Product-specific terms and abbreviations – Festo Электромотор MTR-DCI User Manual
Page 16
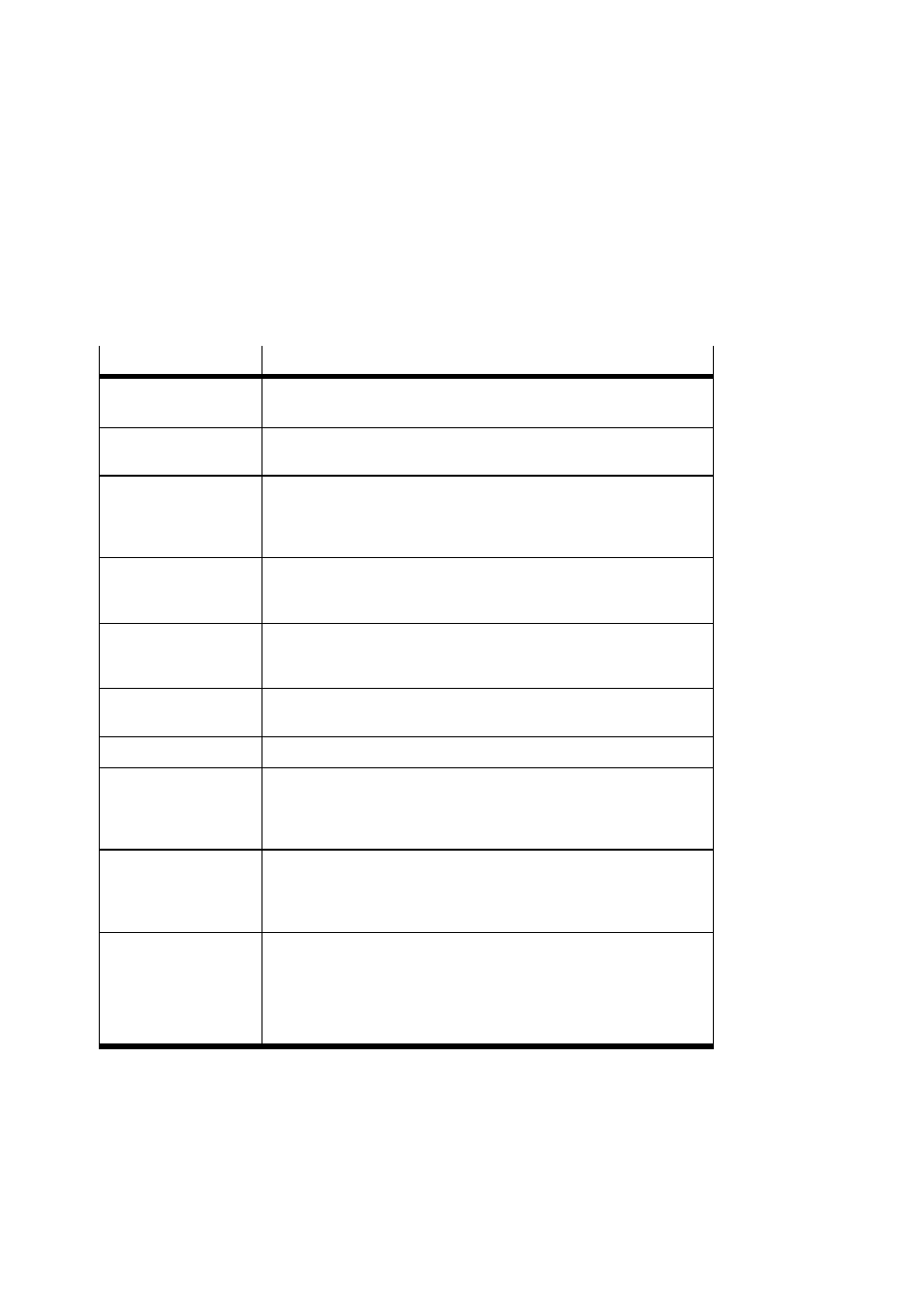
Contents and general safety instructions
XIV
Festo P.BE-MTR-DCI-PB-EN en 1209a
Product-specific terms and abbreviations
The following product-specific terms and abbreviations are
used in this manual:
Term/abbreviation
Meaning
0-signal
Means that there is a 0 V signal present at the input or output (positive
logic, corresponds to LOW)
1-signal
Means that there is a 24 V signal present at the input or output (positive
logic, corresponds to HIGH)
Axis
Mechanical component of a drive which converts the motor revolutions
into positioning movements of a work load. An axis (e.g. positioning servo
axis DMES-...) enables the work load to be mounted and guided and the
reference switch to be mounted.
Axis zero point (AZ)
The axis zero point AZ is defined in relation to the homing point REF (the
“reference” point). The software end positions and the project zero point
PZ are defined in relation to the AZ.
Controller
Electronics which evaluate the sensor signals, calculate movements and
forces and provide the power supply for the motor via the power
electronics.
Drive
Complete actuator, consisting of controller, motor, measuring system
and, if applicable, gear and axis.
EMC
Electromagnetic compatibility
Encoder
Optical pulse generator (rotor position transducer on the motor shaft of
the MTR-DCI). The electric signals generated are sent to the controller,
which then calculates the position and speed on the basis of the signals
received.
Festo Configuration Tool
(FCT)
Commissioning software with uniform project and data management for
all supported device types. The special requirements of a device type are
supported with the necessary descriptions and dialogues by means of
plugins.
Force mode
Control of forces by means of current regulation. The motor torque is
controlled indirectly via the regulation of the current. All specification for
forces/torques are defined in relation to the nominal motor torque (rela-
tive to the nominal motor current). The actual force on the axis should be
determined/checked during commissioning using external measuring
devices and adjusted.