Commissioning – Lenze 8200 Frequency inverters User Manual
Page 129
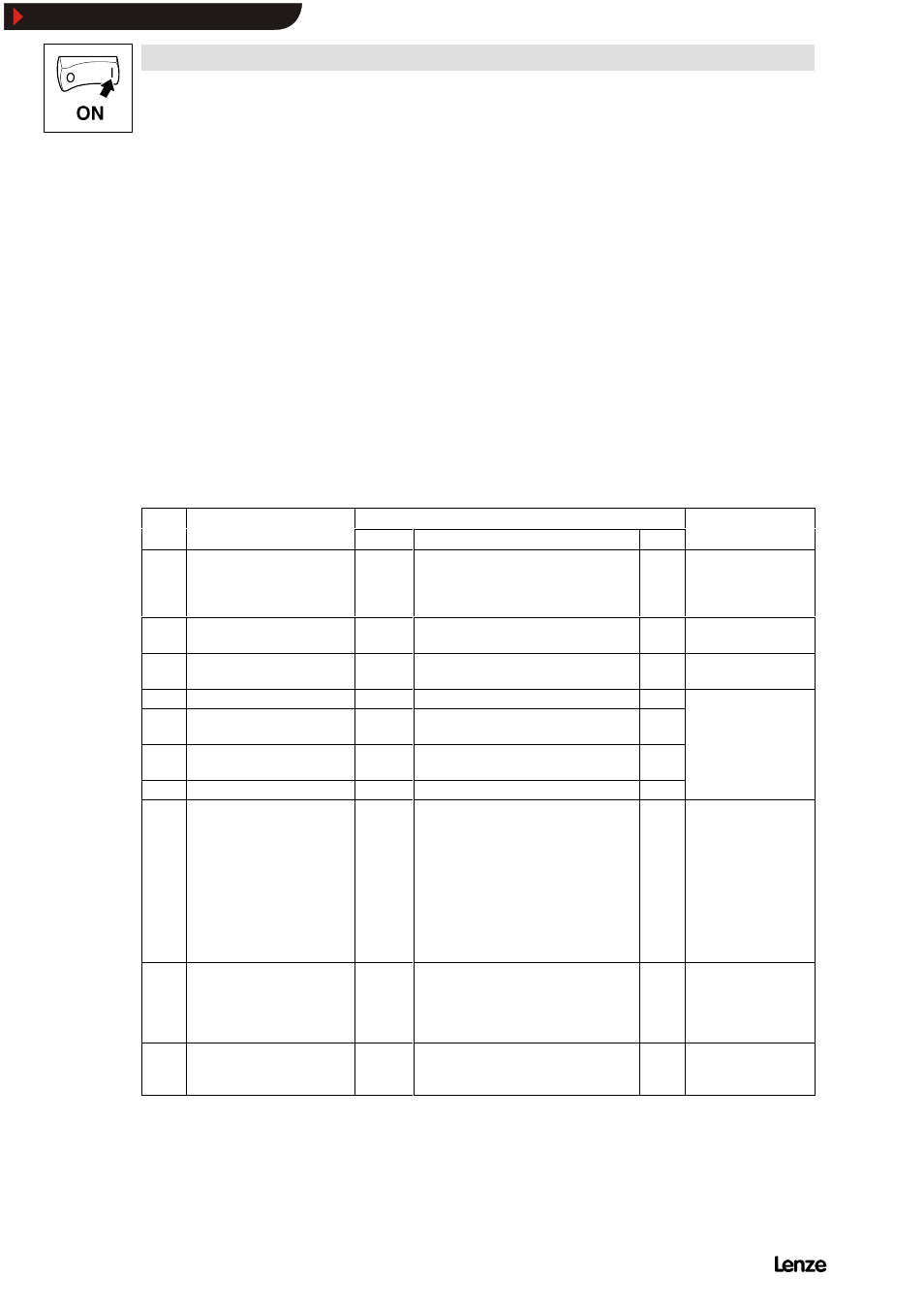
Commissioning
8200SHB0199
5-24
Application FIG 5-4:
The material speed v
2
is to be synchronised to the line speed v
1
by means of a
dancer-position control. The dancer-position setpoint is internally set.
Functions used
-
Internal PID controller as position controller.
-
Selection of the line speed v
1
via terminal 8.
-
Actual dancer-position value from the dancer potentiometer via the analog
plug-in module 8279IB.
-
Set-up speed via terminal Klemme E3 (JOG1).
-
Switch-off of the influence of the dancer controller via terminal E4 (externally)
or internally via Q
min
(C017) and C008 = 7.
Code settings:
Code
Name
Possible settings
IMPORTANT
Code
Name
Lenze
Choice
Info
IMPORTANT
C005 Configuration
-0-
-6-
Controlled operation; setpoint via
terminal 8 with digital frequency
feedback via terminal E1
Jumper setting for
terminal 8 must be
adapted to 5 V (see
chapter 4.2.8.2).
C007 Terminal configuration
-0-
-49-
Actual dancer position
via terminal E1
C037 JOG value 1
20.00
Fixed set-up speed v
1
for material
guidance, individually adjustable
C070 Gain PID controller
1.00
C071 Integral action time PID
controller
100
Adaptation to process
C072 Differential component PID
controller
0.0
Adaptation to process
C074 Influence PID controller
0.0
10.0 %
C105 Deceleration time QSP
5.00
Enter approx. 1 s
E.g. emergency-off
function:
-
The drive geometry
must be adjusted so
that it is possible to
brake the controller to
standstill within a very
short time. A brake
chopper might be
required.
C181 Setpoint PID controller
0.0
Set the dancer to the position required,
C051 = read the actual dancer value and
store it under C181.
C181 must not be 0,
because here the
position setpoint is
generated by the main
setpoint.
C239 Frequency setting range
-0-
-1-
Unipolar
Direction of rotation
cannot be changed via
the process controller.
-
All other parameters are based on the factory setting.
-
Adapt the jumper setting to the main setpoint signal (see chapter 5.5.1).
-
Set the rated motor data under C088 (rated motor current) and C091 (motor cos
Ö) depending to the motor
connected.
Show/Hide Bookmarks