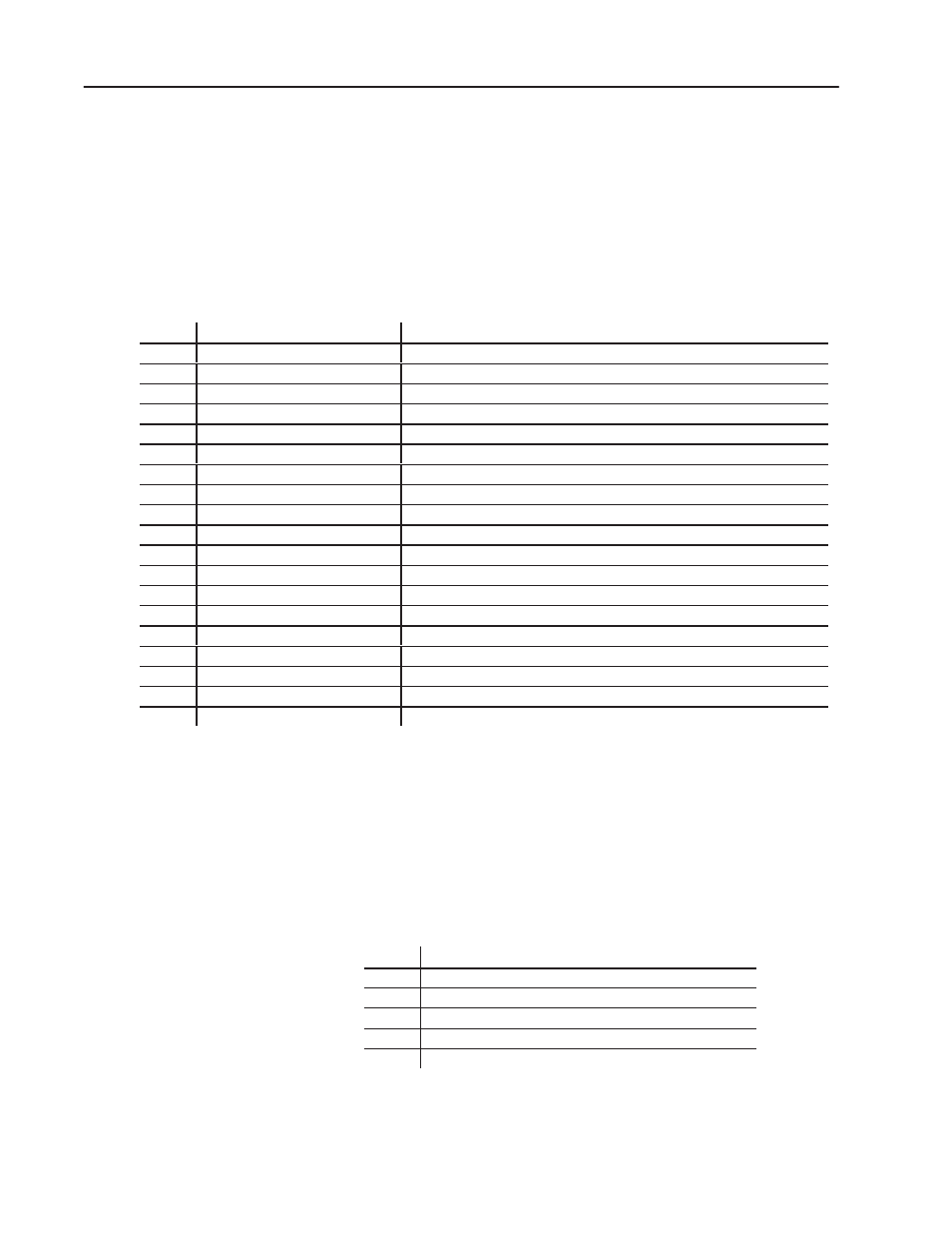
3–2
Status Word/Bit Descriptions
Publication 1771-6.5.126 – March 1998
Notes: For [ ] engineering units, see page 2.
The QI module decodes its own I/O configuration based on parameters
that you provide in the Module Configuration Command Block (MCC).
I/O configuration determines which of the command and status blocks
the module supports. For the module to support command and status
blocks, you must establish the following position input:
•
Connect a ram (screw) position sensor to input 1.
In the listings of status blocks, each stored-value word is followed by
a bracketed [ ] 2-digit number code denoting the engineering units
and range associated with the value as shown in the following table:
#Code
Type of Block
Units and Range
01
Ram (Screw)
Pressure (0000.0 to 9999.0 PSI or 000.0 to 999.9 Bar)
04
Cavity
Pressure (00000.0 to 20000.0 PSI or 0000.0 to 2000.0 Bar)
05
Ram (Screw)
Percent of maximum velocity (00.00 to 99.99%)
06
Ram (Screw)
Velocity along axis (00.00 to 99.99 in. per sec. or 000.0 to 999.9 mm per sec.)
11
Ram (Screw) Measured from zero
Incremental distance (00.00 to 99.99 in. or 000.0 to 999.9 mm.)
12
Ram (Screw) Measured from MCC13
Incremental distance (00.00 to 99.99 in. or 000.0 to 999.9 mm.)
17
Measured as noted in text
Incremental distance (00.00 to 99.99 in. or 000.0 to 999.9 mm.)
18
Measured as noted in text
Incremental distance (00.00 to 00.99 in. or 000.0 to 009.9 mm.)
19
Percent signal output (00.00 to 99.99%)
20
Percent signal output per second (0000. To 9999.)
21
Time measured in seconds (00.00 to 99.99)
22
Time measured in seconds (000.0 to 999.9)
23
Time measured in seconds (00.00 to 00.99)
24
Input signal range (00.00 to 10.00 or 01.00 to 05.00 or 04.00 to 20.00)
25
Screw rotational speed (000.0 to 999.9 RPM)
26
Time (algorithm) (00.00 to 9.99 minutes)
27
Inverse time (algorithm) (00.00 to 99.99 inverse minutes)
28
Inverse time (algorithm) (00.00 to 99.99 inverse seconds)
31
Percent (00.00 to 99.99%)
The System Status Block (SYS) reports system status.
The module can always return the System Status Block to the host
processor. It returns this block after each block transfer read (BTR)
request from the PLC processor unless the previous block transfer
write (BTW) to the module was a valid dynamic command block
(DYC) containing a request for some other status block.
The QI module can return any of these status blocks:
Block
Description
IPS
Injection Profile Status Block
HPS
Pack/Hold Profile Status Block
PPS
Plastication Profile Status Block
PTS
Process Trace Status Block
RLS
Inject ERC Values Status Block
After you configure the QI module with a valid MCC, the module
determines if it has access to ram (screw) position data from the ram
(screw) position sensor connected to input 1.
Data Blocks Require I/O
Configuration
Engineering Units
Status Blocks for
Reporting System and
Ram (Screw) Position
Status