Rockwell Automation 1397 DC Drive Firmware 2.xx User Manual
Page 107
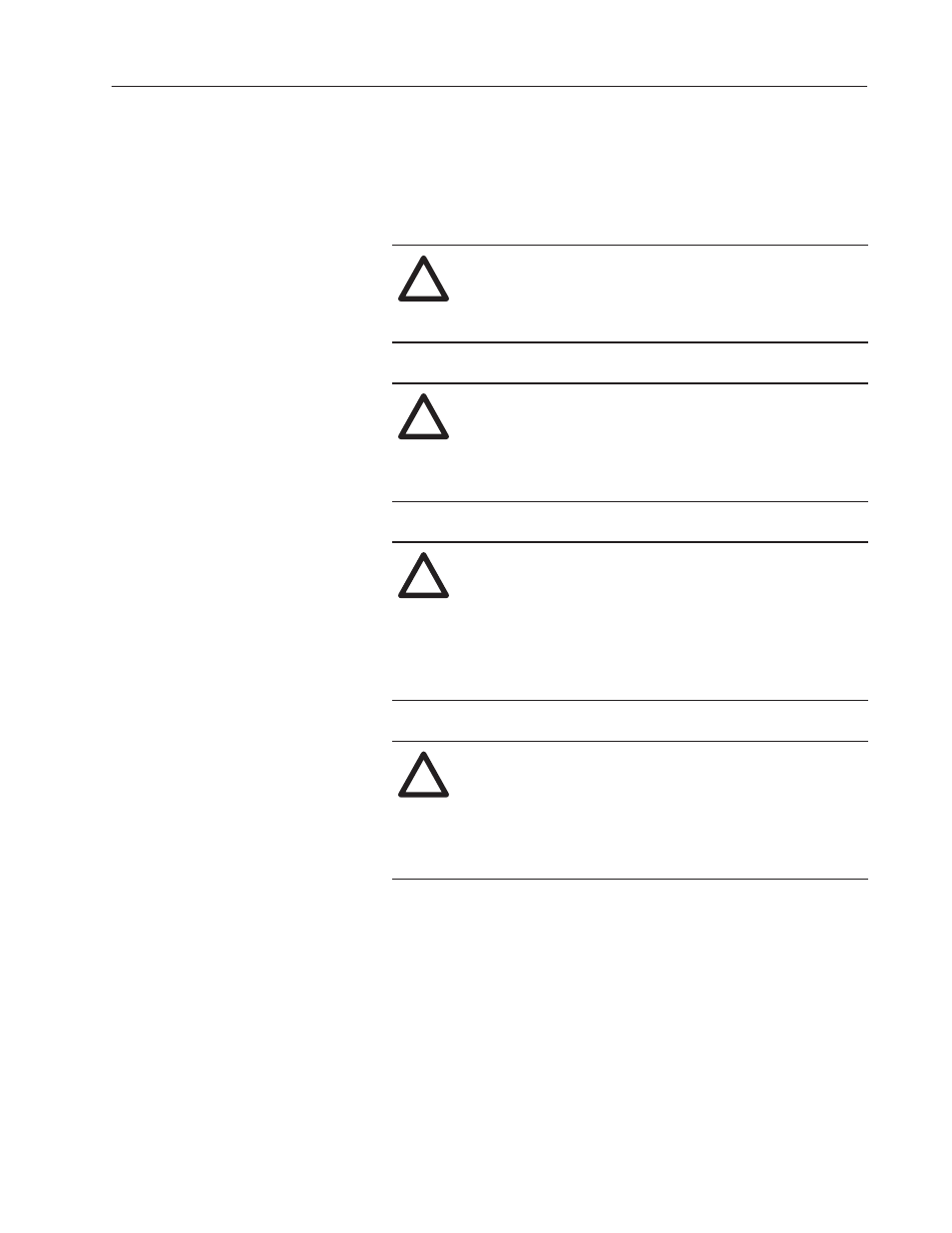
4–35
Start–Up and Adjustment
Publication 1397-5.0 — June, 2001
The 1397 utilizes digital speed regulator and a digital current
regulator to control the DC motor. These regulators (or “loops”)
may be automatically tuned by setting the appropriate tuning
parameter and running the Drive when coupled to the machine
(load).
!
ATTENTION: The motor will rotate during
auto-tuning. Stay clear of rotating machinery to avoid
contact with rotating parts. Failure to observe this
precaution could result in bodily injury.
!
ATTENTION: Before starting auto-tuning, it must be
verified that no overhauling or hanging loads are on the
motor. Auto-tuning will not operate properly if this
type of load exists. Failure to observe this precaution
could result in bodily injury.
!
ATTENTION: Auto-tuning must not be performed on
drives with motors that are mechanically coupled to
one another through the process material. However,
the Drive can be auto-tuned with load applied and with
inertia connected. Failure to observe this precaution
could result in damage to, or destruction of, the
equipment.
!
ATTENTION: Auto-tuning will not operate properly
if prior adjustments in Chapter 4 are not performed.
Perform all prior adjustment procedures contained in
Chapter 4 before proceeding. Failure to observe this
precaution could result in damage to, or destruction of,
the equipment.
IMPORTANT: Speed loop autotuning can only be performed on
Drives with either pulse encoder feedback or analog tachometer
feedback.
Current loop autotuning can be performed on Drives with encoder
feedback, analog tach feedback or which are armature voltage
controlled. This can also be performed if the Drive is configured as
a current regulator (J15 = Current).
Autotuning