2 overview of cmmo-st, 1 general properties, 2 commissioning options – Festo Электроцилиндр User Manual
Page 14: 3 control profiles of the i/o interface
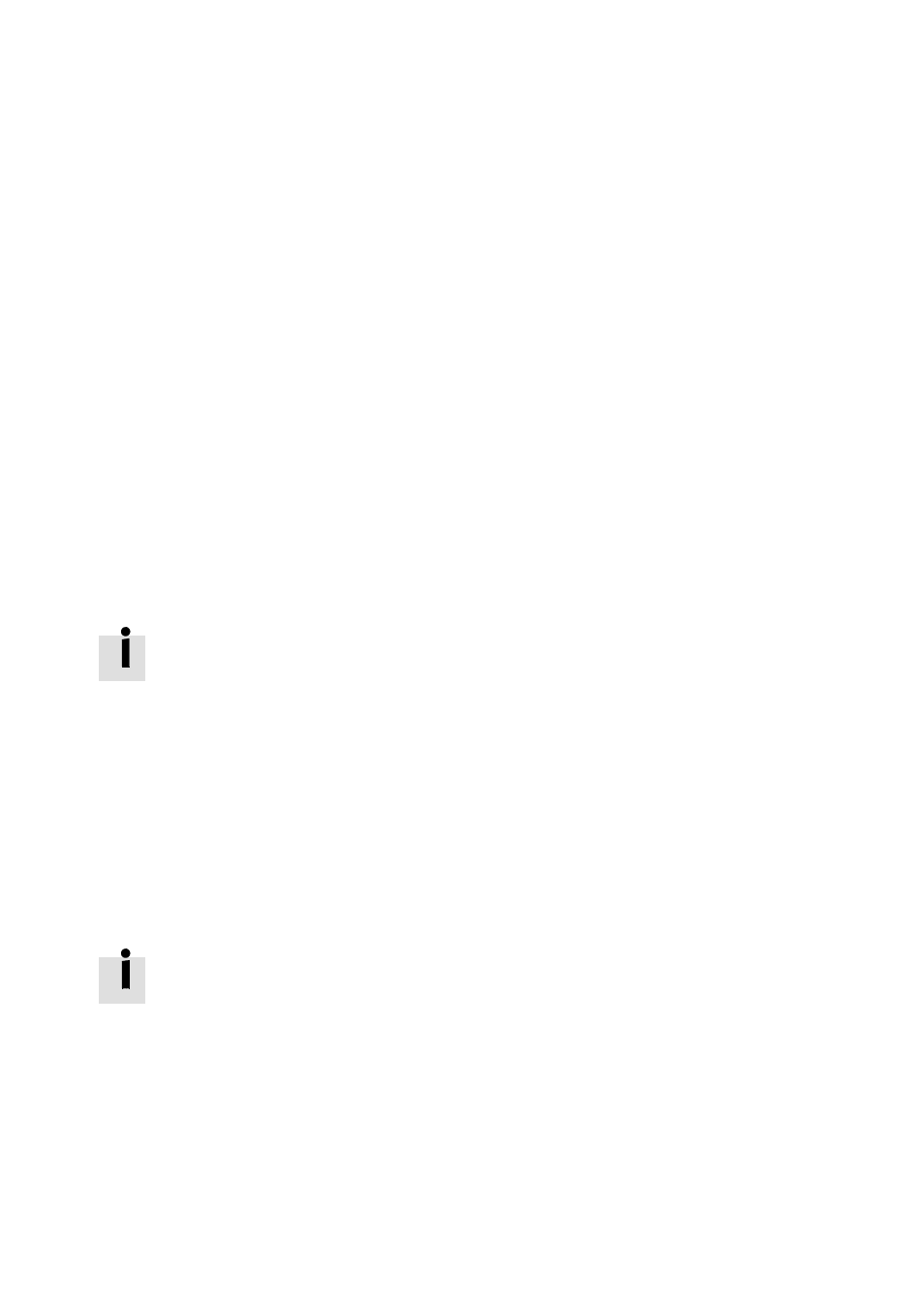
2
Overview
14
Festo – GDCP-CMMO-ST-EA-SY-EN – 1301a – English
2.2
Overview of CMMO-ST
2.2.1
General properties
–
Rotor-oriented control: stepper motor behaves like a servo motor; force control possible, energy-
optimised operation, low heat generation
–
Separate load and logic supply (no new homing run required after emergency stop)
–
Control cabinet unit, field use in IP40 environments is also possible (with full pin assignment)
–
Ethernet interface with integrated web server
–
Backup file: includes all parameterisation settings. It can be stored on separate data storage
media. Enables seamless device replacement.
–
7 segment display to indicate device states, errors and warnings
–
Internal braking resistor present
–
The CMMO is available as an NPN variant (type code CMMO-…-DION) and a PNP variant
(type code CMMO-…-DIOP). This document describes both variants.
–
Function “Safe torque off ” (STO):
description GDCP-CMMO-ST-STO-…
2.2.2
Commissioning options
The CMMO-ST can be parameterised and commissioned as follows:
–
With the integrated web server, using a mechanical drive of the OMS series (optimised motion
series): diagnostics and parameterisation via standard web browser, simple positioning
(
section 5.3)
–
with
FCT, the Festo Configuration Tool: convenient, full function range (
section 5.4)
Control via Ethernet (CVE):
It is possible to start records from a PC programme via the Ethernet interface. However,
in-depth knowledge of programming TCP/IP applications is required for this purpose
(
appendix B.1).
2.2.3
Control profiles of the I/O interface
Valve profile (7)
Simple I/O control: Based on the pneumatic valve pilot,
7 position records can be selected directly
through one input each (7 separate inputs). Upon reaching the target position the output correspond-
ing to the input is set (7 separate outputs). The valve profile exclusively supports simple positioning
operation, optionally with reduced torque.
Binary profile (31)
Flexible I/O control:
31 records (plus record 0 = homing) can be addressed via 5 inputs. The binary
profile also enables jogging and teaching, force mode, speed mode and record linking.
A detailed description of these profiles
section 5.5.