FEC FUSIONE-HS-2 User Manual
Page 106
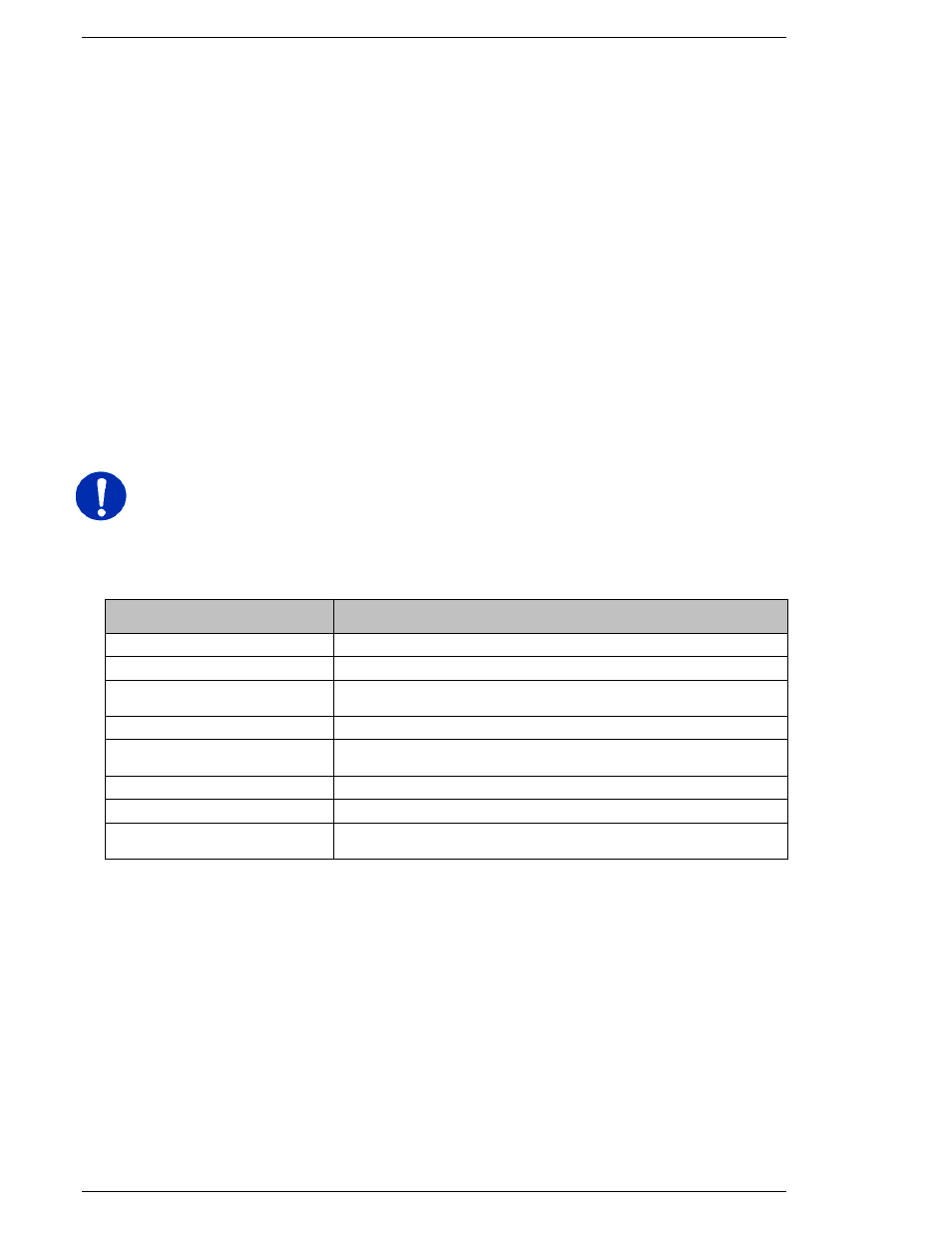
Chapter 6: Fastening Instructions
Three-Step Fastening
Three-step fastening will be used primarily for joints that have a requirement to synchronize
with another spindle during the incremental stages of the rundown to crush/compre
gasket or grommet or for special joint conditioning (valve cover, oil pan, or body assembly, for
example).
1. Angle control commences at SNUG TORQUE. All angle values are referenced from this point.
2. Once SPEED CHANGE TORQUE is reached or FREERUN REVO
switch from FREERUN SPEED to SLOWDOWN SPEED and continue to fasten to 1ST
TORQUE/ANGLE.
3. The system will fasten to the 1ST TORQUE/ANGLE value during the specified 1ST TIME. 1ST
TORQUE/ANGLE must be reached within the 1ST
4. Upon reaching 1ST TORQUE/ANGLE, 1ST TIME ends and FINAL TIME begins. 1ST
TORQUE/ANGLE is the shift point to TORQUE SPEED
mencing the next step.
(See 4.13
5.
The system will fasten to CROSSOVER TORQUE/ANGLE, synchronize with other spindles
and then fasten to STANDARD ANGLE using TORQUE SPEED during FINAL TIME.
STANDARD ANGLE must be reached within the FINAL TIME limits or a reject will occur.
NOTE: When performing multiple step Angle control fastening, the rotation Angle
should be performed as one continuous operation. There should be no intermediate
stop / synchronization points once Snug Torque has been sensed and rotation angle is
being controlled. Under special conditions multiple steps can be performed using i
termediate Torque or Angle stop/synchronization points.
FUNCTION
RECOMMENDATION / COMMENT
SPEED CHANGE TORQUE
30% of S
THRESHOLD TORQUE
Start point of 1
1ST TORQUE/ANGLE
80% of S
Used for RATE/TIME settings and TORQUE SPEED initiation.
SNUG TORQUE
Angle Control Start Point
CROSSOVER
TORQUE/ANGLE
Start point of 3
Synchronization point for 3
STANDARD ANGLE
Engineered product fastening specification
1ST TIME HIGH/LOW LIMIT
Acceptance range to reach 1ST TORQUE
FINAL TIME HIGH/LOW LIMIT Acceptance range to go from 1ST TORQUE
STANDARD
Page 6-10
step fastening will be used primarily for joints that have a requirement to synchronize
with another spindle during the incremental stages of the rundown to crush/compress a
gasket or grommet or for special joint conditioning (valve cover, oil pan, or body assembly, for
Angle control commences at SNUG TORQUE. All angle values are referenced from this point.
Once SPEED CHANGE TORQUE is reached or FREERUN REVOLUTIONS expires, the system will
switch from FREERUN SPEED to SLOWDOWN SPEED and continue to fasten to 1ST
The system will fasten to the 1ST TORQUE/ANGLE value during the specified 1ST TIME. 1ST
TORQUE/ANGLE must be reached within the 1ST TIME limits or a reject will occur.
Upon reaching 1ST TORQUE/ANGLE, 1ST TIME ends and FINAL TIME begins. 1ST
TORQUE/ANGLE is the shift point to TORQUE SPEED and the synchronization point prior to co
13 for Sync. info)
.
e system will fasten to CROSSOVER TORQUE/ANGLE, synchronize with other spindles
n fasten to STANDARD ANGLE using TORQUE SPEED during FINAL TIME.
STANDARD ANGLE must be reached within the FINAL TIME limits or a reject will occur.
rming multiple step Angle control fastening, the rotation Angle
should be performed as one continuous operation. There should be no intermediate
stop / synchronization points once Snug Torque has been sensed and rotation angle is
special conditions multiple steps can be performed using i
termediate Torque or Angle stop/synchronization points.
RECOMMENDATION / COMMENT
% of SNUG TORQUE
Start point of 1
st
torque rate monitoring (section 6.2)
% of SNUG TORQUE
Used for RATE/TIME settings and TORQUE SPEED initiation.
Angle Control Start Point
Start point of 3
RD
torque rate monitoring (section 6.2)
Synchronization point for 3rd Step
Engineered product fastening specification
Acceptance range to reach 1ST TORQUE/ANGLE setting
Acceptance range to go from 1ST TORQUE/ANGLE to
STANDARD ANGLE
step fastening will be used primarily for joints that have a requirement to synchronize
ss a
gasket or grommet or for special joint conditioning (valve cover, oil pan, or body assembly, for
Angle control commences at SNUG TORQUE. All angle values are referenced from this point.
LUTIONS expires, the system will
The system will fasten to the 1ST TORQUE/ANGLE value during the specified 1ST TIME. 1ST
and the synchronization point prior to com-
e system will fasten to CROSSOVER TORQUE/ANGLE, synchronize with other spindles
n fasten to STANDARD ANGLE using TORQUE SPEED during FINAL TIME.
STANDARD ANGLE must be reached within the FINAL TIME limits or a reject will occur.
rming multiple step Angle control fastening, the rotation Angle
should be performed as one continuous operation. There should be no intermediate
stop / synchronization points once Snug Torque has been sensed and rotation angle is
special conditions multiple steps can be performed using in-
Used for RATE/TIME settings and TORQUE SPEED initiation.
setting
to