5 direct setpoint selection, Direct setpoint selection, L-force | plc designer - softmotion – Lenze PLC Designer PLC-Designer (R2-x) SoftMotion User Manual
Page 33
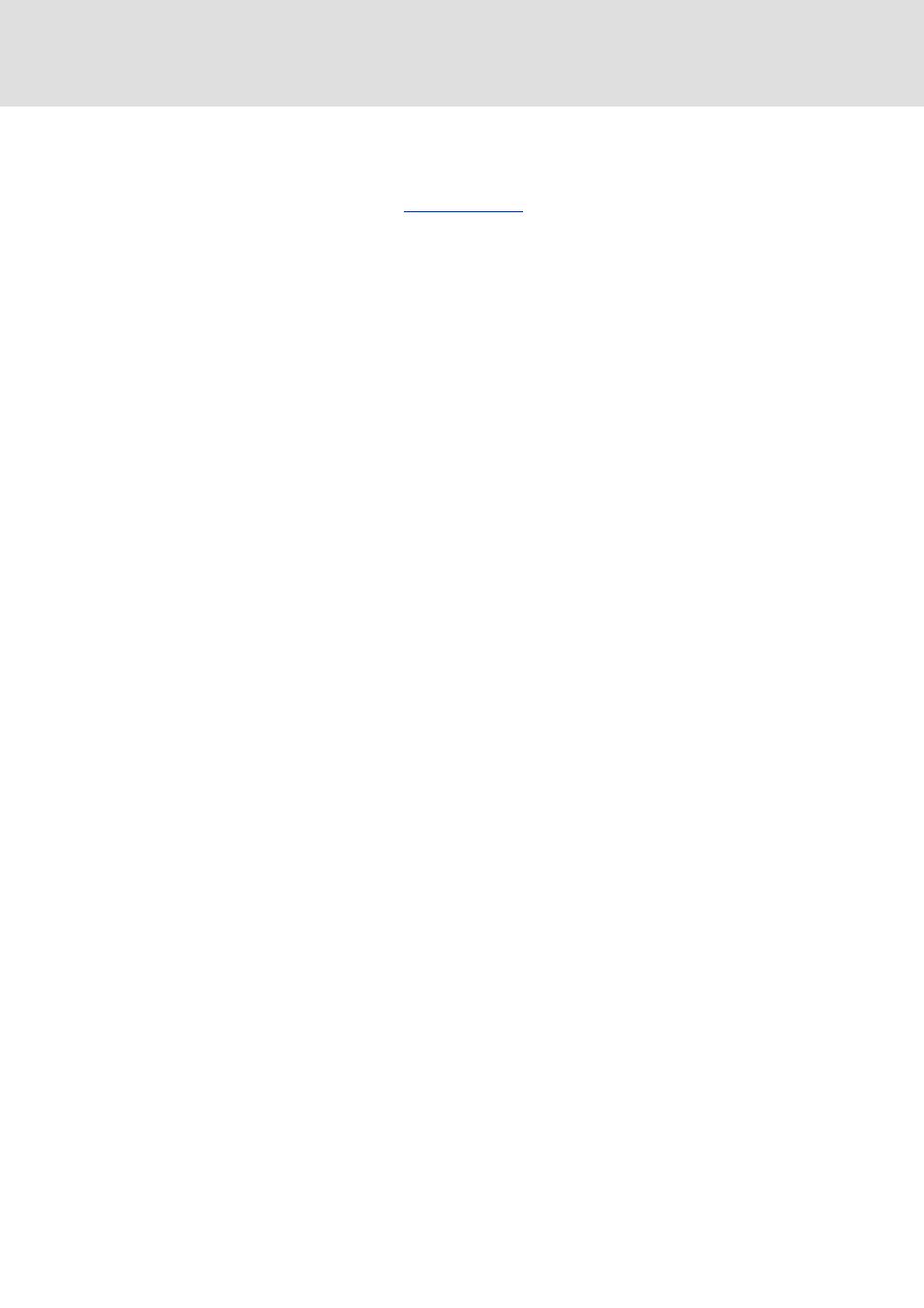
DMS 5.2 EN 03/2011 TD17
L
33
L-force | PLC Designer - SoftMotion
The SoftMotion drive interface
SM_DriveBasic.lib and automatic code generation
3.2.5
Direct setpoint selection
SoftMotion offers the possibility to the user to directly specify setpoints for the position,
speed, and torque/force (see
) and write them to the axis. The
modules provided for this purpose for instance can be used to write profiles to the axis,
which have been self-calculated.
Another important application area is the CNC control where setpoints in X/Y/Z first run
through a transformation block and have to be converted to setpoints for the individual
axes. In order to then transfer these setpoints to the axis and, if required, carry out limit
value monitoring processes, the following POUs are provided.
The POUs SMC_FollowPosition/Velocity write specified setpoints to the axis structure
without further check. The POU SMC_CheckLimits checks the current setpoints with regard
to the compliance of limit values.
The POUs SMC_ControlAxisByPos/Vel are specifically designed for the CNC and offer
additional functions: As long as the limit values are not exceeded, they work like
SMC_FollowPosition/Velocity.
However, if a setpoint step-change occurs (e. g. caused by the sequential execution of two
CNC programs where the end point and starting point does not correspond to each other),
they stop the interpolator, carry out a positioning process to the current set interpolator
position and deactivate the inhibit again, and the interpolator continues its path.
This, these blocks are intended to compensate positions setpoint step-changes. They
detect such a change by checking the compliance with the peak values (of speed and
acceleration). However, the limit values may also be exceeded if the speed of the CNC
program or the override value on the interpolator is too high, or the maximum values of
the axis in the control configuration were set too low (or not at all). The result would be a
jerky run, as the interpolator is always decelerated again as soon as the material speed is
so high that an axis limit is exceeded, and the individual axes are traversed to the
corresponding position. Then the interpolator would start up again to be decelerated again
shortly afterwards.