Section 26 modbus response time, Section 27 modbus interpacket delay, Gateway communications manual – AERCO XPC GATEWAY Communications User Manual
Page 122
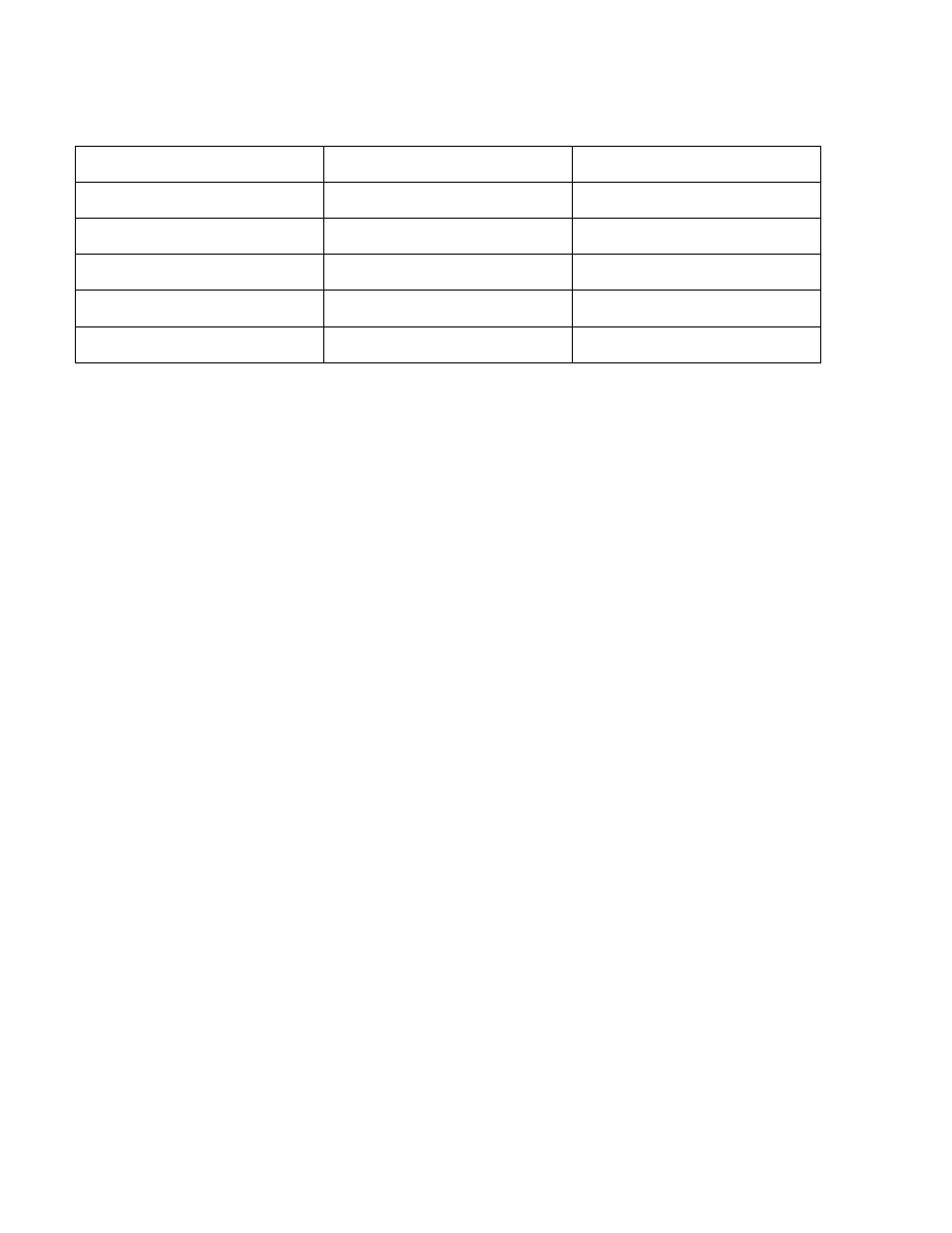
GATEWAY COMMUNICATIONS MANUAL
122
Table 7 AERCO XPC Gateway Timer Default Values
Program File
Modbus Response Time
Modbus Interpacket Delay
Aerco_1x
2000 mSec
20 mSec
Aerco_2x
2000 mSec
50 mSec
Aerco_3x
200 mSec
20 mSec
Aerco_4x
2000 mSec
20 mSec
Aerco_5x
2000 mSec
50 mSec
These timer settings are based on the assumption that all of the points are being requested from AERCO
equipment and data is being transmitted with a baud rate of 9600 bps.
SECTION 26 MODBUS RESPONSE TIME
Now let us take a more detailed look at the Modbus Response Time parameter. A Modbus Response
Time of 2000 mSec is required when information is being requested from the boilers through the
BMS/BMS II (assume Modbus Pass Thru is enabled). Since the BMS/BMS II acts both as a boiler
controller as well as a communications Gateway, it requires up to this amount of time to process a
request from the XPC or a BAS for information from its boilers.
If information is only needed from the BAS/BAS II and not the boilers (Modbus Pass thru is now disabled)
then the Modbus Response Time setting can be reduced to 200 mSec for faster updates. If
communication from the XPC is going directly to the boilers or heaters and no BMS/BMS II is in the
system, the Modbus Response Time setting can also be reduced to 200 mSec or possibly even as low as
100 mSec.
If control between the BMS and boilers is done via the pulse-width wired connection and only monitoring
via the Modbus is being done directly to the BMS and/or boilers, the Modbus Response Time can also be
reduced to 200 mSec for faster updates.
SECTION 27 MODBUS INTERPACKET Delay
Normally, the “XPC” should not need to be adjusted. Nevertheless, there are a few cases where
adjustments may be needed. For example, whenever the BMS/BMS II is controlling a lot of boilers
(generally more than 8) while at the same time passing off information from the boilers to a BAS. In this
case, it may be necessary to increase the Modbus Interpacket Delay setting. This would slow down the
frequency of the requests from the XPC to the boilers through the BMS/BMS II. The effect is to give the
BMS more time to perform its task of controlling the boilers. Increasing the Modbus Interpacket Delay
setting may also help if noise in the boiler room is adversely affecting the BMS/BMS II control of the
boilers over the Modbus Network by causing dropouts (“Modbus Communications faults”). When the XPC