Electromagnetic interference – Echelon Series 6000 Chip databook User Manual
Page 92
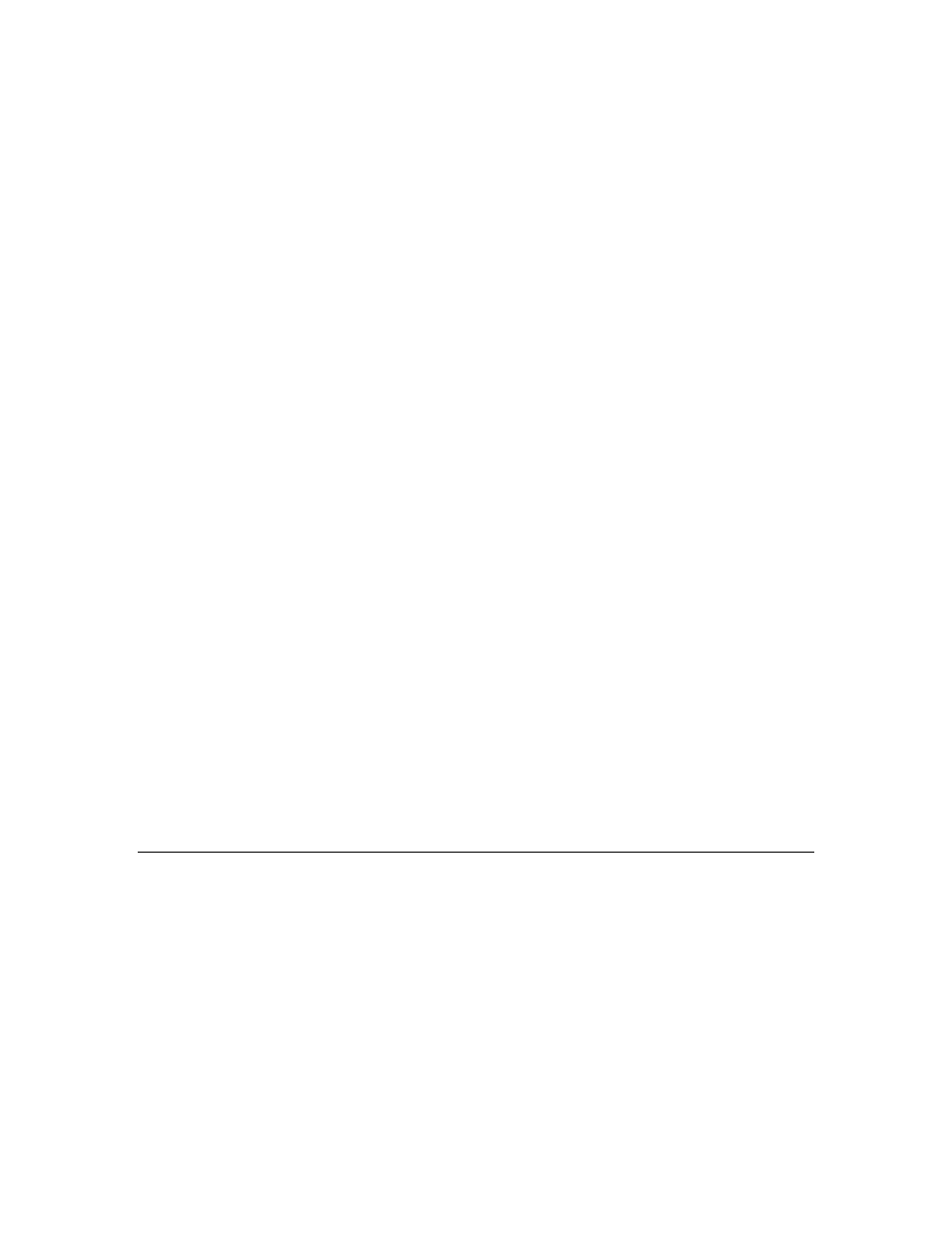
between electrically charged objects at different voltage potentials (one of which can be
ground). The most common form of ESD is an electric spark, but not all ESD hits are
accompanied by a spark.
A reliable system design must consider the effects of ESD, and take steps to protect sensitive
components. Static discharges occur frequently in low-humidity environments when human
operators touch electronic equipment. Keyboards, connectors, and enclosures can also
provide paths for static discharges to reach ESD-sensitive components. In addition, the
European Community has adopted requirements for ESD testing.
There are two general approaches to minimizing the effects of ESD for an electronic product:
•
Seal the product to prevent static discharges from reaching sensitive circuits inside
the package.
•
Design the grounding of the product so that ESD hits to user-accessible metal parts
can be shunted around sensitive circuitry.
Because a L
ON
W
ORKS
network connector is likely to be user-accessible, it is generally not
possible to seal Series 6000 devices completely. However, the product’s package should be
designed to minimize the possibility of an ESD hit arcing into the device’s circuit board. If
the product's package is made of plastic, then the PCB should be supported within the
package so that unprotected circuitry on the PCB is not adjacent to any seams in the
package. The PCB should not touch the plastic of an enclosure near a seam, because a static
discharge can creep along the surface of the plastic, through the seam, and arc onto the PCB.
After an ESD hit arcs into the product, the current from the discharge flows through all
possible paths back to Earth ground. The grounding of the PCB, and the protection of user-
accessible circuitry, must allow these ESD return currents to flow back to Earth ground
without disrupting normal circuit operation of the Series 6000 chip, its host microprocessor
(if any), or other device circuitry. Generally, this means that you should ensure that the
ESD currents are shunted to the center of a star ground configuration (as described in
Achieving High Immunity), and then out to the product’s chassis or Earth ground connection.
If the device floats with respect to Earth ground, the ESD current can return capacitively to
Earth by the network wire, the power supply wires, and the PCB ground plane.
Testing for ESD to comply with the EN 61000-4-2 ESD immunity test standard is performed
on a metal test table using an ESD transient generator. Level 4 testing involves injecting up
to ±8 kV contact discharges and up to ±15 kV air discharges into the product under test.
Depending on the product design, you can inject the discharges at the network connector,
power connector, or other user-accessible areas. During the test, the device should continue
to operate normally, with occasional packet loss due to the ESD hits.
Electromagnetic Interference
The high-speed digital signals that are associated with microcontroller designs can generate
unintentional electromagnetic interference (EMI). This interference is emitted by electrical
circuits that carry rapidly changing signals that generate RF currents that can cause
unwanted signals to be induced in other circuits. These unwanted signals can interrupt or
degrade the effective performance of those other circuits.
Products that use an FT 6000 Smart Transceiver or Neuron 6000 Processor will generally
need to demonstrate compliance with EMI limits enforced by various regulatory agencies. In
the USA, the Federal Communications Commission (FCC) requires that industrial products
comply with Title 47 of the Code of Federal Regulations (CFR) Part 15, Subpart A, and it
requires that products which can be used in residential environments comply with Subpart
80
Design and Test for Electromagnetic Compatibility