Figure 71: microstrip cross section below, Figure 72: strip line cross section below, Figure 72: strip line cross section below) – Kontron COMe Starterkit Eval T2 User Manual
Page 176
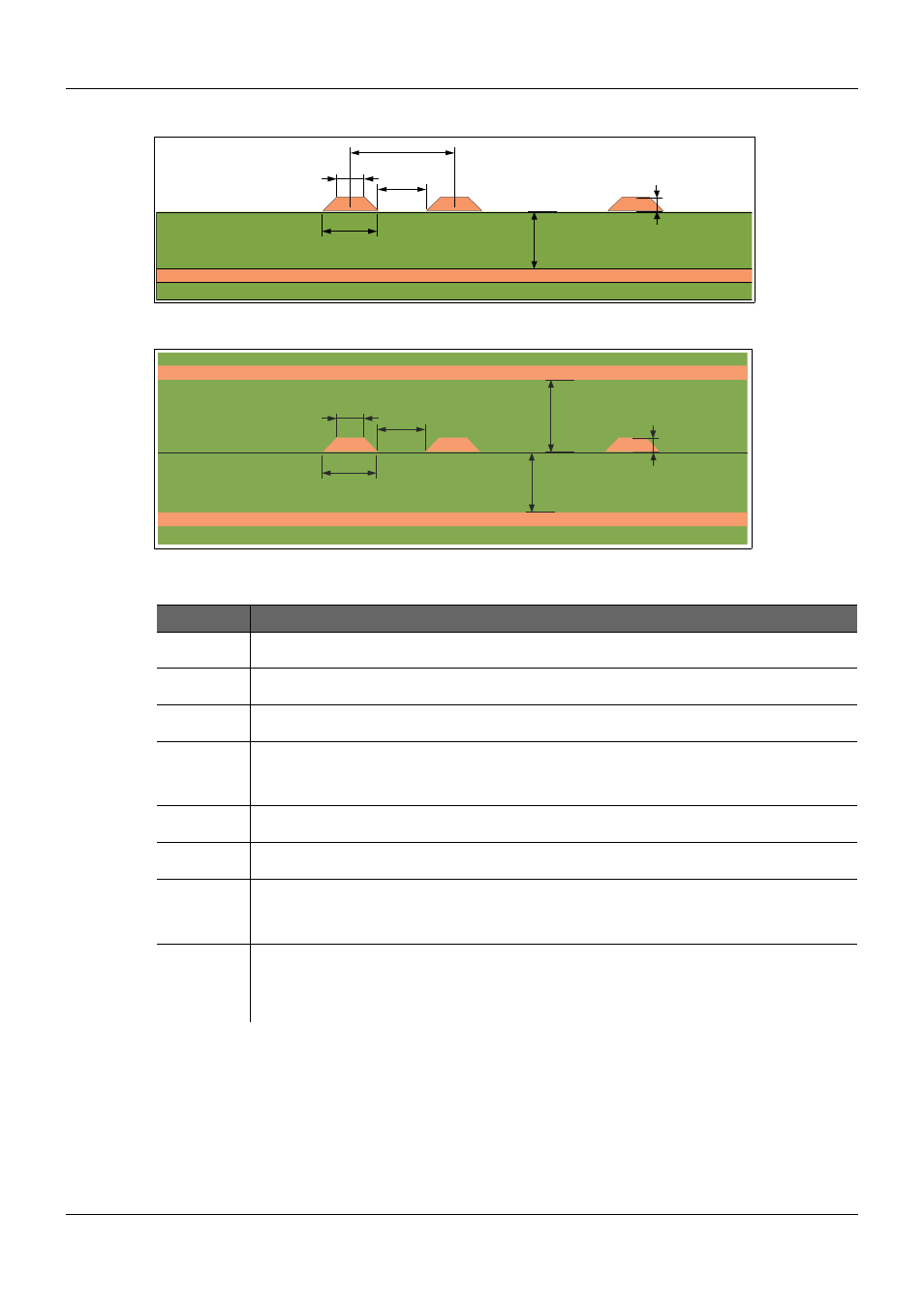
Carrier Board PCB Layout Guidelines
Figure 71:
Microstrip Cross Section
Figure 72:
Strip Line Cross Section
Table 60:
Trace Parameters
Symbol
Definition
ε
r
1
Dielectric constant of material between the trace and the reference plane. Increasing ε
r
1 results in a lower
trace impedance.
ε
r
2
Dielectric constant of the material between the 2
nd
reference plane (stripline case only).
Usually ε
r
1 and ε
r
2 are the same. Increasing ε
r
2 results in a lower trace impedance.
H1
Distance between the trace lower surface and the closer reference plane.
Increasing H1 raises the trace impedance (assuming that H1 is less than H2).
H2
Distance between the trace lower surface and the more distant reference plane (stripline case only).
Usually H2 is significantly greater than H1.
When this is true, the lower plane shown in the figure is the primary reference plane. Increasing H2 raises
the trace impedance.
Pair Pitch
The center-to-center spacing between two traces in a differential pair. Increasing the pair pitch raises the
differential trace impedance.
S
The spacing or gap between two traces in a differential pair. The pair pitch is the sum of S and W1.
Increasing S raises the differential trace impedance.
T
The thickness of the trace. The thickness of a ½ oz. inner layer trace is about 0.0007 inches. The
thickness of a 1 oz. inner layer trace is about 0.0014 inches. Outer layer traces using a given copper
weight are thicker, due to plating that is usually done on outer layers. Increasing the trace thickness lowers
trace impedance.
W1, W2
W1 is the base thickness of the trace. W2 is the thickness at the top of the trace. The relation between W1
and W2 is called the “etch factor” in the PCB trade. For rough calculations, it can be assumed that W1 =
W2. The etch factor is process dependent. W2 is often about 0.001 inches less than W1 for ½ oz inner
layer traces; for example, a 5 mil (0.005 inch) nominal trace will be 5-mil wide at the bottom and 4-mil wide
at the top. Increasing the trace-width lowers trace impedance.
PICMG
®
COM Express
®
Carrier Board Design Guide
Rev. 2.0 / December 6, 2013
176/218
Power/GND Plane
ε
r
1
Pair Pitch
S
H1
T
W2
W1
ε
r
1
ε
r
2
Power/GND Plane
Power/GND Plane
S
H1
H2
T
W2
W1