1 error causes, 2 error location – HEIDENHAIN TNC 415 (259 9x0) Service Manual User Manual
Page 83
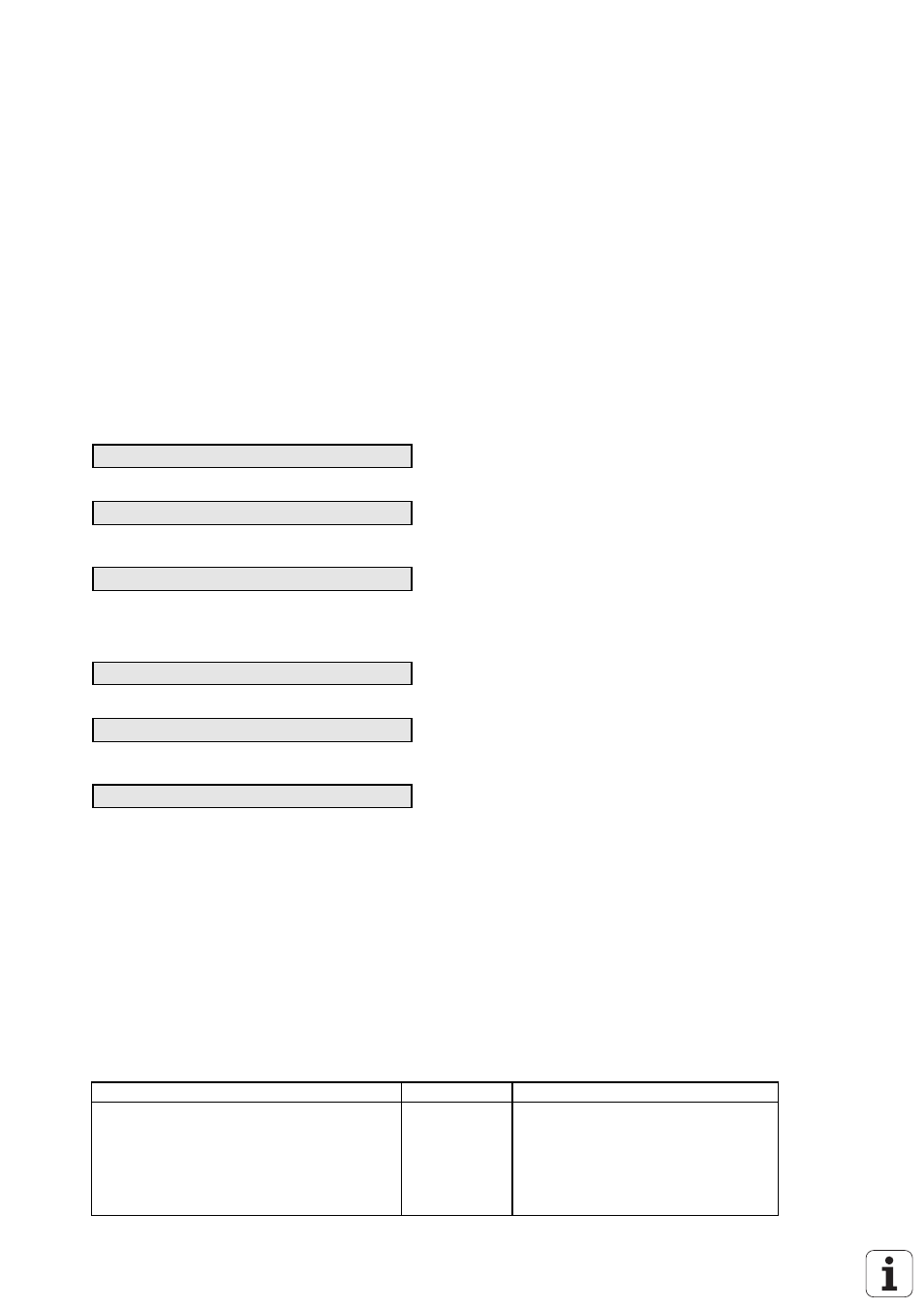
SERVICE MANUAL TNC 415B/425
Page 78
Issue: 20.08.95
13.2 Error Messages for Axes with Integral Digital
Speed Controller
With the integral digital speed controller there are two encoder inputs for each axis:
Encoder inputs for the actual position:
encoder 1:
input X1
encoder 2:
input X2
encoder 3:
input X3
encoder 4:
input X4
encoder 5:
input X5
encoder S:
input X6
Encoder inputs for the actual speed:
encoder 1:
input X15
encoder 2:
input X16
encoder 3:
input X17
encoder 4:
input X18
encoder 5:
input X19
Therefore, there are two groups of error messages:
Monitoring of actual position capture (X1, X2, X3, X4, X5, X6)
ENCODER
A = signal amplitude error, position encoder
ENCODER
B = signal frequency error, position encoder
Y = CPU number
1 = main processor
2 = geometry processor
3 = CLP processor
ENCODER
C = error with distance-coded scales, position encoder
Monitoring of actual speed capture (X15, X16, X17, X18, X19)
ENCODER
A = signal amplitude error, speed encoder
ENCODER
B = signal frequency error, speed encoder
Y = CPU number
1 = main processor
2 = geometry processor
3 = CLP processor
ENCODER
C = error with distance-coded scales (speed encoder)
13.2.1 Error Causes
•
Glass scale contaminated or damaged
•
Scanning head contaminated or defective
•
Cable damaged
•
Encoder input of the logic unit (LE) defective
13.2.2 Error Location
In order to determine whether the one of the encoders of an axis or one of the encoder inputs on the logic
unit is defective, the encoders can be switched at the logic unit. For this purpose the corresponding machine
parameters must be altered as well (always change both parameters!):
Function
MP
Entry value
Allocation of the axes
X
to the encoder inputs
Y
Z
IV
V
0 = X1 (pos.) / X15 (speed)
1 = X2 (pos.) / X16 (speed)
2 = X3 (pos.) / X17 (speed)
3 = X4 (pos.) / X18 (speed)
4 = X5 (pos.) / X19 (speed)
5 = X61) (pos.)
1)
X6 can be used for a machine axis, if no oriented spindle stop is required.