2 switching between cams, Switching between cams, L-force | plc designer - softmotion – Lenze PLC Designer PLC-Designer (R2-x) SoftMotion User Manual
Page 100
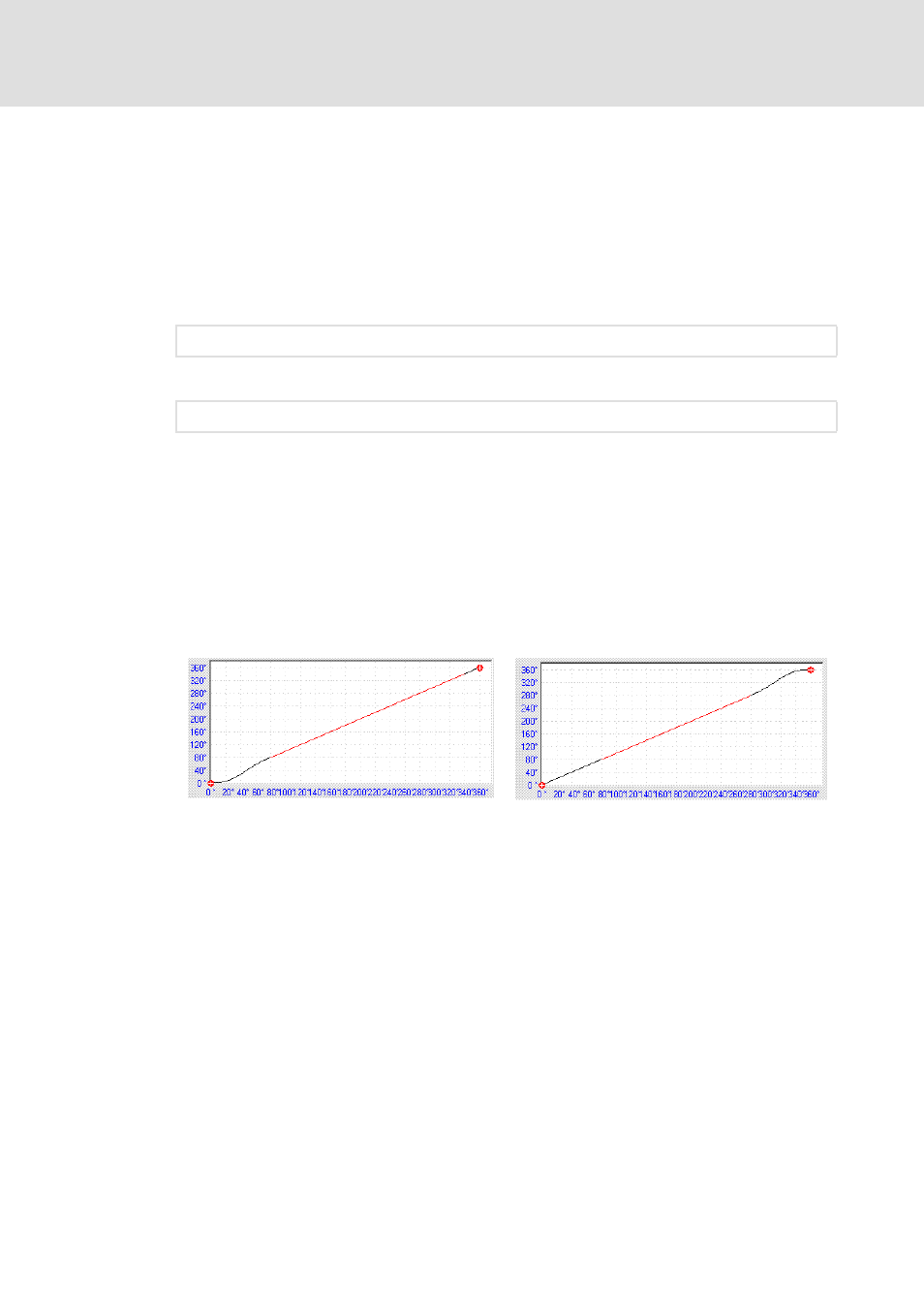
L-force | PLC Designer - SoftMotion
CAM editor
Using cams
100
L
DMS 5.2 EN 03/2011 TD17
5.6.2
Switching between cams
In principle, switching between cams is possible at any time. Please note the following: on
a rising edge, the slave setpoint position is strictly determined by the current master
position (with master offset and master scaling applied) and the cam used, and it is only
modified by means of slave offset and slave scaling. If the master or slave interval of the
cam and the actual position interval of the drives are different, this will result in further
offsets of the master and slave position for each cam cycle/drive revolution completed.
Hence, the simple function equation.
no longer applies, and is replaced by:
where Offset1 and Offset2 can change at the end of each cam.
As a result, if the MC_CamIn cam POU is restarted (rising edge at bExecute), interpreting
this as a completely new action, it will delete its memory and consequently its Offset1 and
Offset2, and use the original equation. This can produce a completely different slave
setpoint. For this reason, you should only restart the MC_CamIn FB if you are about to
process a different cam.
When switching between cams, please note:
Example involving a switch from Cam1 to Cam2:
(1) The velocities and accelerations of the end point of the last cam and the new cam
should match in order to avoid jumps and jerks.This is the case in the example: the end
point of Cam1 and the start point of Cam2 have identical velocity and acceleration values.
Slave position = cam (master position)
Slave position = cam (master position + Offset1) + Offset2