Common guidelines for all applications, Common guidelines for all applications. f-3 – Rockwell Automation 22D PowerFlex 40P User Manual, FRN 3 User Manual
Page 171
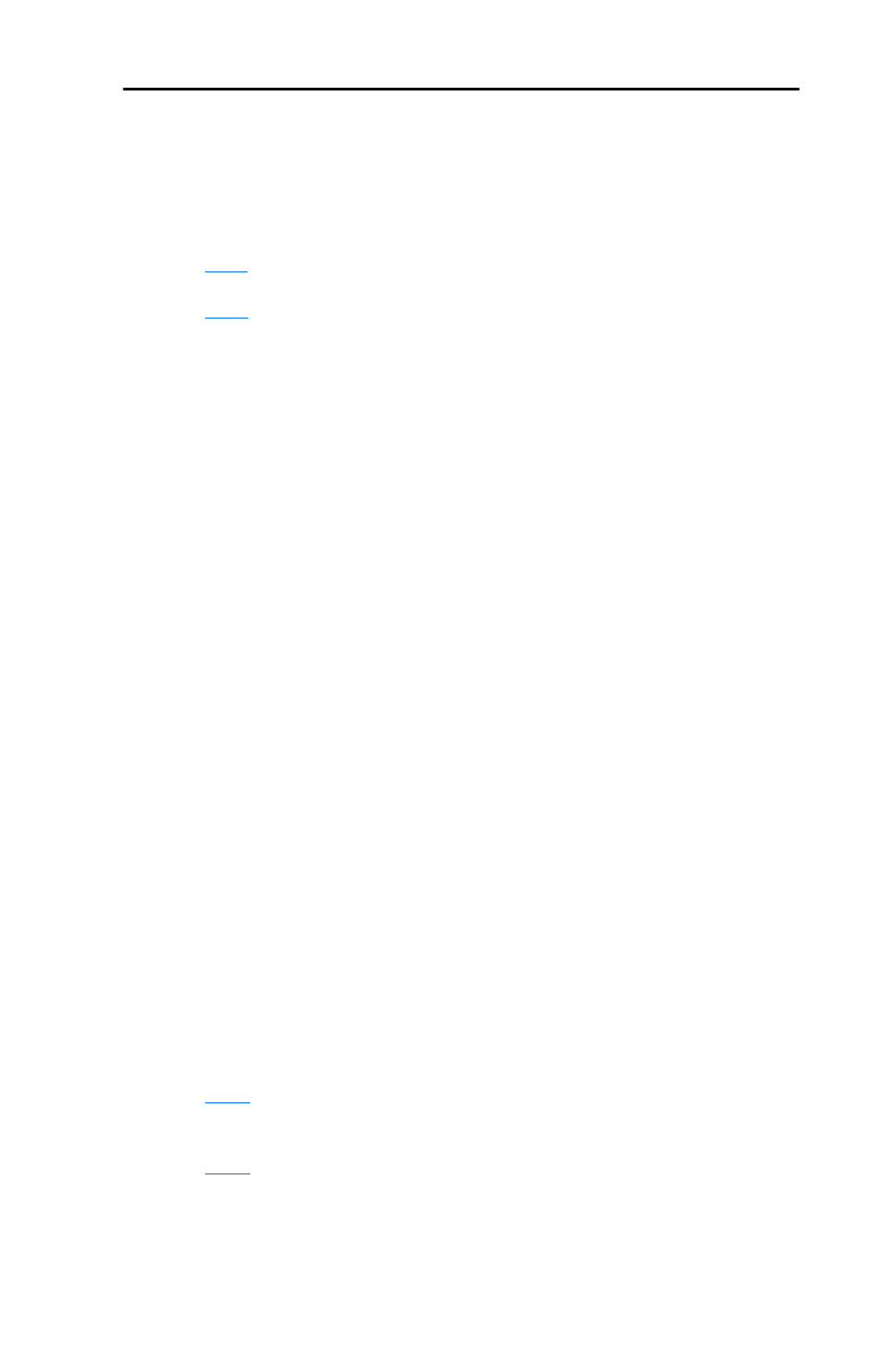
Encoder Usage and Position StepLogic Application
F-3
Common Guidelines for All Applications
The position regulator can be configured for operation appropriate for a
variety of applications. Certain parameters will need to be adjusted in all
cases.
[Speed Reference] must be set to option 9 “Positioning”.
[Motor Fdbk Type] must be set to the match the feedback device.
Positioning mode must use E216 [Motor Fdbk Type] option 4.
E216 [Motor Fdbk Type] Options
0 “None” indicates no encoder is used. This can not be used for
positioning.
1 “Pulse Train” is a single channel input, no direction, speed feedback
only. This should not be used for positioning. The Single Channel
selection is similar to a Pulse Train, but uses the standard encoder
scaling parameters.
2 “Single Chan” is a single channel input, no direction, speed feedback
only. This should not be used for positioning. Single channel uses the
standard encoder scaling parameters.
3 “Single Check” is a single channel input with encoder signal loss
detection. The drive will fault if it detects that the input pulses do not
match the expected motor speed. This should not be used for positioning.
4 “Quadrature” is a dual channel encoder input with direction and
speed from the encoder. This may be used for positioning control.
5 “Quad Check” is a dual channel encoder with encoder signal loss
detection. The drive will fault if it detects that the encoder speed does not
match the expected motor speed. FRN 2.xx or greater supports Option 5
“Quad Check” in Positioning mode.
Important: Drives using FRN 1.xx must use option 4 “Quadrature” for
Positioning mode. FRN 1.xx does not support option 5
“Quad Check”.
[Reverse Disable] should be set to option 0 “Rev Enabled” to
allow bidirectional movement necessary for position control.
[Torque Perf Mode] default setting of 1 “Sensrls Vect” is
recommended for most applications to improve the low speed torque for
positioning applications. The autotune routine can be completed to
further improve the drive-motor performance.