Festo Электромотор MTR-DCI User Manual
Page 26
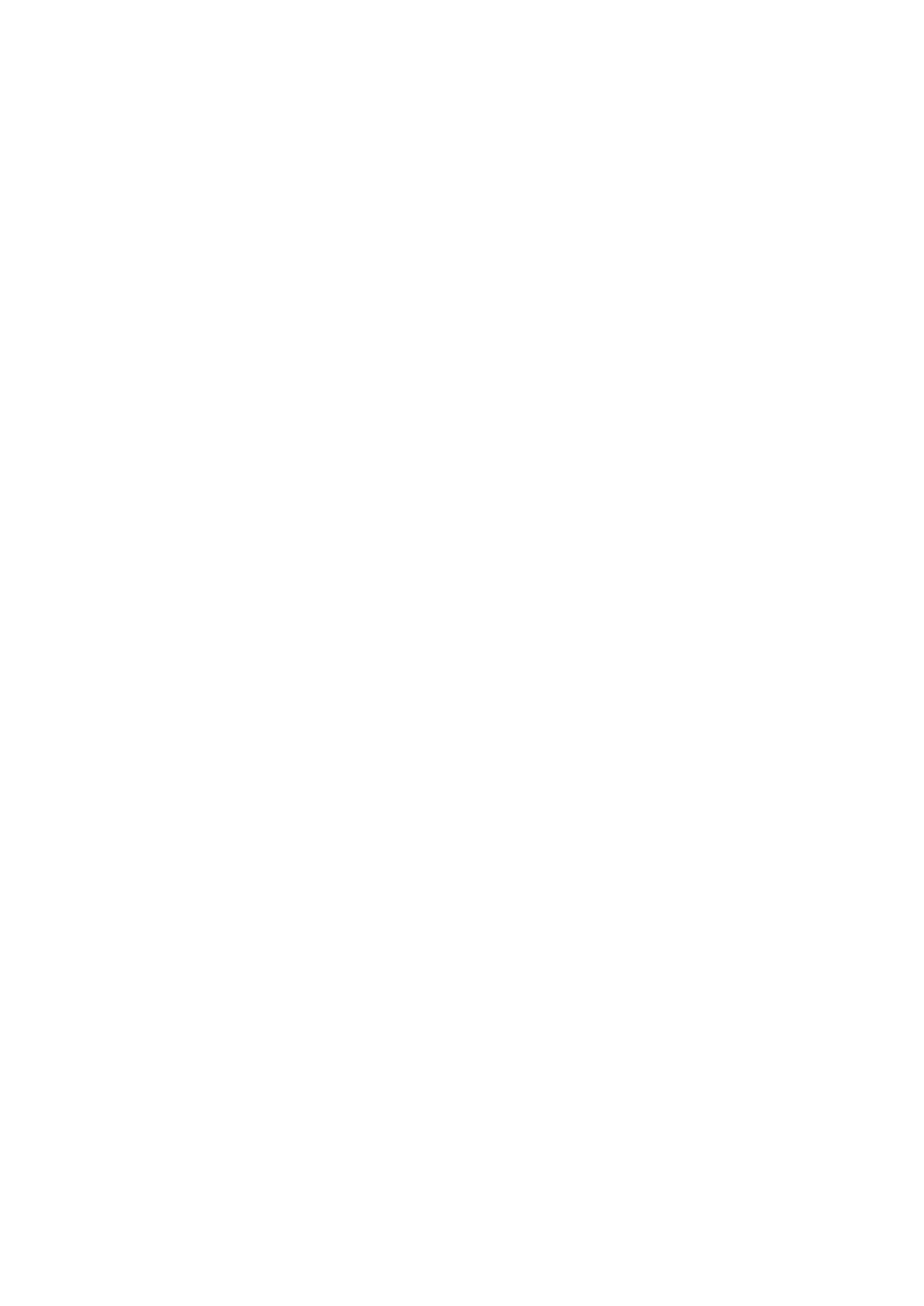
1. System overview
1-6
Festo P.BE-MTR-DCI-PB-EN en 1209a
1.2
Components
To configure an electric drive with the MTR-DCI you will re-
quire the following components:
Motor unit MTR-DCI
Motor with controller, available in 4 sizes, optionally with
control panel (type ...-H2).
By means of different gear reductions, different
requirements can be fulfilled in respect of (gear unit) output
torque and (gear unit) output speed (see appendix A.1).
High torques with low rotational speed are typical for
positioning functions. With the smaller gear reduction, the
travel speed of the axis can be increased with
correspondingly reduced force.
Axis
Linear or rotation axes as per catalogue
Coupling with coupling
housing
For the axial attachment of Festo axes, e.g. type DMES-... or
type DNCE-..., couplings and coupling housings are
available as accessories. The motor unit is connected to the
axis by means of a clamping connector in the coupling
housing. The use of supplementary motor flanges is
therefore unnecessary. Additional information can be found
in the operating instructions for the axis.
Power supply cable
Power supply to the MTR-DCI via a power supply unit.
The power supply for the electronics (logic voltage) can
also take place separated from the load voltage (see
section 3.3).
Programming cable
Parameterisation of the MTR-DCI during commissioning with
the FCT
Fieldbus adapter
For separate power supply to the logic components.
Protection class IP 54. Refer to sections 3.2.3 and A.2.
Fieldbus cable
Operating the MTR-DCI on a higher-order controller
(PLC/IPC).
Reference switch
Sensor as per appendix A.2.
Accessories
For positioning systems, Festo offers adapted matching
accessories (see Festo product range or catalogue).