HEIDENHAIN TNC 415 (259 9x0) Service Manual User Manual
Page 16
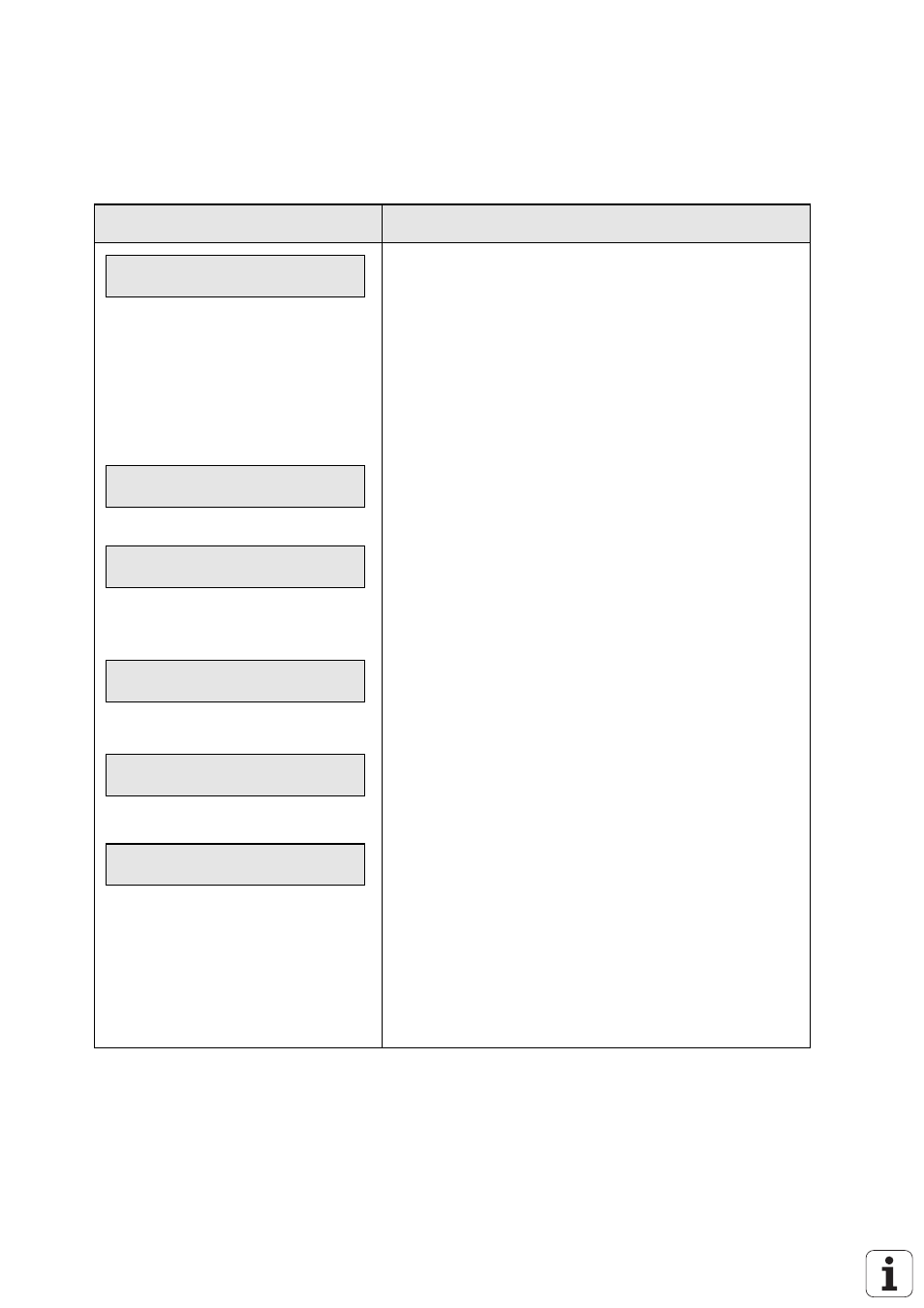
SERVICE MANUAL TNC 415B/425
Page
13
Issue: 20.08.95
Error Messages GROSS POSITIONING ERROR:
Axes with Integrated Digital Speed Controller
Display (blinking)
Error Cause
GROSS POSITIONING ERROR
GROSS POSITIONING ERROR
GROSS POSITIONING ERROR
GROSS POSITIONING ERROR
GROSS POSITIONING ERROR
GROSS POSITIONING ERROR
Positioning (Servo Lag) Monitoring
- Operation with feed forward control:
position monitoring range exceeded
(range defined in MP1420.X)
- Operation with servo lag:
servo lag monitoring range exceeded
(range defined in MP1720.X)
- Operation with gantry axes:
positions of master and slave axes deviate by more than
the value set in MP855.X. (displayed axis = slave axis)
Monitoring of the Analogue Voltage Limit
- The nominal voltage calculated by the control has
reached its limit of
±
10 V (
±
20 V for spindle).
(only with feed forward control)
Movement Monitoring
- The difference between the path information of the
position encoder (LS) and that of the speed encoder
(ROD) has reached the tolerance limit defined in
MP1970.x.
Standstill Monitoring
- The deviation from the nominal position of an axis in
standstill has exceeded the value programmed in the
machine parameter MP1110.x.
Monitoring of the Offset Voltage
- The offset voltage limit of 100mV has been reached
during an automatic offset adjustment with MP1220.
Monitoring of the Integrated Digital Speed
Controller
- The monitoring limit of the integrated speed controller
Y = CPU number 1 = main processor
2 = geometry processor
3 = CLP processor
Error Location
When the error message GROSS POSITIONING ERROR is displayed, the error may be located
in any element of the closed loop.
e.g.: - Error in control (e.g. CLP board)
- Excessive offset voltage at the servo amplifier
- Monitoring function of servo amplifier has responded
(e.g. monitoring of current intensity)
- Electrical defect at the servo amplifier
- Motor, tachometer, encoder or cabling defective
- Mechanical error (bearing, spindle, guides)
- Excessive mechanical forces on a drive