NORD Drivesystems BU0300 User Manual
Page 109
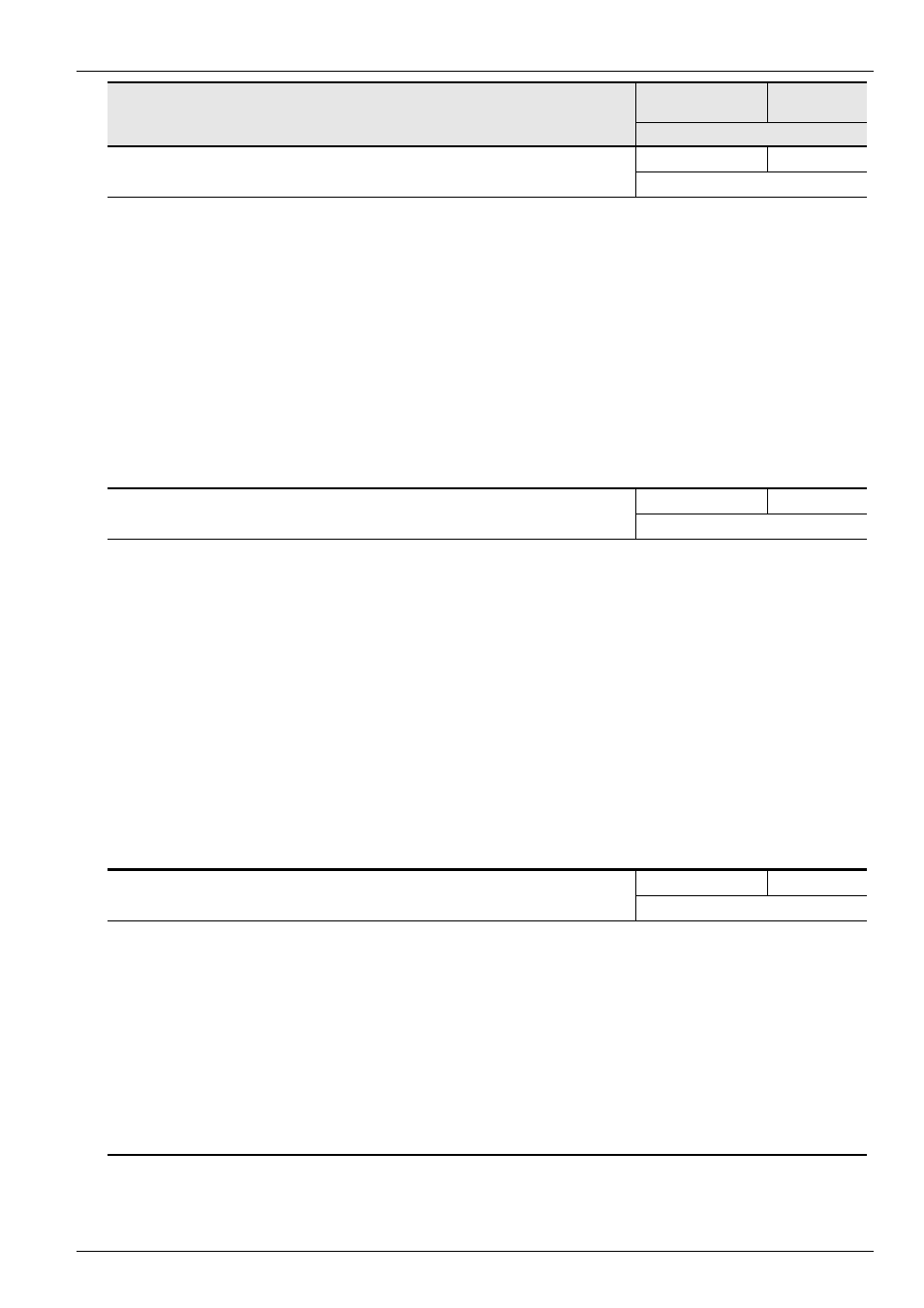
7.9 Additional parameters
BU 0300 EN
Subject to technical alterations
109
Parameter
Setting value / Description / Note
Supervisor
Parameter
set
Available with option
P547
Function Bus setpoint 2
S P
Always available
0 ... 20
[ 0 ]
In this parameter, a function is allocated to the output setpoint 2 during bus actuation.
NOTE:
Further details can be found in the respective BUS instruction manuals.
0 =
Off
1 =
Setpoint frequency
2 =
Torque current limit
3 =
Actual frequency PID
4 =
Frequency addition
5 =
Frequency subtraction
6 =
Reserved
7 =
Reserved
8 =
Actual PID frequency limited
9 =
Actual PID frequency monitored
10-13 =
Reserved
14 =
Process controller actual value
15 =
Process controller setpoint
16 =
Process controller lead
17 =
Bus IO In Bits 0-7
18 =
Reserved
19 =
Set relays
20 =
Set analog output
P548
Function Bus setpoint 3
S P
Always available
0 ... 20
[ 0 ]
In this parameter, a function is allocated to the output setpoint 3 during bus actuation. It is only
present when P546
≠ 3.
NOTE:
Further details can be found in the respective BUS instruction manuals.
0 =
Off
1 =
Setpoint frequency
2 =
Torque current limit
3 =
Actual frequency PID
4 =
Frequency addition
5 =
Frequency subtraction
6 =
Reserved
7 =
Reserved
8 =
Actual PID frequency limited
9 =
Actual PID frequency monitored
10-13 =
Reserved
14 =
Process controller actual value
15 =
Process controller setpoint
16 =
Process controller lead
17 =
Bus IO In Bits 0-7
18 =
Reserved
19 =
Set relays
20 =
Set analog output
P549
Function PotiBox (Option)
S
Always available
0 ... 16
[ 1 ]
In this parameter, the setpoint of the PotentiometerBox (SK TU2-POT) is assigned a function. (An
explanation can be found in the description of P400) The FI is only enabled with the
PotentiometerBox when this parameter is set to the setpoint frequency (P400=1).
0 =
Off
1 =
Setpoint frequency
2 =
Torque current limit
3 =
Actual frequency PID
4 =
Frequency addition
5 =
Frequency subtraction
6 =
Reserved
7 =
Reserved
8 =
Actual PID frequency limited
9 =
Actual PID frequency monitored
10-13 =
Reserved
14 =
Process controller actual value
15 =
Process controller setpoint
16 =
Process controller lead