Modbus – IAI America ROBO Cylinder Series User Manual
Page 150
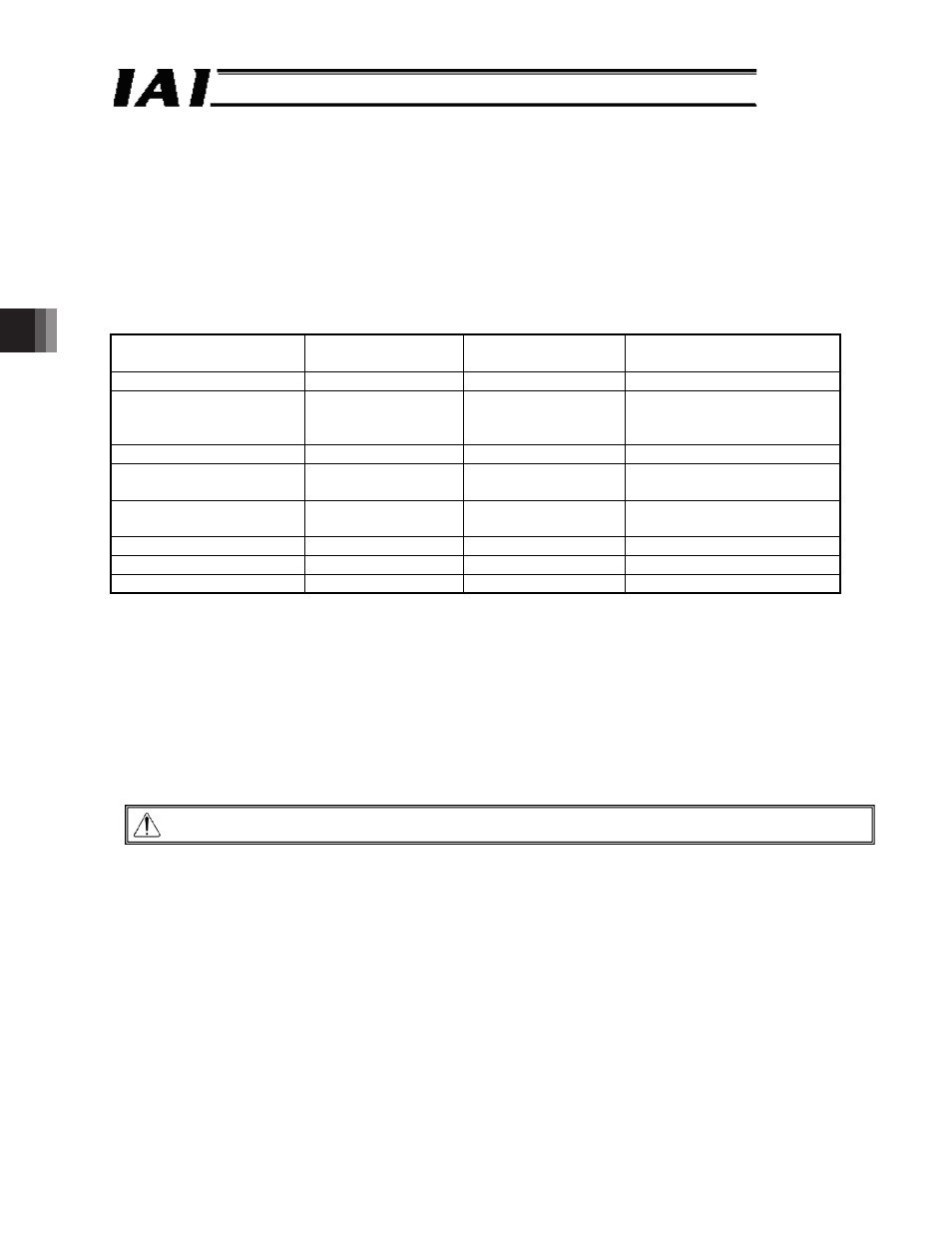
5. Modbus RTU
142
Modbus
5.4.15 Load Cell Calibration Command <
connected.
(1) Function --- SCON-CA only
The dedicated load cell is calibrated.
The factory setting of your load cell is that the ON status corresponds to a no-load state. If you
want to define the reference state as a condition where a work part (load) is installed, calibrate
the load cell.
Also calibrate the load cell in other situations as necessary (readjustment, inspection, etc.).
(2) Query format
Field
Number of data items
(number of bytes)
RTU mode
8-bit data
Remarks
Start
None
Silent interval
Slave address [H]
1
Arbitrary
Axis number + 1 (01
H
to 10
H
)
00
H
when broadcast is
specified
Function code [H]
1
05
Write to a single coil DO
Start address [H]
2
0426
Load cell calibration
command
Changed data [H]
2
Arbitrary
Calibration command: FF00
H
Normal operation: 0000
H
Error check [H]
2
CRC (16 bits)
End
None
Silent interval
Total number of bytes
8
(3) Calibration procedure
[1] Stop the actuator operation. (The load cell cannot be calibrated while the actuator is
performing any axis operation or push-motion operation or being paused, in which case 0E1
(load cell calibration error) alarm generates.)
[2] Turn this signal ON and keep it ON for at least 20 ms.
[3] When the calibration is complete, the calibration complete signal (CEND of device status
register 1 explained in 4.3.2 (12)) turns ON. After confirming that the CEND has turned ON,
turn OFF the CLBR.
If the calibration was unsuccessful, a 0E1 (load cell calibration error) alarm generates.
Caution: Normal operation commands are not accepted while the CLBR is ON.