Time proportioning, Time proportioning control – Micromod MOD: Modcell 2050R Users Guide User Manual
Page 197
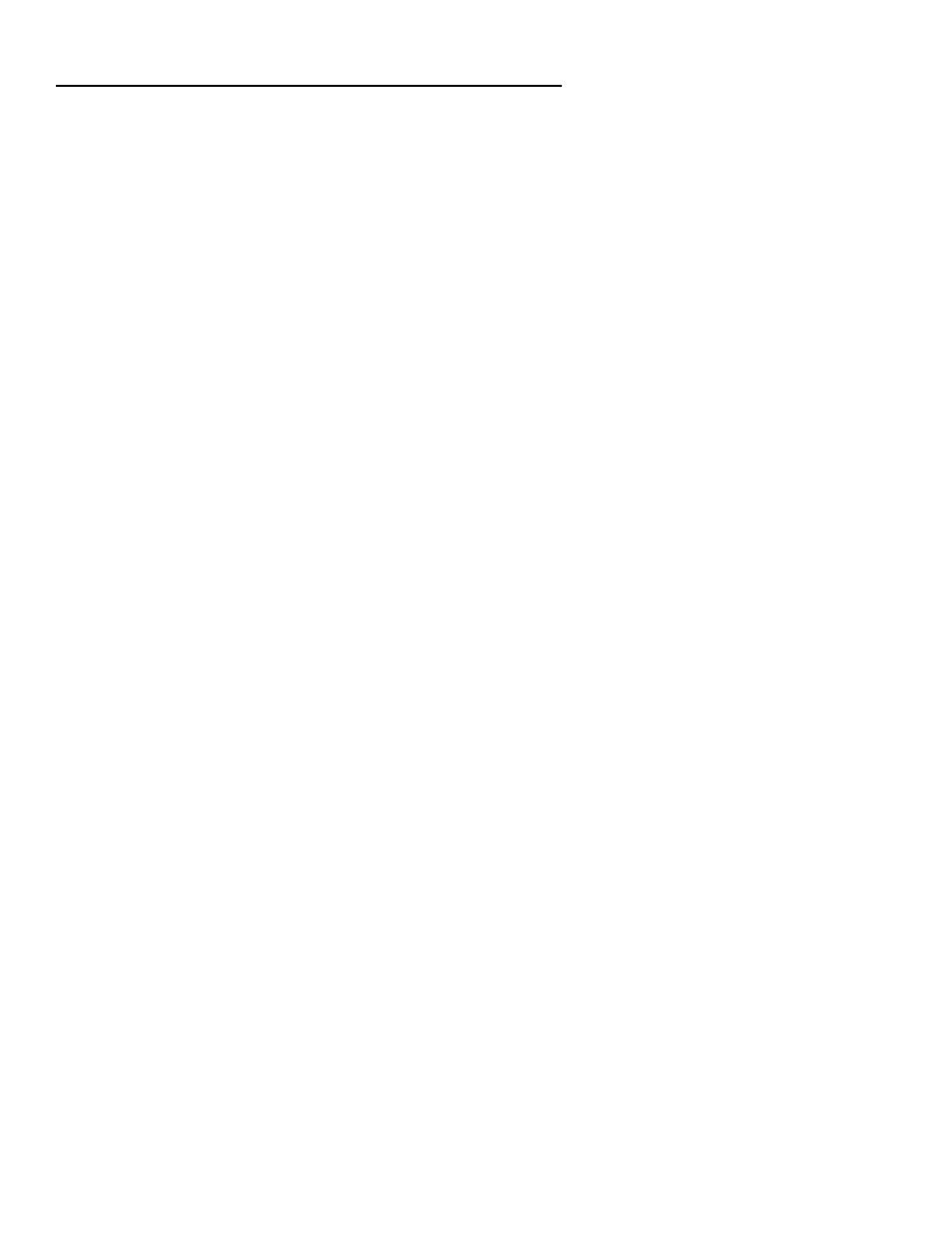
IB-23C650
TIME PROPORTIONING CONTROL
TIME PROPORTIONING CONTROL
DESCRIPTION
Time proportioning control permits PID control to be used in applications
where the control element is an on/off device. The control output is provided
by a mechanical SPDT relay.
The local set-point and manual control adjustments are made using front panel
keys. Process and set-point values are displayed in engineering units, and the
calculated output is displayed in percent of output span.
When the controller is operating in automatic, the control algorithm receives
the active set-point and process input signals. A calculated output signal is
generated based on set-point/process deviation and the configuration of the P,
I, and D responses. Response adjustments are made from the front of the
controller using a series of display prompts provided in the controller firmware.
The calculated output goes to the output driver to control the duty cycle of the
continuously oscillating output relay. The period of oscillation is determined
by the value of the cycle time tuning parameter. The diagram in Figure 26
shows the duty cycle for an output relay with a cycle time setting of 10
seconds. When the calculated output value is 50%, the relay is on for half its
cycle and off for half its cycle. Decreasing output reduces on-time (1 second
on, 9 second off at 10% output), and increasing output proportionally
increases the on-time (9 second on, 1 second off at 90% output).
When the controller is switched to manual, the output relay continues to
oscillate as a function of the cycle time setting the same as in automatic. The
duty cycle is controlled manually by changing the calculated output value via
the front panel keys. Output adjustment while in manual is from 0 to 100% of
span.
191