NORD Drivesystems BU0300 User Manual
Page 110
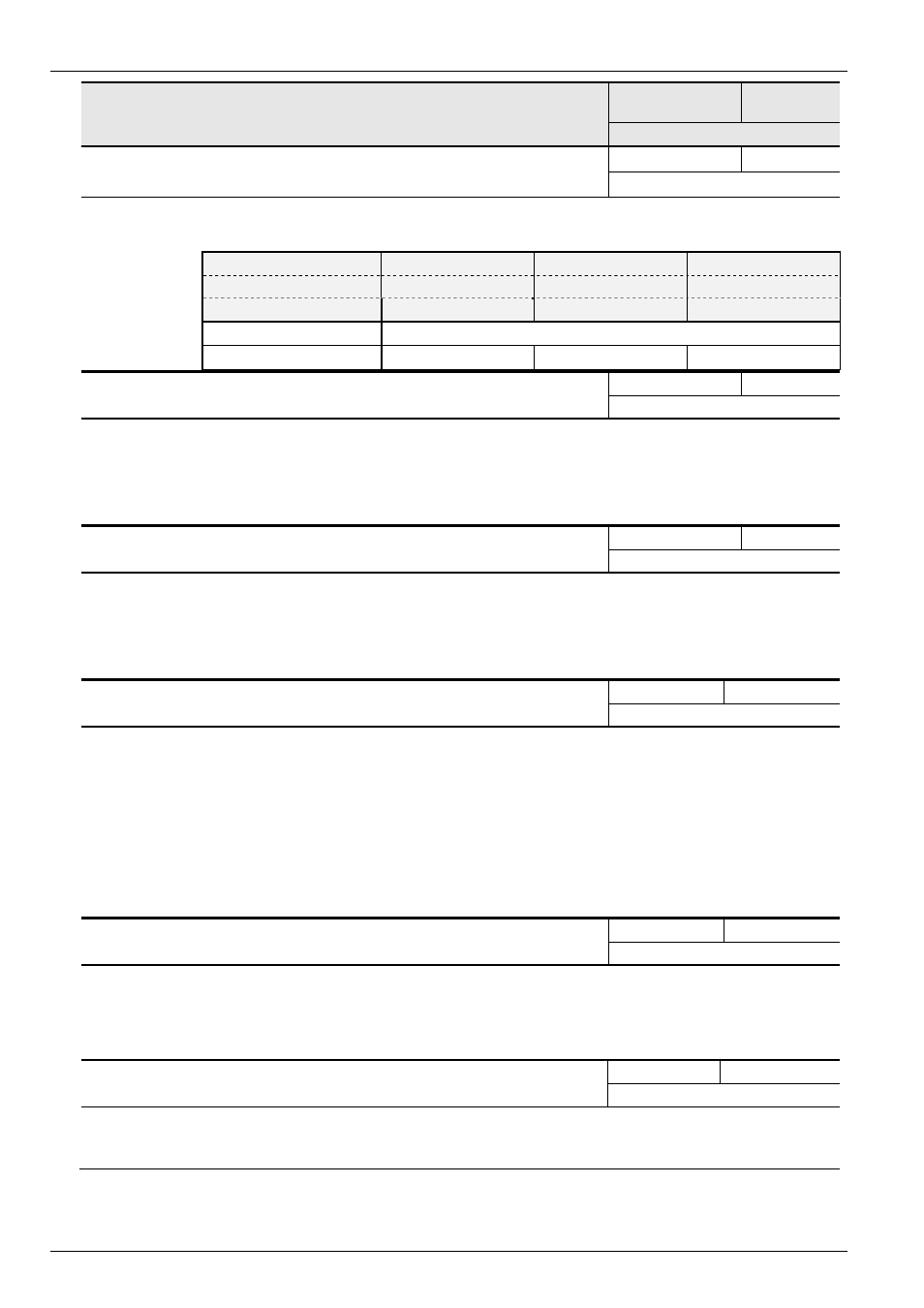
NORDAC trio SK 300E Manual
110
Subject to technical alterations
BU 0300 EN
Parameter
Setting value / Description / Note
Supervisor
Parameter
set
Available with option
P551 Drive
profile
S
Always available
0 ... 1
[ 0 ]
According to the option the relevant process data profiles can be activated with this parameter.
This parameter is only effective for pluggable technology units (SK TU2-…).
System
CANopen*
DeviceNet
InterBus
Technology unit
SK TU2-CAO
SK TU2-DEV
SK TU2-IBS
Setting
0 =
USS protocol (Profile "Nord")
1 =
DS402 profile
AC Drives profile
Drivecom profile
P552
Function PotentiometerBox right
S
Always available
0 ... 2
[ 1 ]
In this parameter the function can be set, in combination with the option PotentiometerBox (SK
TU2-POT), for the switch in the Right-hand position (R).
0 =
No function
1 =
Enabled right
2 =
Enabled left
P553
Function PotentiometerBox left
S
Always available
0 ... 2
[ 2 ]
In this parameter the function can be set, in combination with the option PotentiometerBox (SK
TU2-POT), for the switch in the Left-hand position (L).
0 =
No function
1 =
Enabled right
2 =
Enabled left
P558 Magnetisation
time
S P
Always available
0/1/2...500 ms
[ 1 ]
The ISD control can only function correctly if there is a magnetic field in the motor. For this reason, a
DC current is applied before starting the motor. The duration depends on the size of the motor and is
automatically set in the factory setting of the FI.
For time critical applications, the excitation time can be set or deactivated.
0 =
No magnetisation time
1 =
Automatically determined magnetisation time
2 ... 500 = According to magnetisation time set
NOTE:
Setting values that are too low can reduce the dynamics and starting torque.
P559
DC run-on time
S P
Always available
0.00 ... 5.00 s
[ 0.50 ]
Following a stop signal and the deceleration ramp, a direct current is briefly applied to the motor to
fully bring the drive to a stop. Depending on the inertia, the time for which the current is applied can
be set in this parameter.
The current level depends on the previous braking procedure (current vector control) or the static
boost (linear characteristic).
P560
Safe on EEPROM
S
P
0…1
[1]
Setting 0 prevents cyclical writing to the EEPROM.
This is particularly important where, e.g. constant overwriting of parameters via bus connection would
greatly overload the memory.