2 gantry systems with tool offset, Gantry systems with tool offset, L-force | plc designer - softmotion – Lenze PLC Designer PLC-Designer (R2-x) SoftMotion User Manual
Page 222
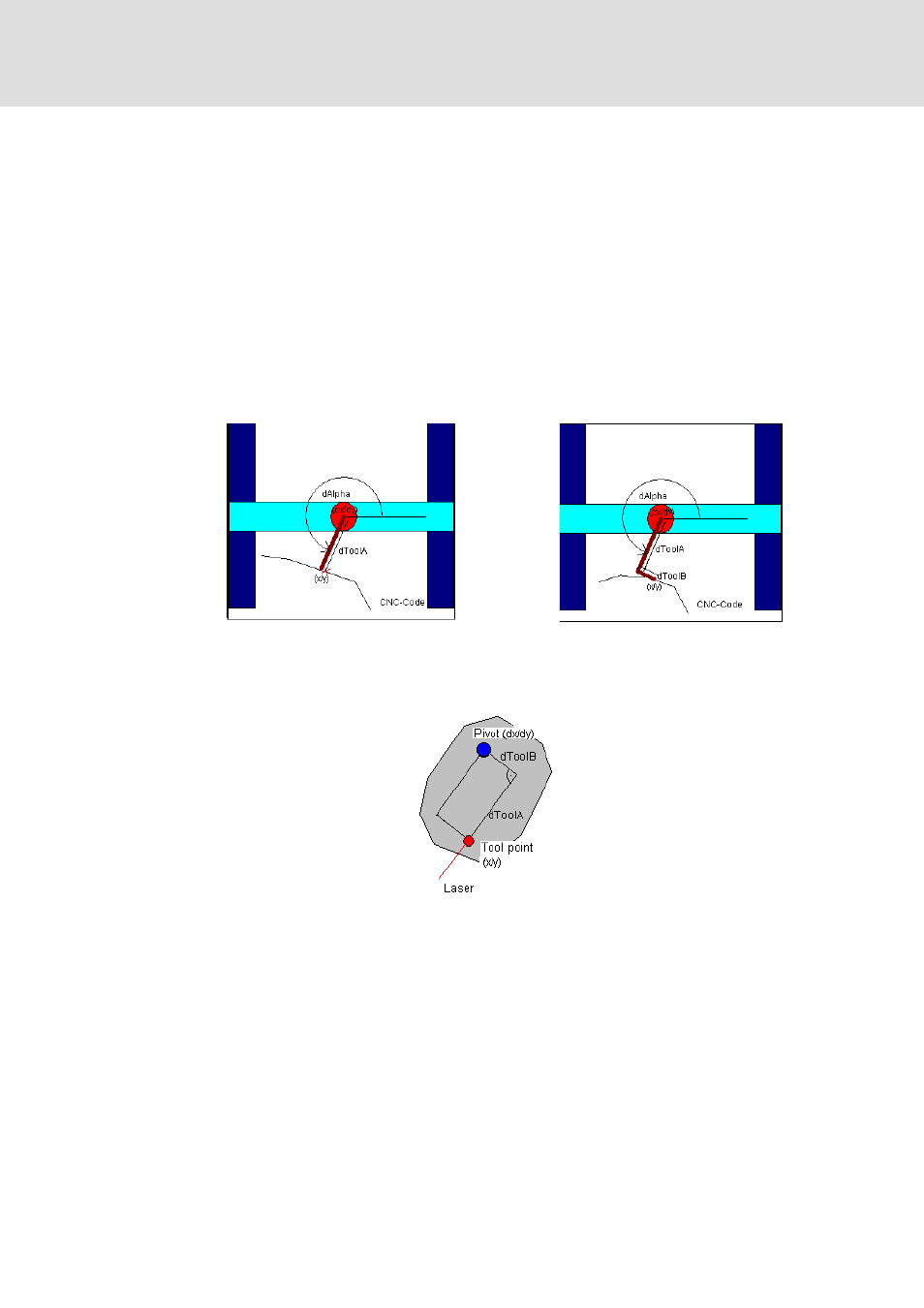
L-force | PLC Designer - SoftMotion
The SM_Trafo.lib library
Transformation function blocks
222
L
DMS 5.2 EN 03/2011 TD17
9.1.2
Gantry systems with tool offset
There are machine gantries whose xyz position does not match the tool's point of action,
as this is not positioned axially on the z axis, but is offset. If the z axis cannot be rotated,
this will be a constant xy offset, which can be fed as such into the standard gantry
transformation.
However, if a rotary axis that rotates around z is involved, this will not be a constant offset;
in this case, the offset will depend on the position of the C axis.
You must determine whether the tool is to be approached as a line (if the vector between
the tool's point of action and axis and the desired tool orientation match ->
SMC_TRAFO_Gantry2Tool1) or as a parallelogram or a right-angled triangle
(SMC_TRAFO_Gantry2Tool2):
In this example the tool cannot be approached as a line, but must be approached as a right-
angled triangle:
In principle, the path can be appropriately modulated by means of SMC_ToolCorr instead
of via a one-dimensional transformation with tool offset (tool can be approached as a line).
The difference between the two methods is the velocity of the tool point. If SMC_ToolCorr
is used, the velocity of the rotation point is controlled according to the specifications made
in the CNC program (F, E) and the velocity of the tool point may vary. However, if this
transformation is used, the velocity of the tool point is determined by the CNC program.
The following function can be used to calculate the tool orientation (dAlpha):