Additional parameters, P503 leading function output, P504 pulse frequency – NORD Drivesystems BU0300 User Manual
Page 102: P505 absolute minimum frequency
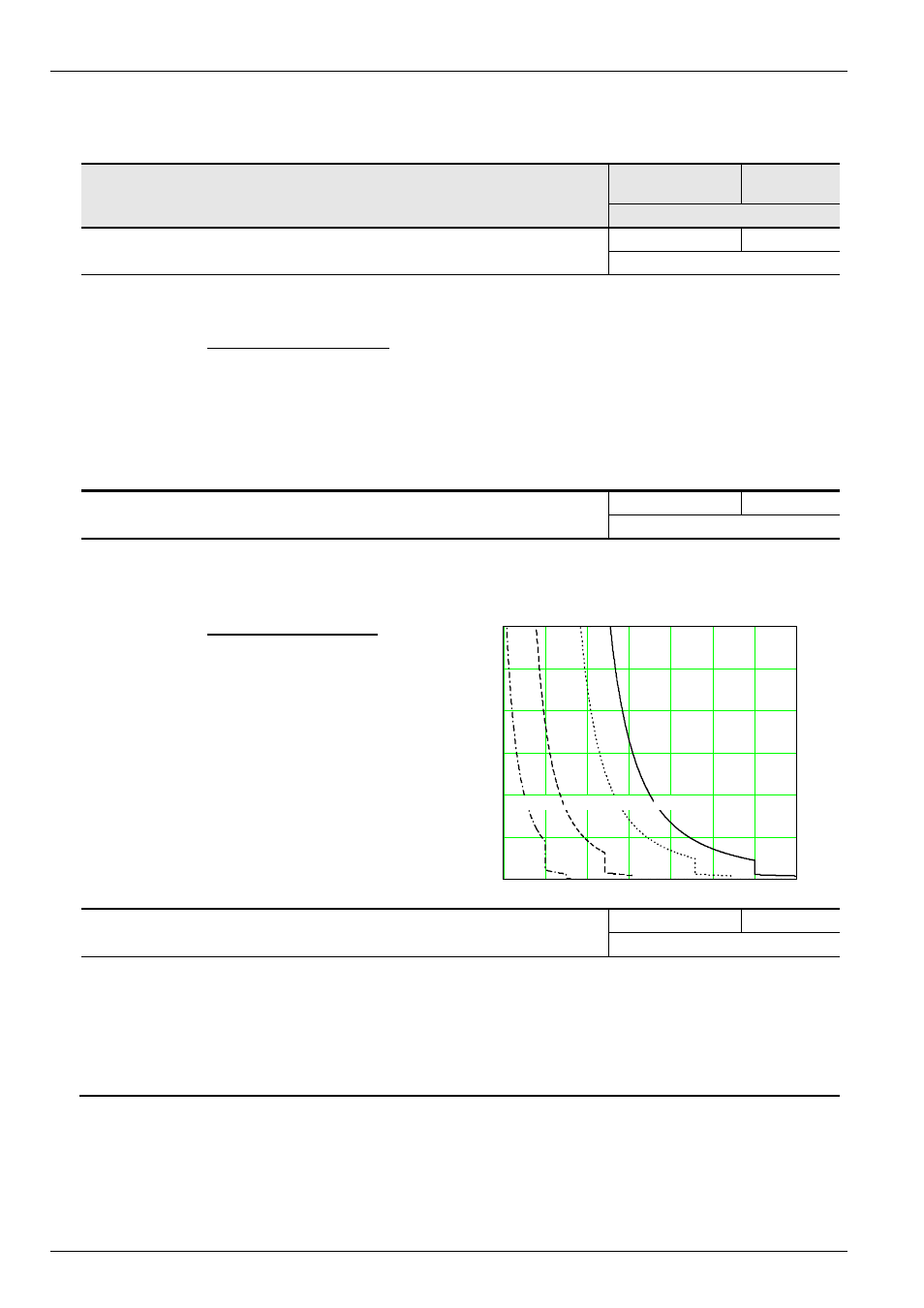
NORDAC trio SK 300E Manual
102
Subject to technical alterations
BU 0300 EN
7.9
Additional parameters
Parameter
Setting value / Description / Note
Supervisor
Parameter
set
Available with option
P503
Leading function output
S
Always available
0 ... 4
[ 0 ]
To use the master function output, the inverter controller source must be selected in P509. Only the
master frequency (setpoint 1) is transferred with Mode 1, while the actual values selected in P543,
P544 and P545 are transferred in Mode 2.
When using the USS mode:
If the SK 300E is operated with a connected ParameterBox, the external USS channel for bus control
is blocked. The external USS communication is automatically initiated when the ParameterBox
connection is interrupted. If the FI has to be re-parameterised, the bus communication will be
interrupted when the ParameterBox is connected.
0 = Off
1 = USS mode 1
2 = CAN mode 1
3 = USS mode 2
4 = CAN mode 2
P504 Pulse
frequency
S
Always available
3.0 ... 10.0 kHz
[ 6.0 ]
The internal pulse frequency for actuating the power component can be changed with this parameter.
A higher setting reduces motor noise, but leads to increased EMC emissions and reduction of the
possible motor nominal torque.
I
2
t- characteristic curve FI
, raising
the pulse frequency leads to a
reduction of the output current
dependent on time.
Note
Æ
The noise suppression grade
limit curve B (for FI attached to motor)
is reached with the setting 6kHz
t sec
(
)
0.8
1
1.2
1.4
1.6
1.8
2
2.2
0
30
60
90
120
150
180
20 kHz 16 kHz
10 kHz <=6kHz
x Inenn
.
P505
Absolute minimum frequency
S P
Always available
0.1 ... 10.0 Hz
[ 2.0 ]
Gives the frequency value that cannot be undershot by the FI. If the setpoint becomes smaller than
the absolute minimum frequency, the FI switches off or changes to 0.0Hz.
At the absolute minimum frequency, braking control (P434 or P441) and the setpoint delay (P107)
are actuated. If a setting value of "Zero" is selected, the brake relay does not switch during reversing.
When controlling lift equipment, this value should be set at a minimum of 2Hz. From 2Hz, the current
control of the FI operates and a connected motor can supply sufficient torque.
NOTE:
Output frequencies < 2Hz lead to current limitation.