FEC FUSIONE-HS-2 User Manual
Page 17
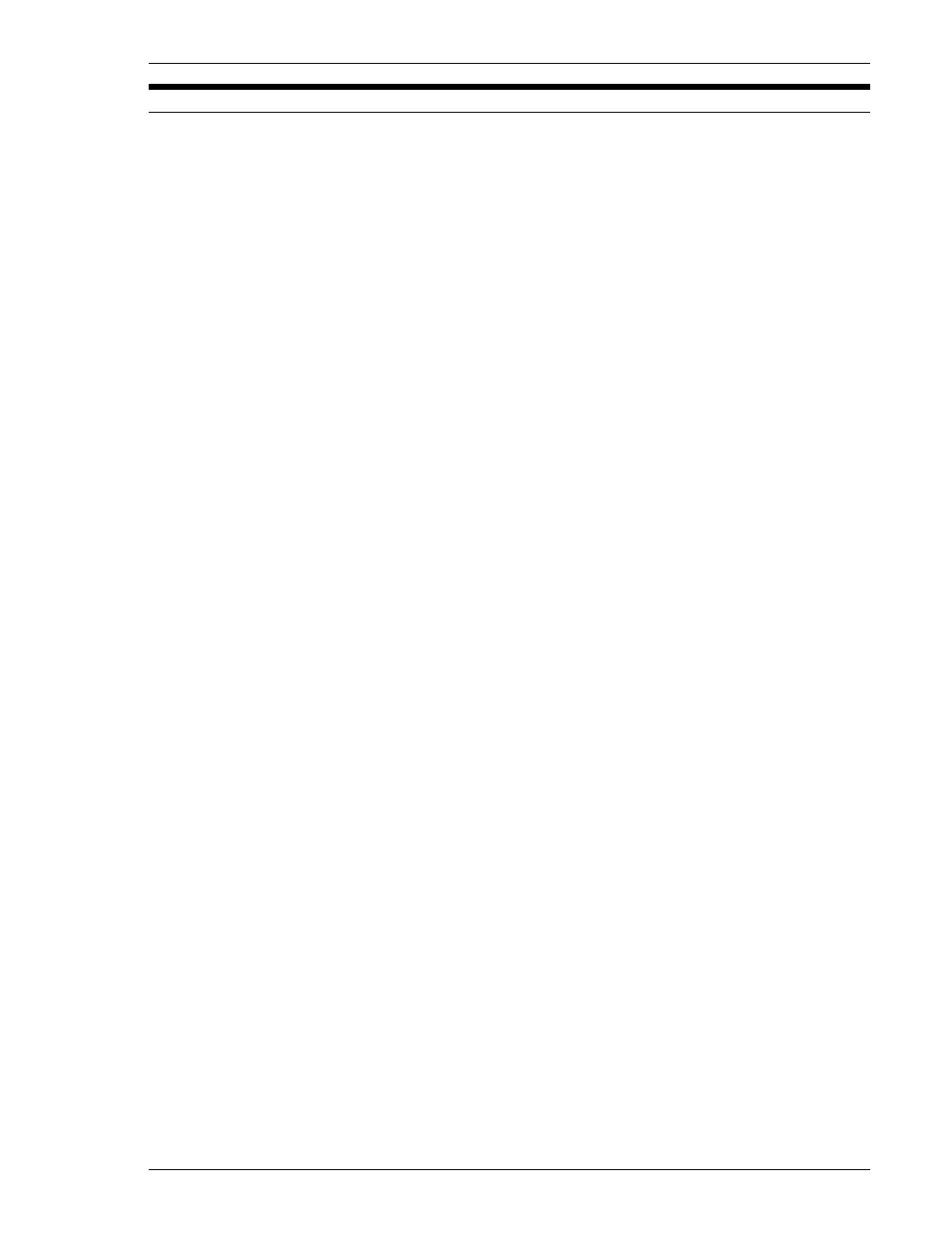
FEC FUSION Operations Manual
Chapter 1: Outline (Rev 2)
Page 1-3
1.2 Features
The FUSION Fastening System is a culmination of over twenty years of electric fastening expertise
integrated with the latest electronic technology. The system is designed with modular construction in
mind. The basic elements of this system are:
1) A brushless DC permanent magnet high speed motor, with resolver feedback
2) A combination Fastening Controller / Servo Amplifier
3) 32-bit RISC (Reduced Instruction Set Computing) CPU for spindle control
4) Fully digital controlled drive amplifier
5) Configurable communications interfaces
•
Compact Design
As the result of miniaturization circuit technology, the controller maintains a maximum
width of 160mm in spite of the built-in power source, controller interface and servo
amplifier. Controllers operate on single-phase 100 ~ 230 VAC (Auto switching) for
simplified connection to standard plant floor receptacles. System components can be
back panel mounted with quick replacement capabilities.
•
Front Keypad-Display.
A front keypad display is an integral component for programming single units and/or
monitoring the fastening results and status conditions in the system. Large
alphanumeric LED displays and status lights provide excellent visibility in plant
operations.
•
Fastening Functions.
Fastening can be performed in either the Torque Control or the Angle Control method.
Angle (rotational) and torque rate monitoring provide additional error proofing functions.
•
Parameter Selection
•
Totally digitized system eliminates analog potentiometers.
•
Up to 16 sets of parameters can be stored into Flash ROM.
•
No battery-backup of memory is required.
•
“No Cost” AFC User Console Programming Software
Nutrunner programming and data collection can be performed via the user-friendly AFC
software provided at no cost with every system. Functions such as Preset Parameter
programming, fastening data monitoring and fastening data analysis can be performed.
The software is primarily utilized on single spindle application in a detachable mode via
a laptop computer with RS232 communications.
•
Communication and I/O Interface
(1) Programming and Display – Front Panel -Input/Output – Manual interface.
(1) RS232 – Front Panel - Input/output – Programming and Data collection
(2) RS232 – Rear Panel – Output – Printer or data collection device.
(1) T/A MON – Front Panel – Output – Analog Torque and Angle analysis.
(1) Discrete I/O Terminal – Rear panel - Control and PLC interface
(1) Optional Ethernet – Output - Data collection
(1) Optional Fieldbus I/O interfaces – Input/Output – Control and PLC interface