8diagnostics & error management – Lenze 8400 BaseLine C User Manual
Page 155
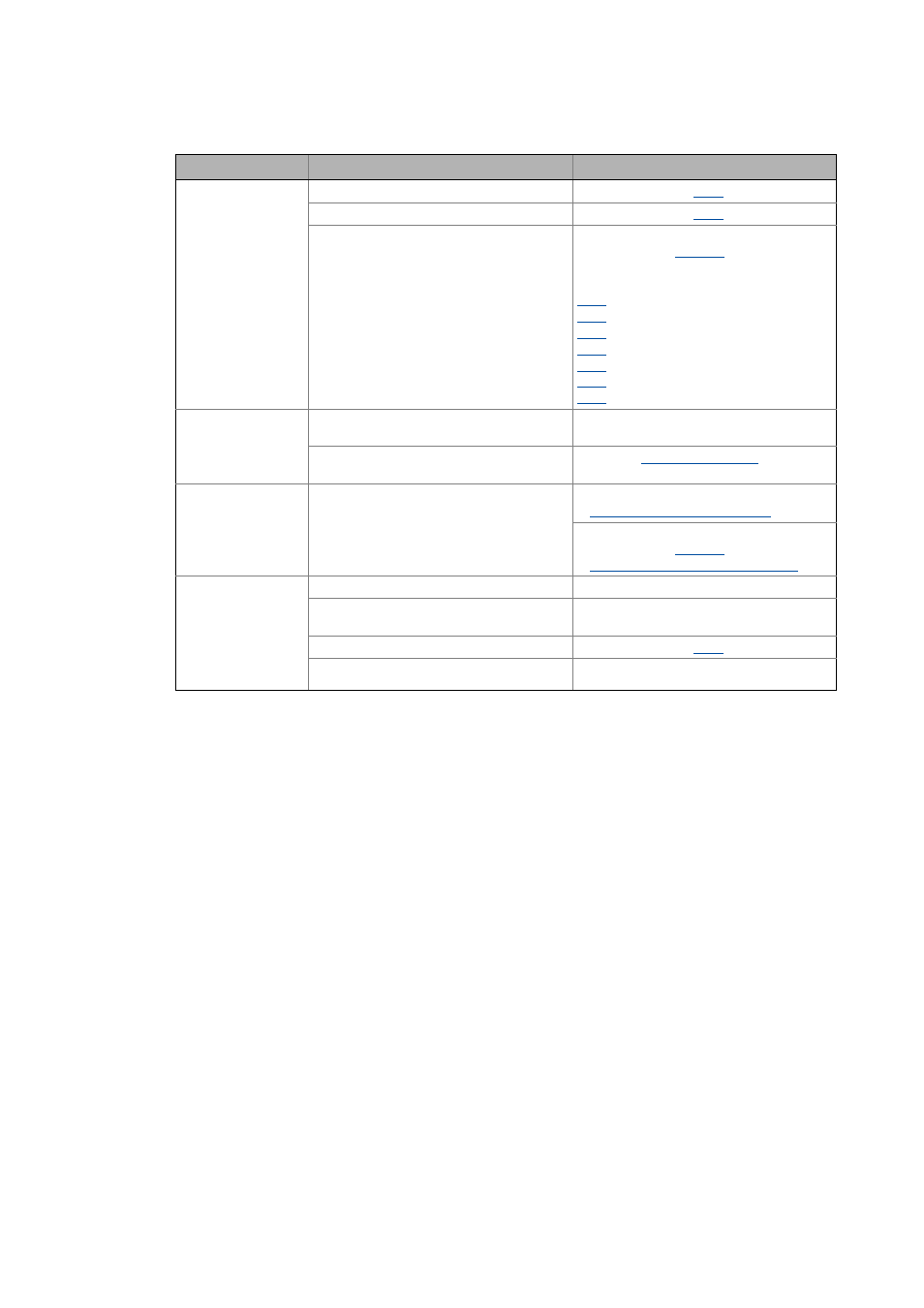
Lenze · 8400 BaseLine C · Reference manual · DMS 1.6 EN · 01/2014 · TD05
155
8
Diagnostics & error management
8.6
Maloperation of the drive
_ _ _ _ _ _ _ _ _ _ _ _ _ _ _ _ _ _ _ _ _ _ _ _ _ _ _ _ _ _ _ _ _ _ _ _ _ _ _ _ _ _ _ _ _ _ _ _ _ _ _ _ _ _ _ _ _ _ _ _ _ _ _ _
Motor consumes too
much current
U
min
boost has been selected too high
V/f base frequency has been selected too low Correct setting with
Rated motor data (stator resistance, speed,
current, frequency, voltage) and cos ϕ and/
or magnetising inductance is not adapted to
the motor data
Carry out automatic motor parameter identi-
fication with the
device command
- or -
Adjust motor parameters manually:
: Motor stator resistance
: Rated motor speed
: Rated motor current
: Rated motor frequency
: Rated motor voltage
: Motor cosine phi
: Motor magnetising inductance
Motor parameter
identification is abor-
ted with error LP1
Motor is too small compared to the rated de-
vice power (>1 : 3)
Use device with lower rated power
DC injection braking (DCB) is active via termi-
nal
Deactivate
Drive behaviour with
vector control is not
satisfactory
different
Optimise or manually adapt vector control
Sensorless vector control (SLVC)
Carry out automatic motor parameter identi-
fication with the
device command
Automatic motor data identification
Torque dip in field
weakening range
or
motor stalling when
being operated in the
field weakening ran-
ge
Motor is overloaded
Check motor load
Motor windings are wired incorrectly
Reverse from star connection to delta con-
nection
V/f base frequency is set too high
Correct setting with
Mains voltage is too low
Increase mains voltage
Maloperation
Cause
Remedy