Modbus – IAI America ROBO Cylinder Series User Manual
Page 260
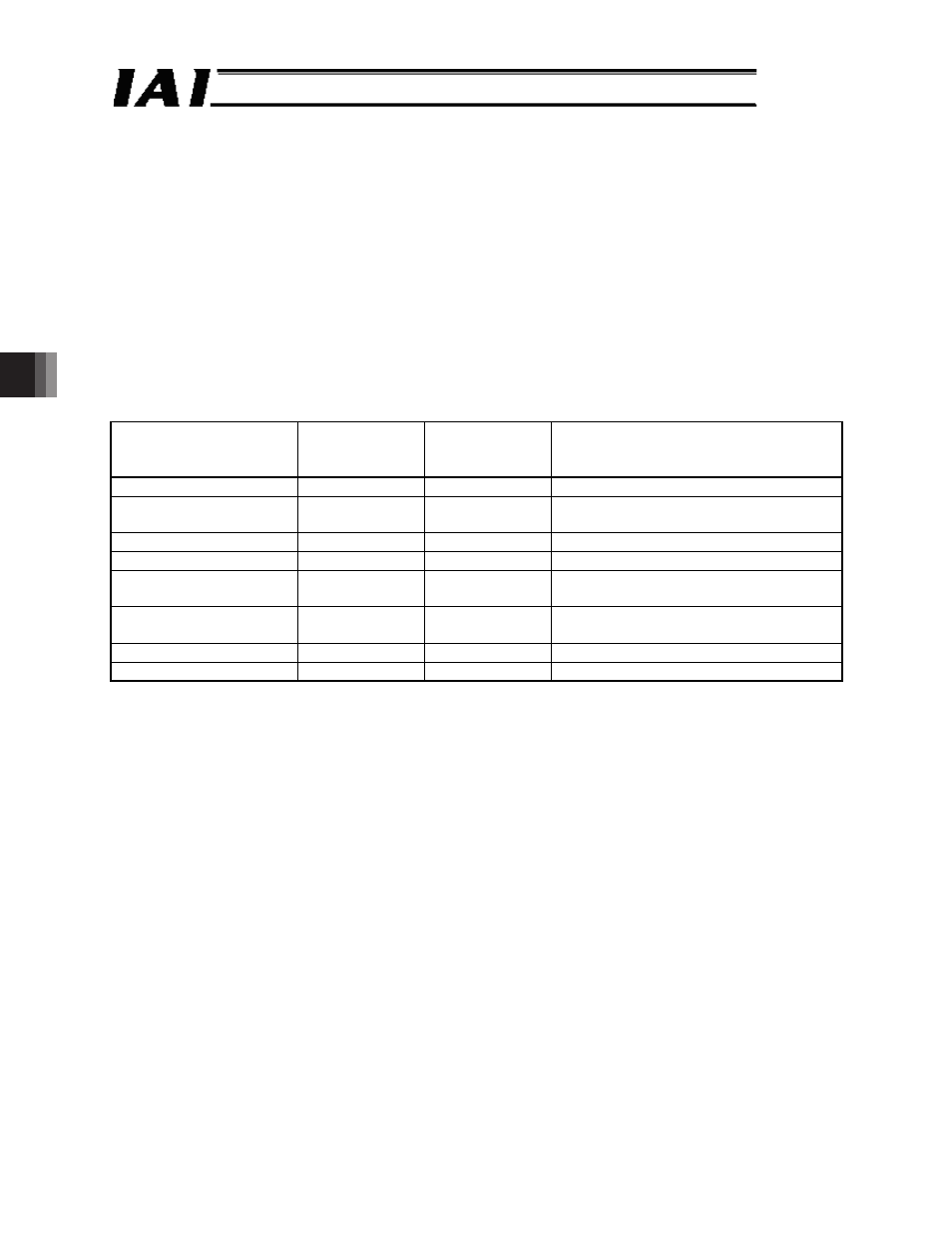
6. Modbus
ASCII
252
Modbus
6.5.8 Positioning Start Command <
(1) Function
If the rising edge of the positioning start command is detected (the data is first set to FF00
H
and then
changed to 0000
H
), the actuator will move to the position specified by the position number stored in
the position number specification register (POSR:0D03
H
). If nothing is done after the position start
command (FF00
H
is read and no new data is written), a position complete will not be output even
when the actuator enters the positioning band (write 0000
H
and restore the normal status).
If this command is executed when home return has never been performed after the power is turned
on (when the HEND bit is 0), the actuator will perform home return and then start moving to the
target position.
* The target position, speed and all other operation parameters must be set in the position table
(nonvolatile memory) of the controller in advance.
(2) Query format
Field
Number of
characters
ASCII mode
character string
(fixed)
Remarks
Header
1
‘:’
Slave address [H]
2
Arbitrary
Axis number + 1 (01
H
to 10
H
)
00
H
when broadcast is specified
Function code [H]
2
‘0’, ‘5’
Write to a single coil DO.
Start address [H]
4
‘0’, ‘4’ ‘0’, ‘C’
Positioning start command
Changed data [H]
4
Arbitrary
Positioning start command: ‘F’, ‘F’, ‘0’, ‘0’
Normal: ‘0’, ‘0’, ‘0’, ‘0’
Error check [H]
2
LRC calculation
result
Trailer
2
‘CR’, ‘LF’
Total number of bytes
17
(3) Response
If the change is successful, the response message will be the same as the query.
If invalid data is sent, an exception response (refer to section 7) will be returned, or no response will
be returned.