L-force | plc designer - softmotion – Lenze PLC Designer PLC-Designer (R2-x) SoftMotion User Manual
Page 15
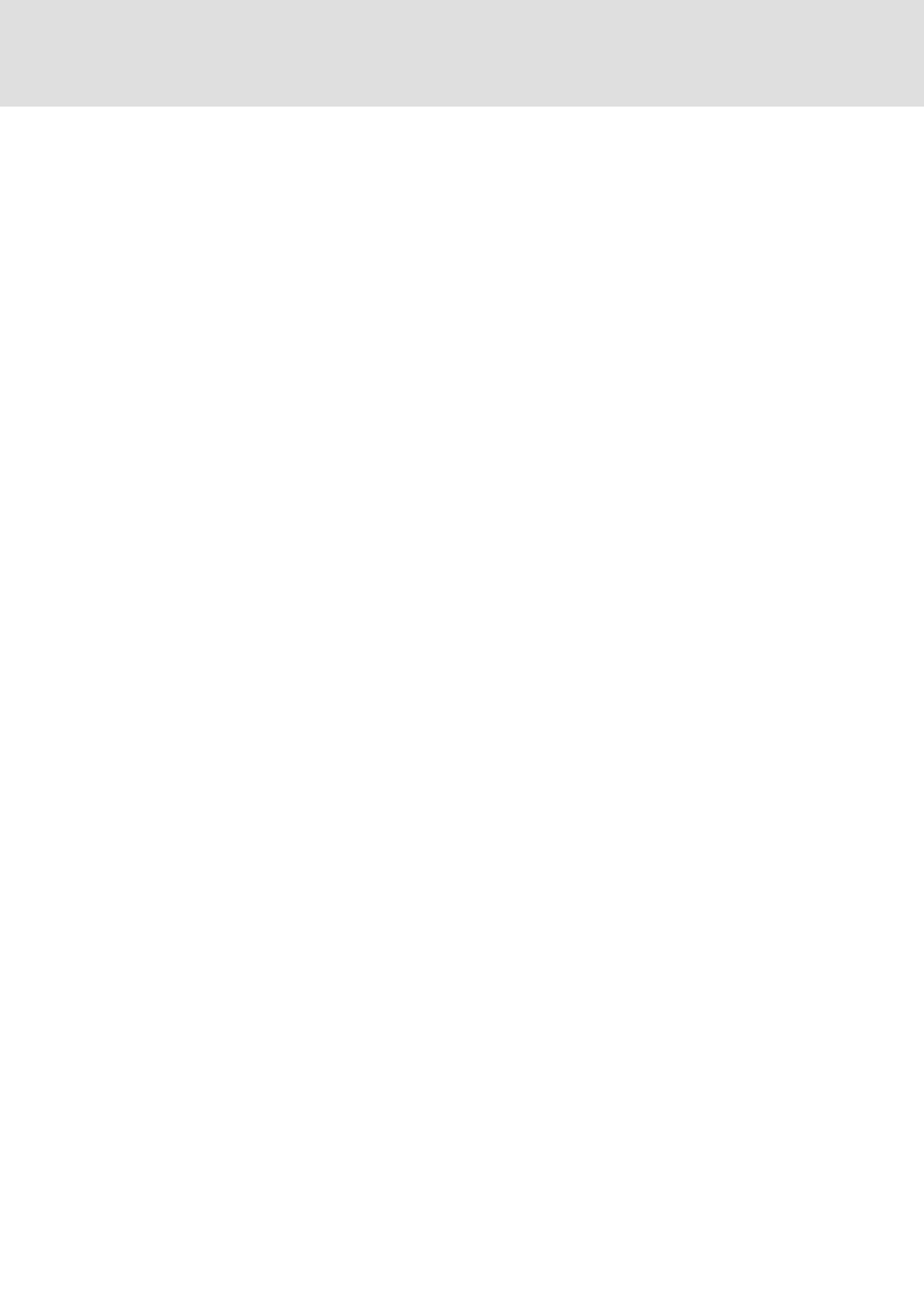
DMS 5.2 EN 03/2011 TD17
L
15
L-force | PLC Designer - SoftMotion
SoftMotion concept and overview of the components
SoftMotion is divided into the following components:
Drive Interface
This SoftMotion component is responsible for communication between the PLC program
and the drives. It consists of the SM_DriveBasic.lib library as well as drive and bus system-
specific libraries and drivers.
The "LenzeCAN (CAN)" drive driver and the LenzeCANdrive.lib library support the motion
control of the Lenze 9400 Servo Drives StateLine and the ECSxM axis modules (Motion) via
the CANopen bus system.
The programmer uses the configuration editor in the »PLC Designer« to map the structure
and parameterisation of the drive hardware. With the help of the Drive Interface libraries,
the "PLC Designer" then uses this information to create IEC data structures that represent
the drives in an abstract manner. The Drive Interface communicates with the drives
automatically, i.e. without the IEC programmer having to do anything else, thus ensuring
that the drive data structures are updated continuously and that any data modified within
them is transferred. To control the drive hardware, the IEC program can either access these
data structures via standard POUs in the SoftMotion libraries (SM_CNC.lib,
SM_PLCOpen.lib) or by means of programs actually created by the IEC programmer.
The setpoints are always set cyclically, i.e. setpoints (positions, velocities, accelerations,
etc.) are calculated and transferred from the Drive Interface to the drives with each IEC task
cycle. It is not possible to "instruct" the drives, for example, to set a target position so that
a drive moves independently and, once the position has been reached, sends a message to
the control that the instruction has been completed successfully. Amongst other reasons,
this is because in such a case it would not be possible to coordinate the motions of several
axes and the central control would not have any influence on the drives during execution
of an instruction.
CNC editor
The CNC editor in the »PLC Designer« is used for the graphical and textual programming of
multidimensional drive motions, based on the DIN 66205 CNC language. Basically,
motions of up to 9 dimensions can be realised, whereby only two dimensions will not be
interpolated linearly. In other words, lines, circles, circular arcs, parabolas, ellipses and
splines can be programmed in two dimensions; the other directions will merely be
interpolated linearly. For each path generated, the "PLC Designer" will automatically create
a global data structure (CNC data) that will be available in the IEC program.
CAM editor
The graphically operated CAM editor integrated in the »PLC Designer« is used to program
cams for the purpose of controlling multi-axis drives. On the basis of each programmed
cam, the »PLC Designer« will automatically generate a global data structure (CAM data),
which will be made available in the IEC program.
CNC libraries
The "SM_CNC.lib", "SM_CNCDiagnostic.lib" and "SM_Trafo.lib" libraries provide the IEC
programmer with program organisation units that can be used to edit, display and execute
motions generated in the CNC editor or planned during runtime.