NORD Drivesystems BU0300 User Manual
Page 86
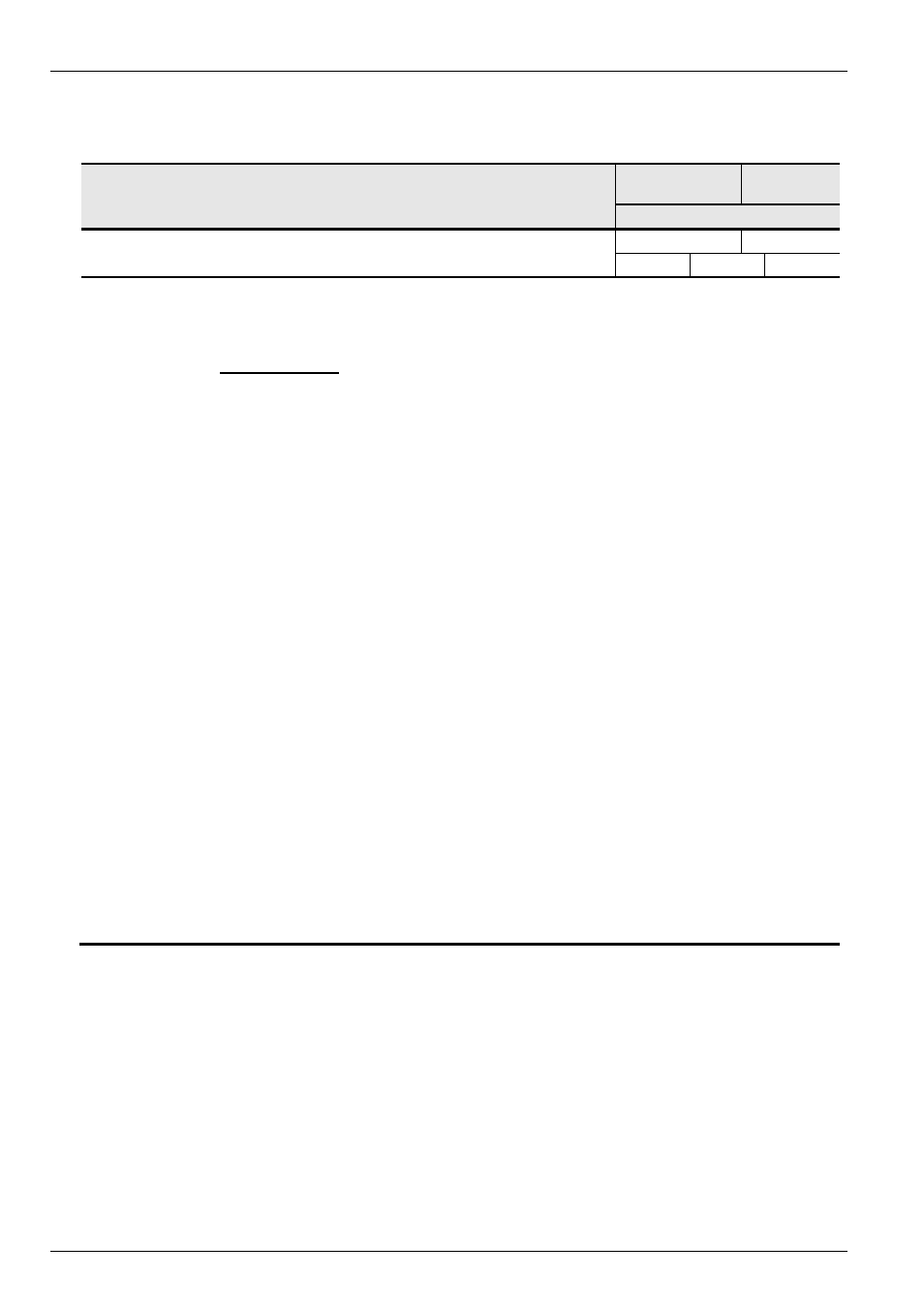
NORDAC trio SK 300E Manual
86
Subject to technical alterations
BU 0300 EN
7.8
Control terminals
Parameter
Setting value / Description / Note
Supervisor
Parameter
set
Available with option
P400
Analog input function 1
BSC
STD
0 ... 16
[ 1 ]
The FI analog input can be used for various functions. It must be noted that only one of the
functions given below is possible at any time.
If, for example, an actual PID frequency is selected, the frequency setpoint cannot be an analog
signal. The setpoint can, e.g., be specified via a fixed frequency.
Analog functions:
0 = Off,
the analog input has no function.
1 = Set frequency,
the given analog range (P402/P403) varies the output frequency between
the set minimum and maximum frequencies (P104/P105).
2 = Torque current limit
, based on the set torque current limit (P112), this can be changed
via the analog input. 100% setpoint here corresponds to the set torque current limit.
3 = Actual frequency PID
, required to generate a control circuit. The analog input (actual
value) is compared with the setpoint (e.g. fixed frequency). The output frequency is
adjusted as far as possible until the actual value equals the setpoint. (see controller
settings P413 – P415)
4 = Frequency addition
, applies in connection with an additional frequency specification
about auxiliary setpoints (P410/411). In these cases, the setpoints are added.
5 = Frequency subtraction
, the frequency value provided is subtracted from the setpoint.
6 =
Reserved
7 =
Reserved
8 = Actual frequency PID limited
, like function 3 "Actual frequency PID", however the output
frequency cannot fall below the programmed minimum frequency value in Parameter
P104. (no rotation direction reversal)
9 = Actual frequency PID monitored
, like Function 3 "Actual frequency PID", however the
FI switches the output frequency off when the minimum frequency P104 is reached.
10 =
up to 13 = reserved
14 = Actual value process controller *,
activates the process controller, analog input 1 is
connected to the actual value sensor (compensator, air can, flow volume meter, etc.). The
mode (0-10 V or 0/4-20 mA) is set in P401.
15 = Setpoint process controller *,
as function 14, however the setpoint is specified (e.g. by
a potentiometer). The actual value must be specified using another input.
16 = Lead process controller *,
adds an adjustable additional setpoint after the process
controller.
*) further details regarding the process controller can be found in Chap. 12.3