HEIDENHAIN TNC 415 (259 9x0) Service Manual User Manual
Page 127
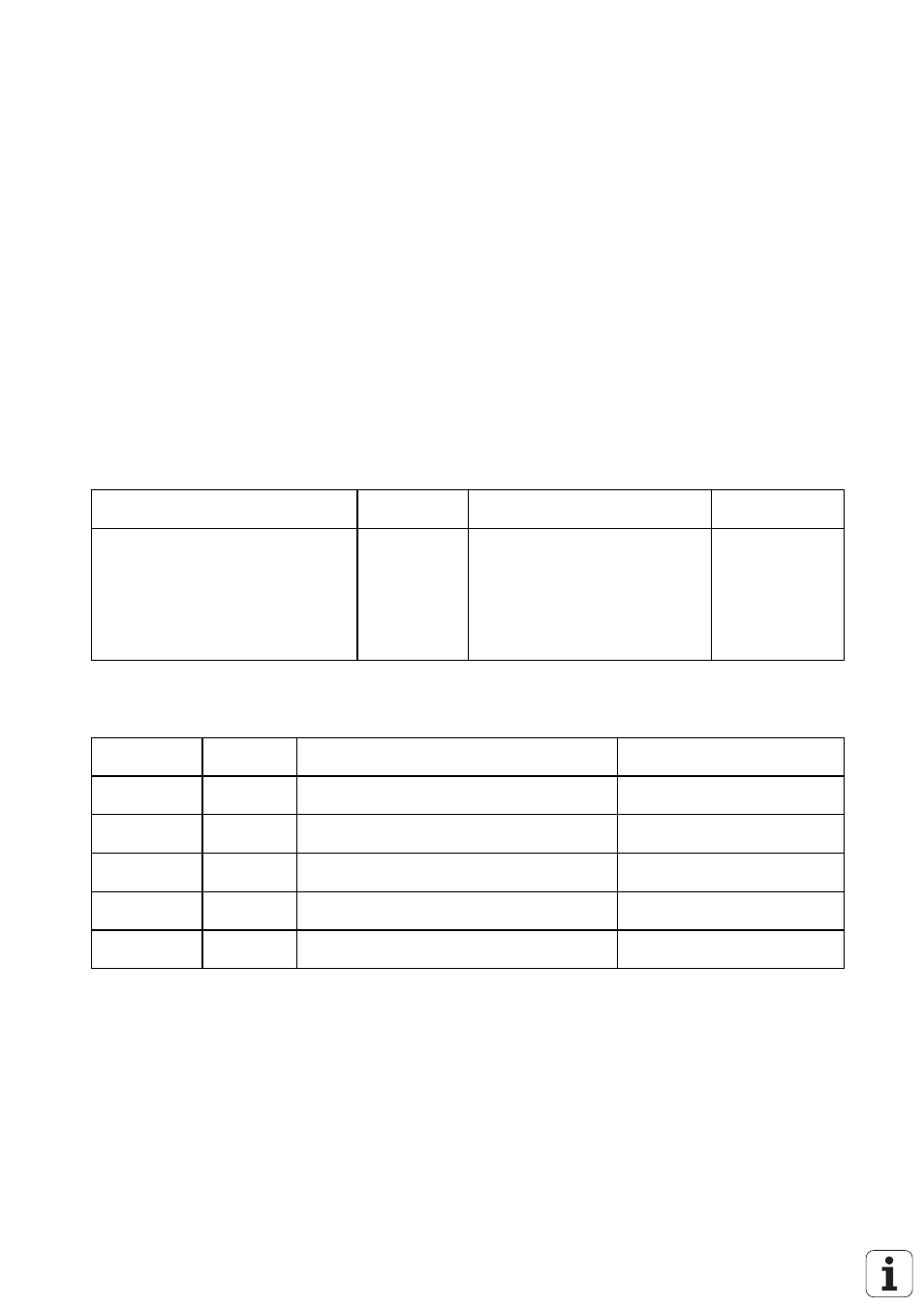
SERVICE MANUAL TNC 415B/425
Page 122
Issue: 20.08.95
18.2.2 Axes with Integral Digital Speed Controller
Depending on the machine parameter MP1900 the driving axes of TNC 425/E are individually defined as
analogue axes (as TNC 415 B/F) or as digital axes.
With axes with integral digital speed controller (corresponding bit of MP1900 = 1) a TTL voltage
is output at the analogue output.
If however, the axis does not move due to a defect, and if you want to test whether the error is inside or
outside the control, the following steps are recommended:
•
Switch off the main switch.
•
Disconnect the nominal value line from the connector X8 and check for short-circuit and line
disconnection.
•
If the nominal value line is in order, leave it disconnected and connect the test adapter to
the connector X8.
•
Switch on main switch and machine control voltage.
•
Switch the position display to LAG (servo lag); see section 18.3.
•
Define the axis to be checked as analogue controlled axis (MP1900, corresponding bit = 0)
Function
MP
No.
Bit
Entry range
Original
1)
Entry Values
Axes with
digital speed controller
X
Y
Z
IV
V
0 to 31
0 =
analogue-controlled axis
+1 = X-axis digital controlled
+2 = Y-axis digital controlled
+4 = Z-axis digital controlled
+8 = IV. axis digital controlled
+16 = V. axis digital controlled
•
The following machine parameters need to be checked and adapted. (Do not forget to re-enter the
original values after having finished the test!)
MP
Entry
Value
Function
Original Entry Values
30
[
mm
]
Servo lag monitoring (cancellable),
feed forward control
30
[
mm
]
Servo lag monitoring (EMERG. STOP),
feed forward control
9.99
[
V
]
Movement monitoring
300
[
mm
]
Servo lag monitoring (cancellable),
trailing operation
300
[
mm
]
Servo lag monitoring (EMERG. STOP),
trailing operation
•
Turn the override potentiometer of the keyboard unit completely to the left and start reference mark
traverse for the defective axis.
•
Check the axis enable for the defective axis at the servo amplifier.
•
Check the screen display
* (control ready for operation) must be switched on, the F of the feed rate display must be lit normally
(if the display is inverse the feed rate enable is missing) and the symbol for "axis not in position loop"
(e.g.
→|←
X) must not follow the position display.
•
Turn the override potentiometer slowly to the right and turn it back left before the servo lag display
reaches the limit of the position monitoring.