1 overview, Modbus 1 overview – IAI America ROBO Cylinder Series User Manual
Page 21
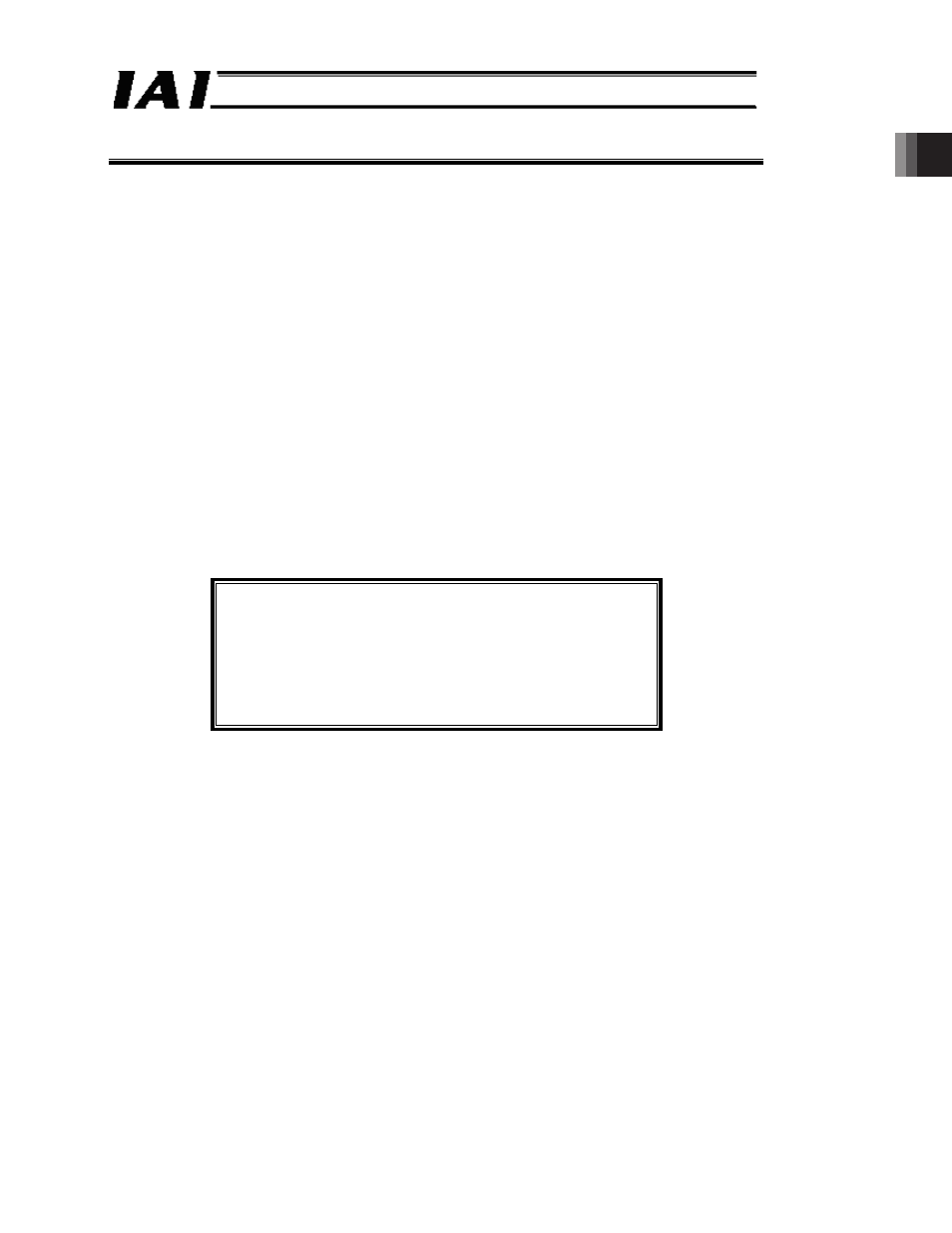
1. Overview
13
Modbus
1 Overview
The ROBO Cylinder Controller (hereinafter referred to as RC controller) is equipped with a
serial bus interface for asynchronous communication conforming to the EIA RS485 standard.
This interface allows the RC controller to communicate with the host (host controller). In this
way, it is possible to build an SIO link system that can connect and control up to 16 axes of
slaves (RC controllers) (
Note
1).
In addition to sending commands to each axis individually, it is also possible to broadcast the
same command to all slaves at the same time.
Modbus Protocol is employed as the communication protocol, and it is possible to send
commands from a host as well as read internal information.
Since the specifications of Modbus Protocol are disclosed globally, software development can
be carried out easily.
(Note 1) Note that it is only possible to connect RC series devices on the same network; old RC series
(protocol T) or other devices cannot be connected.
There are 2 types of serial transmission modes: ASCII mode (where 1-byte (8 bits) data is
Converted to ASCII code (2 characters) and sent) and RTU mode (where 1-byte (8 bits) data is
sent as is). RC controllers identify the transmission mode on a packet-by-packet basis, thus
making it possible to receive in both modes
(
Note 2
)
.
Set the ROBONET RS485 to the SIO through mode. [Refer to the separate ROBONET
Operation Manual.]
(Note 2) Make sure to use the same serial transmission mode for all devices on one network: it is not
allowed to use both modes.
Controllable controllers
x
ERC2 (SE) / ERC3*
x
PCON-C / CA* / CFA* / CG / CF / CY / SE / PL / PO
x
ACON-C / CG / CY / SE / PL / PO
x
SCON-C / CA
x
ROBONET_RS485 (SIO through mode)
* V0002 or later